Lazerių naudojimas automobilių gamybos pramonėje
Nuo tada, kai 1913 m. Henry Fordas pristatė pirmąją surinkimo liniją automobilių gamybos pramonėje, automobilių gamintojai nuolat stengėsi optimizuoti savo procesus, siekdami galutinio tikslo – sumažinti surinkimo laiką, sumažinti išlaidas ir padidinti pelną. Šiuolaikinė automobilių gamyba yra labai automatizuota, o robotai tapo įprasti visoje pramonėje. Dabar į šį procesą integruojama lazerinė technologija, pakeičianti tradicinius įrankius ir suteikianti daug papildomų privalumų gamybos procesui.

Automobilių gamybos pramonėje naudojamos įvairios medžiagos, įskaitant plastiką, tekstilę, stiklą ir gumą, kurios visos gali būti sėkmingai apdorojamos naudojant lazerius. Tiesą sakant, lazeriu apdoroti komponentai ir medžiagos yra beveik visose tipiškos transporto priemonės vietose, tiek viduje, tiek išorėje. Lazeriai taikomi įvairiuose automobilio gamybos proceso etapuose – nuo projektavimo ir kūrimo iki galutinio surinkimo. Lazerinės technologijos neapsiriboja masine gamyba ir netgi randa pritaikymą aukščiausios klasės automobilių gamyboje pagal užsakymą, kur gamybos apimtys yra palyginti mažos, o tam tikri procesai vis dar reikalauja rankų darbo. Čia siekiama ne plėsti ar paspartinti gamybą, o pagerinti apdorojimo kokybę, pakartojamumą ir patikimumą, taip sumažinant atliekas ir brangiai kainuojantį netinkamą medžiagų naudojimą.
Lazeris: plastikinių dalių apdorojimo jėgainė

TPlačiausias lazerių panaudojimas yra plastikinių dalių apdirbimas. Tai apima vidaus ir prietaisų skydelio plokštes, stulpelius, buferius, spoierius, apdailas, valstybinius numerius ir šviesų korpusus. Automobilių komponentai gali būti gaminami iš įvairių plastikų, tokių kaip ABS, TPO, polipropilenas, polikarbonatas, HDPE, akrilas, taip pat iš įvairių kompozitų ir laminatų. Plastikas gali būti eksponuojamas arba dažomas ir gali būti derinamas su kitomis medžiagomis, pvz., audiniu dengtais vidiniais statramsčiais arba atraminėmis konstrukcijomis, užpildytomis anglies ar stiklo pluoštu, kad būtų padidintas stiprumas. Lazeriais galima išpjauti arba išgręžti skylutes tvirtinimo taškams, šviesoms, jungikliams, parkavimosi jutikliams.
Permatomus plastikinius žibintų korpusus ir lęšius dažnai reikia apipjaustyti lazeriu, kad būtų pašalintos po įpurškimo likusios atliekos. Lempų dalys dažniausiai gaminamos iš polikarbonato dėl optinio skaidrumo, didelio atsparumo smūgiams, atsparumo oro sąlygoms ir atsparumo UV spinduliams. Nors apdorojant lazeriu šio konkretaus plastiko paviršius gali būti šiurkštus, visiškai sumontavus priekinį žibintą lazeriu nupjautų kraštų nesimato. Daugelį kitų plastikų galima pjauti itin kokybiškai, todėl paliekami švarūs kraštai, kurių nereikia valyti po apdorojimo ar keisti.
Lazerio magija: operacijų ribų laužymas
Lazerinės operacijos gali būti atliekamos tose vietose, kurios yra neprieinamos tradiciniams įrankiams. Kadangi pjovimas lazeriu yra nekontaktinis procesas, įrankis nesusidėvi ar nelūžta, o lazeriams reikia minimalios priežiūros, todėl prastovos laikas yra minimalus. Operatoriaus saugumas užtikrinamas, nes visas procesas vyksta uždaroje erdvėje, todėl vartotojo įsikišimo nereikia. Nėra judančių peilių, todėl pašalinami susiję saugos pavojai.

Plastiko pjovimo operacijas galima atlikti naudojant lazerius, kurių galia svyruoja nuo 125 W iki didesnės, priklausomai nuo laiko, reikalingo užduočiai atlikti. Daugumos plastikų atveju ryšys tarp lazerio galios ir apdorojimo greičio yra tiesinis, o tai reiškia, kad norint padvigubinti pjovimo greitį, reikia padvigubinti lazerio galią. Vertinant bendrą operacijų ciklo laiką, taip pat reikia atsižvelgti į apdorojimo laiką, kad būtų galima tinkamai parinkti lazerio galią.
Be pjovimo ir apdailos: padidinkite lazerio plastiko apdorojimo galią

