Wat is laserslassen? Laserslassen uitgelegd! Alles wat u moet weten over laserslassen, inclusief belangrijk principe en hoofdprocesparameters!
Veel klanten begrijpen de fundamentele werkprincipes van laserlasapparaat niet, laat staan om de juiste laserlasmachine te kiezen, maar mimowork laser is er om u te helpen de juiste beslissing te nemen en extra ondersteuning te bieden om u te helpen bij het begrijpen van laserlassen.
Wat is laserslassen?
Laserslassen is een type smeltende lassen, met behulp van de laserstraal als een laswarmingsbron, het lasprincipe is via een specifieke methode om het actieve medium te stimuleren, waardoor resonerende holtecillatie wordt gevormd en vervolgens transformeren in de gestimuleerde stralingsbalk, wanneer de bundel En het werkstuk neemt contact op met elkaar, de energie wordt geabsorbeerd door het werkstuk, wanneer de temperatuur het smeltpunt van het materiaal bereikt, kan worden gelast.
Volgens het belangrijkste mechanisme van het laspool heeft laserslassen twee basislassenmechanismen: lassen van warmtegeleiding en diepe penetratie (sleutelgat) lassen. De warmte die wordt gegenereerd door laslassen van warmtegeleiding is verspreid naar het werkstuk door warmteoverdracht, zodat het lasoppervlak is gesmolten, er zou geen verdamping moeten plaatsvinden, wat vaak wordt gebruikt bij het lassen van dunne componenten met lage snelheid. Diep fusielassen verdampt het materiaal en vormt een grote hoeveelheid plasma. Vanwege verhoogde warmte zullen er gaten aan de voorkant van het gesmolten zwembad zijn. Diepe penetratielassen is de meest gebruikte laserslasmodus, het kan het werkstuk grondig lassen, en de invoersenergie is enorm, wat leidt tot snelle lassnelheid.
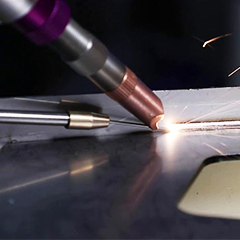
Procesparameters in laserslassen
Er zijn veel procesparameters die de kwaliteit van laserslassen beïnvloeden, zoals vermogensdichtheid, laserpulsgolfvorm, onscherpe, lassnelheid en de keuze van hulpschermgas.
Laserkrachtdichtheid
Power -dichtheid is een van de belangrijkste parameters bij laserverwerking. Met een hogere vermogensdichtheid kan de oppervlaktelaag worden verwarmd tot kookpunt binnen een microseconde, wat resulteert in een grote hoeveelheid verdamping. Daarom is de krachtige dichtheid voordelig voor materiaalverwijderingsprocessen zoals boren, snijden en graveren. Voor lage vermogensdichtheid duurt het verschillende milliseconden voordat de oppervlaktetemperatuur het kookpunt bereikt, en voordat het oppervlak verdampt, bereikt de bodem het smeltpunt, wat gemakkelijk is om een goede smeltlas te vormen. Daarom is het vermogensdichtheidsbereik in de vorm van warmtegeleiding laserlassen 104-106W/cm2.
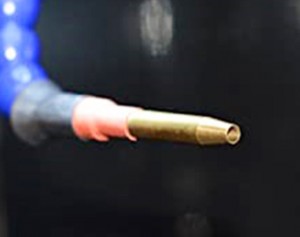
Laserpulsgolfvorm
Laserpulsgolfvorm is niet alleen een belangrijke parameter om materiaalverwijdering te onderscheiden van het smelten van materiaal, maar ook een belangrijke parameter om het volume en de kosten van verwerkingsapparatuur te bepalen. Wanneer de laserstraal met hoge intensiteit naar het oppervlak van het materiaal wordt neergeschoten, zal het oppervlak van het materiaal 60 ~ 90% van de laserergie hebben die wordt gereflecteerd en beschouwd als verlies, met name goud, zilver, koper, aluminium, titanium en andere materialen die hebben Sterke reflectie en snelle warmteoverdracht. De reflectie van een metaal varieert met de tijd tijdens een laserpuls. Wanneer de oppervlaktetemperatuur van het materiaal naar het smeltpunt stijgt, neemt de reflectie snel af en wanneer het oppervlak zich in de smeltstaat bevindt, stabiliseert de reflectie op een bepaalde waarde.
Laserpulsbreedte
Pulsbreedte is een belangrijke parameter van gepulseerd laserlassen. De pulsbreedte werd bepaald door de penetratiediepte en de met warmte aangetaste zone. Hoe langer de pulsbreedte was, hoe groter de door warmte aangetaste zone was, en de penetratiediepte nam toe met het 1/2 vermogen van de pulsbreedte. De toename van de pulsbreedte zal echter het piekvermogen verminderen, dus de toename van de pulsbreedte wordt in het algemeen gebruikt voor lassen van warmtegeleiding, wat resulteert in een brede en ondiepe lasgrootte, vooral geschikt voor laplassen van dunne en dikke platen. Lager piekvermogen resulteert echter in overtollige warmte -input en elk materiaal heeft een optimale pulsbreedte die de penetratiediepte maximaliseert.
