1. Хуткасць рэзкі
Многія кліенты ў кансультацыі па лазернай рэжучай машыне спытаюць, наколькі хутка лазерная машына можа выразаць. Сапраўды, лазерная машына для выразання - гэта высокаэфектыўная абсталяванне, а хуткасць рэзкі, натуральна, з'яўляецца асноўнай увагай кліента. Але самая хуткая хуткасць рэзкі не вызначае якасць лазернай рэзкі.
Занадта хуткі тЁн скарачаючы хуткасць
a. Не магу прарэзаць матэрыял
нар. Нарэзаная паверхня ўяўляе сабой касу
c. Шурпаты пярэдні край
Занадта павольна хуткасць рэзкі
a. Над станам плаўлення з шурпатай рэжучай паверхняй
нар. Шырэйшая разрэзаная шчыліна і востры кут растаюць у закругленыя куты
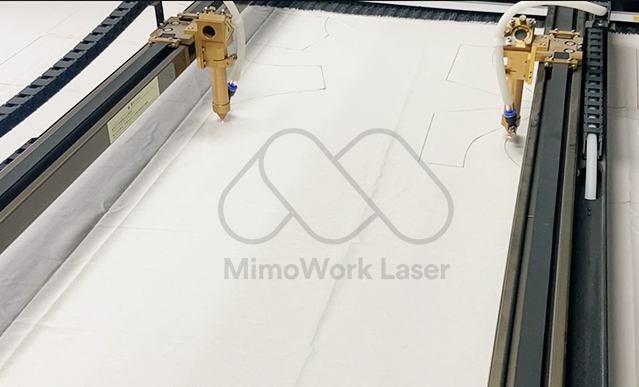
Каб зрабіць абсталяванне для лазернага рэжучага машыны лепш гуляць у яе рэжучую функцыю, не проста пытайцеся, наколькі хутка лазерная машына можа выразаць, адказ часта недакладны. Наадварот, забяспечце MimoWork спецыфікацыю вашага матэрыялу, і мы дамо вам больш адказны адказ.
2. Фокус -пункт
Паколькі шчыльнасць лазернай магутнасці аказвае вялікі ўплыў на хуткасць рэзкі, выбар фокуснай адлегласці лінзаў з'яўляецца важным момантам. Памер лазернага пляма пасля факусоўкі лазернага прамяня прапарцыйны фокуснай даўжыні аб'ектыва. Пасля таго, як лазерны прамень сканцэнтраваны на аб'ектыве з кароткай фокуснай адлегласцю, памер лазернай плямы вельмі невялікі, а шчыльнасць магутнасці ў фокуснай кропцы вельмі высокі, што выгадна для рэзкі матэрыялаў. Але яго недахоп заключаецца ў тым, што пры кароткай глыбіні фокусу толькі невялікая дапамога на карэкціроўку для таўшчыні матэрыялу. Увогуле, фокусную лінзу з кароткай фокуснай даўжынёй больш падыходзіць для хуткаснага рэзання тонкага матэрыялу. А ў фокуснай лінзе з доўгай фокуснай адлегласцю ёсць шырокая фокусная глыбіня, пакуль яна мае дастатковую шчыльнасць магутнасці, ён больш падыходзіць для выразання тоўстых нарыхтовак, такіх як пена, акрыл і дрэва.
Пасля вызначэння, якую фокусную даўжыню трэба выкарыстоўваць, адноснае становішча фокуснай кропкі паверхні нарыхтоўкі вельмі важна, каб забяспечыць якасць рэзкі. З -за самай высокай шчыльнасці магутнасці ў фокусе, у большасці выпадкаў каардынацыйны цэнтр знаходзіцца на або крыху ніжэй паверхні нарыхтоўкі пры рэзанні. У цэлым працэсе рэзкі важная ўмова, каб забяспечыць адноснае становішча фокусу і нарыхтоўкі пастаяннай для атрымання стабільнай якасці рэзкі.
3. Сістэма выбуху паветра і дапаможны газ
Увогуле, матэрыяльная лазерная рэзка патрабуе выкарыстання дапаможнага газу, у асноўным звязанага з тыпам і ціскам дапаможнага газу. Звычайна дапаможны газ выкідваецца кааксіяльна лазерным прамянём, каб абараніць аб'ектыў ад забруджвання і выдзімае дзындра ў ніжняй частцы рэжучай плошчы. Для неметалічных матэрыялаў і некаторых металічных матэрыялаў для выдалення расплаўленых і выпараных матэрыялаў выкарыстоўваецца сціснуты паветра або інертны газ, прытрымліваючы залішняга гарэння ў рэжучай зоне.