Lazerinis pritaikymas plastiko apdirbimui neapsiriboja vien pjovimu ir apipjaustymu. Tiesą sakant, ta pati lazerinio pjovimo technologija gali būti naudojama paviršiaus modifikavimui arba dažų pašalinimui iš tam tikrų plastikinių ar kompozitinių medžiagų vietų. Kai dalis su dažytu paviršiumi reikia klijuoti klijais, dažnai reikia nuimti viršutinį dažų sluoksnį arba šiurkštinti paviršių, kad būtų užtikrintas geras sukibimas. Tokiais atvejais lazeriai naudojami kartu su galvanometriniais skaitytuvais, kad lazerio spindulį būtų galima greitai praleisti per reikiamą plotą, suteikiant pakankamai energijos paviršiui pašalinti nepažeidžiant birių medžiagų. Galima lengvai pasiekti tikslią geometriją, o pašalinimo gylį ir paviršiaus tekstūrą galima valdyti, todėl prireikus galima lengvai keisti pašalinimo modelį.
Žinoma, automobiliai nėra vien tik iš plastiko, o lazeriais galima pjauti ir kitas automobilių gamyboje naudojamas medžiagas. Automobilių interjere dažniausiai naudojamos įvairios tekstilės medžiagos, iš kurių ryškiausias yra apmušalų audinys. Pjovimo greitis priklauso nuo audinio tipo ir storio, tačiau didesnės galios lazeriai pjauna atitinkamai didesniu greičiu. Dauguma sintetinių audinių gali būti švariai iškirpti, su sandariais kraštais, kad nesusidėvėtų vėlesnio automobilio sėdynių susiuvimo ir surinkimo metu.
Natūrali oda ir sintetinė oda taip pat gali būti pjaustomos taip pat, kaip ir automobilių interjero medžiagoms. Audinių dangos, dažnai matomos ant daugelio plataus vartojimo transporto priemonių vidaus atramų, taip pat dažnai yra tiksliai apdorojamos naudojant lazerius. Įpurškimo proceso metu audinys sujungiamas su šiomis dalimis, o audinio perteklių reikia pašalinti nuo kraštų prieš montuojant į transporto priemonę. Tai taip pat yra 5 ašių robotizuotas apdirbimo procesas, kai pjovimo galvutė seka detalės kontūrus ir tiksliai apipjausto audinį. Tokiais atvejais dažniausiai naudojami Luxinar SR ir OEM serijos lazeriai.
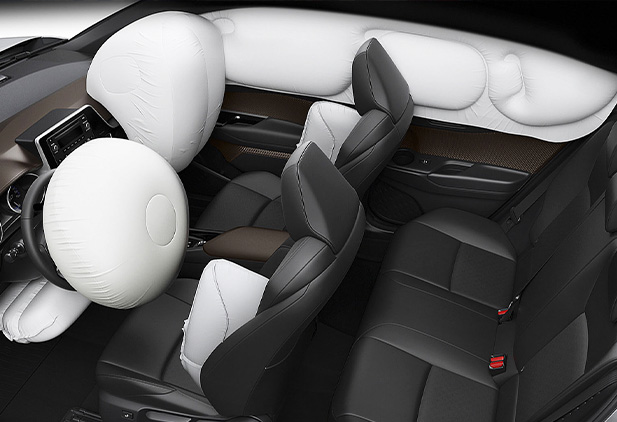
Lazerio pranašumai automobilių gamyboje
Lazerinis apdorojimas automobilių gamybos pramonėje suteikia daug privalumų. Lazerinis apdorojimas ne tik užtikrina pastovią kokybę ir patikimumą, bet ir yra labai lankstus ir pritaikomas įvairiems komponentams, medžiagoms ir procesams, naudojamiems automobilių gamyboje. Lazerinė technologija leidžia pjauti, gręžti, žymėti, suvirinti, rašyti ir abliuoti. Kitaip tariant, lazerių technologija yra labai universali ir atlieka gyvybiškai svarbų vaidmenį skatinant nuolatinį automobilių pramonės vystymąsi.
Automobilių pramonei toliau tobulėjant, automobilių gamintojai randa naujų būdų panaudoti lazerines technologijas. Šiuo metu pramonė iš esmės pereina prie elektrinių ir hibridinių transporto priemonių, įvedant „elektrinio mobilumo“ sąvoką, tradicinius vidaus degimo variklius pakeičiant elektrine pavaros technologija. Tam reikia, kad gamintojai priimtų daug naujų komponentų ir gamybos procesų
▶ Norite pradėti iš karto?
Ką apie šias puikias galimybes?
Kyla sunkumų pradedant?
Susisiekite su mumis dėl išsamaus klientų aptarnavimo!
▶ Apie mus – MimoWork Laser
Nei mes, nei jūs netenkiname už vidutiniškus rezultatus
„Mimowork“ yra į rezultatus orientuotas lazerių gamintojas, įsikūręs Šanchajuje ir Dongguane Kinijoje, teikiantis 20 metų gilią eksploatavimo patirtį gaminant lazerines sistemas ir siūlantis išsamius apdorojimo ir gamybos sprendimus MVĮ (mažoms ir vidutinėms įmonėms) įvairiose pramonės šakose. .
Mūsų turtinga lazerinių sprendimų, skirtų metalo ir nemetalinių medžiagų apdirbimui, patirtis yra giliai įsišaknijusi pasaulinės reklamos, automobilių ir aviacijos, metalo gaminių, dažų sublimacijos, audinių ir tekstilės pramonėje.
Užuot siūlęs neapibrėžtą sprendimą, kurį reikia pirkti iš nekvalifikuotų gamintojų, „MimoWork“ kontroliuoja kiekvieną gamybos grandinės dalį, siekdama užtikrinti, kad mūsų produktai veiktų nuolat.

„MimoWork“ įsipareigojo kurti ir atnaujinti lazerių gamybą ir sukūrė dešimtis pažangių lazerinių technologijų, kad dar labiau pagerintų klientų gamybos pajėgumus ir padidintų efektyvumą. Įgydami daugybę lazerinių technologijų patentų, visada koncentruojamės į lazerinių mašinų sistemų kokybę ir saugą, siekdami užtikrinti nuoseklią ir patikimą apdirbimo gamybą. Lazerio mašinos kokybė yra sertifikuota CE ir FDA.
Gaukite daugiau idėjų iš mūsų „YouTube“ kanalo
Pjovimo lazeriu paslaptis?
Susisiekite su mumis dėl išsamių vadovų
Paskelbimo laikas: 2023-07-13