Onschadder
Laserslassen vereist meestal een bepaalde hoeveelheid onfocus, omdat de vermogensdichtheid van het spotcentrum in de laserfocus te hoog is, wat gemakkelijk is om het lasmateriaal in gaten te verdampen. De verdeling van de vermogensdichtheid is relatief uniform in elk vlak weg van de laserfocus.
Er zijn twee defocusmodi:
Positieve en negatieve defocus. Als het brandvlak zich boven het werkstuk bevindt, is het een positieve defocus; Anders is het negatieve defocus. Volgens de geometrische optiektheorie is, wanneer de afstand tussen de positieve en negatieve defocuserende vlakken en het lasvlak gelijk is, de vermogensdichtheid op het overeenkomstige vlak ongeveer hetzelfde is, maar in feite is de verkregen gesmolten poolvorm anders. In het geval van negatieve defocus kan een grotere penetratie worden verkregen, wat verband houdt met het vormingsproces van gesmolten pool.
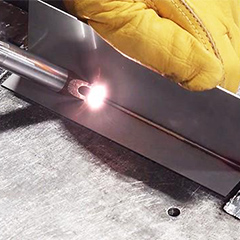
Lassnelheid
Lassnelheid bepaalt de kwaliteit van het lasoppervlak, penetratiediepte, door warmte aangetaste zone enzovoort. De lassnelheid heeft invloed op de warmte -ingang per tijdseenheid. Als de lassnelheid te langzaam is, is de warmte -ingang te hoog, wat resulteert in het doorbreken van het werkstuk. Als de lassnelheid te snel is, is de warmte -invoer te weinig, wat resulteert in het werkstuklassen gedeeltelijk en onafgemaakt. Het verminderen van de lassnelheid wordt meestal gebruikt om de penetratie te verbeteren.
Hulpblaasbeveiligingsgas
Hulpblaadbeveiligingsgas is een essentiële procedure bij laserlassen met hoog vermogen. Enerzijds, om te voorkomen dat metaalmaterialen sputteren en de focusgatspiegel verontreinigen; Aan de andere kant is het om te voorkomen dat het plasma dat in het lasproces wordt gegening te concentreren en te voorkomen dat de laser het oppervlak van het materiaal bereikt. Tijdens het proces van laserslassen worden helium, argon, stikstof en andere gassen vaak gebruikt om het gesmolten pool te beschermen, om te voorkomen dat het werkstuk van oxidatie in de lastechniek is. Factoren zoals het type beschermende gas, de grootte van de luchtstroom en de blaashoek hebben een grote impact op de lasresultaten en verschillende blaasmethoden hebben ook een zekere impact op de laskwaliteit.
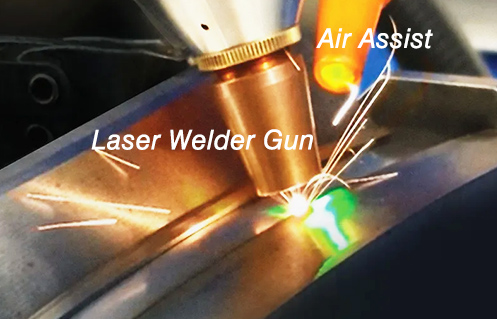
Onze aanbevolen draagbare laserlasser:
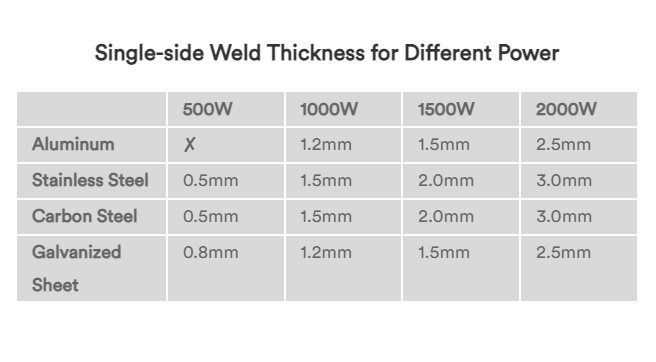
Laser Welder - Werkomgeving
◾ Temperatuurbereik van werkomgeving: 15 ~ 35 ℃
◾ Vochtigheidsbereik van de werkomgeving: <70%geen condensatie
◾ Koeling: waterkoeler is noodzakelijk vanwege de functie van het verwijderen van warmte voor laserwarmte-dissipatiecomponenten, waardoor de laserlasser goed loopt.
(Gedetailleerd gebruik en gids over Water Chiller, u kunt de:Freeze-proofing maatregelen voor CO2-lasersysteem)
Wil je meer weten over laserslassers?
Posttijd: december-22-2022