У перадумове забеспячэння дапаможнага газу, ціск газу з'яўляецца надзвычай важным фактарам. Пры разрэзе тонкага матэрыялу з высокай хуткасцю патрабуецца высокі ціск газу, каб прадухіліць прыліпанне дзындраў да задняй часткі разрэзу (гарачы дзындр пашкодзіць зрэзаны край, калі ён трапляе ў нарыхтоўку). Калі таўшчыня матэрыялу павялічваецца альбо хуткасць рэзкі павольная, ціск газу павінна быць належным чынам зніжана.
4. Хуткасць разважанняў
Даўжыня хвалі лазера CO2 складае 10,6 мкм, што выдатна падыходзіць для паглынання неметалічных матэрыялаў. Але лазер CO2 не падыходзіць для металічнай рэзкі, асабліва металічнага матэрыялу з высокімі адлюстраваннямі, такімі як золата, срэбра, медзь і алюмініевы метал і г.д.
Хуткасць паглынання матэрыялу да прамяня гуляе важную ролю ў пачатковай стадыі нагрэву, але як толькі ўтвараецца рэжучая адтуліна ўнутры нарыхтоўкі, эфект адтуліны чорнага цела робіць хуткасць паглынання матэрыялу да прамяня блізкасці закрыта да 100%.
Павярхоўны стан матэрыялу непасрэдна ўплывае на паглынанне прамяня, асабліва шурпатасць паверхні, і пласт павярхоўнага аксіду прывядзе да відавочных змяненняў у хуткасці паглынання паверхні. У практыцы лазернай рэзкі часам рэжучыя характарыстыкі матэрыялу могуць быць палепшаны шляхам уплыву стану паверхні матэрыялу на хуткасць паглынання прамяня.
5. Лазерная галава сопла
Калі асадка няправільна адабрана альбо дрэнна падтрымліваецца, лёгка прычыніць забруджванне або пашкоджанне, альбо з -за дрэннай круглую рот сопла або мясцовай закаркаванні, выкліканай гарачым металічным пырскам, віхравыя токі будуць утвораны ў сопла, што прыводзіць да значна Горш прадукцыйнасць рэзкі. Часам рот сопла не адпавядае мэтанакіраванага прамяня, утвараючы прамень, каб зрушыць край сопла, што таксама паўплывае на якасць рэзкі краю, павялічыць шырыню шчыліны і зрабіць вывіх памеру рэзкі.
Для асадкі трэба звярнуць на два пытанні асаблівую ўвагу
a. Уплыў дыяметра сопла.
нар. Уплыў адлегласці паміж асадкай і паверхняй нарыхтоўкі.
6. Аптычны шлях
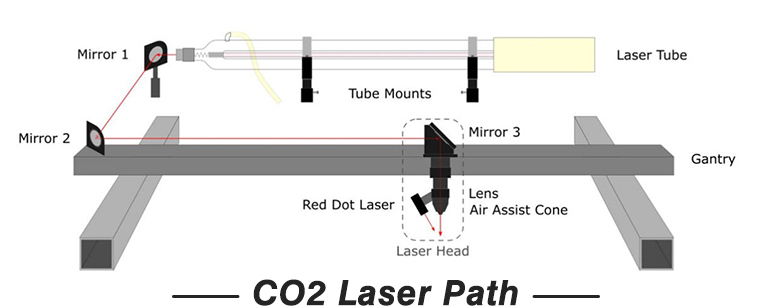
Арыгінальны прамень, які выпраменьваецца лазерам, перадаецца (уключаючы адлюстраванне і перадачу) праз сістэму знешняга аптычнага шляху, і дакладна асвятляе паверхню нарыхтоўкі з вельмі высокай шчыльнасцю.
Аптычныя элементы сістэмы знешняга аптычнага шляху павінны рэгулярна правяраць і карэктавацца своечасова, каб пераканацца, што, калі паходня праходзіць над нарыхтоўкай, светлы прамень правільна перадаецца ў цэнтр аб'ектыва і сканцэнтраваны ў невялікім месцы для выразання нарыхтоўка з высокай якасцю. Пасля таго, як становішча любога аптычнага элемента змяняецца альбо забруджана, на якасць рэзкі будзе закрануты, і нават рэзка не можа быць праведзена.
Знешні аптычны аб'ектыў шляху забруджваецца прымешкамі ў паветраным патоку і звязаны пры пырсканні часціц у рэжучай зоне, альбо лінза недастаткова астуджаецца, што прывядзе да перагрэву аб'ектыва і паўплываць на перадачу энергіі прамяня. Гэта выклікае калімацыю аптычнага шляху да дрэйфу і прыводзіць да сур'ёзных наступстваў. Перагрэў лінзаў таксама прывядзе да фокуснага скажэння і нават паставіць пад пагрозу саму аб'ектыў.
Даведайцеся больш пра тыпы і цэны на лазерныя разрэзы CO2
Час паведамлення: верасня 20-2022