1. కట్టింగ్ వేగం
లేజర్ కట్టింగ్ మెషీన్ సంప్రదింపులలో చాలా మంది కస్టమర్లు లేజర్ యంత్రం ఎంత వేగంగా కత్తిరించగలదో అడుగుతారు. నిజమే, లేజర్ కట్టింగ్ మెషీన్ అత్యంత సమర్థవంతమైన పరికరాలు, మరియు కట్టింగ్ వేగం సహజంగానే కస్టమర్ ఆందోళన యొక్క కేంద్రంగా ఉంటుంది. కానీ వేగవంతమైన కట్టింగ్ వేగం లేజర్ కటింగ్ యొక్క నాణ్యతను నిర్వచించదు.
చాలా వేగంగా టిఅతను వేగం తగ్గించాడు
ఎ. పదార్థం ద్వారా కత్తిరించలేరు
బి. కట్టింగ్ ఉపరితలం వాలుగా ఉన్న ధాన్యాన్ని అందిస్తుంది, మరియు వర్క్పీస్ యొక్క దిగువ సగం ద్రవీభవన మరకలను ఉత్పత్తి చేస్తుంది
సి. కఠినమైన కట్టింగ్ ఎడ్జ్
కట్టింగ్ వేగం చాలా నెమ్మదిగా ఉంటుంది
ఎ. కఠినమైన కట్టింగ్ ఉపరితలంతో ద్రవీభవన స్థితిపై
బి. విస్తృత కట్టింగ్ గ్యాప్ మరియు పదునైన మూలలో గుండ్రని మూలలుగా కరిగించబడతాయి
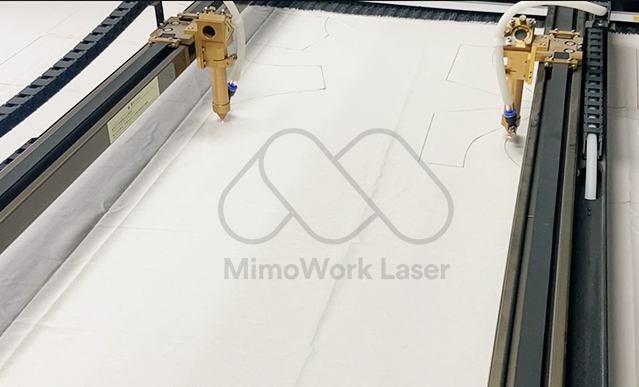
లేజర్ కట్టింగ్ మెషిన్ ఎక్విప్మెంట్ను దాని కట్టింగ్ ఫంక్షన్ను బాగా ఆడటానికి, లేజర్ మెషీన్ ఎంత వేగంగా కత్తిరించగలదో అడగవద్దు, సమాధానం తరచుగా సరికాదు. దీనికి విరుద్ధంగా, మీ పదార్థం యొక్క స్పెసిఫికేషన్తో మిమోవర్క్ను అందించండి మరియు మేము మీకు మరింత బాధ్యతాయుతమైన సమాధానం ఇస్తాము.
2. ఫోకస్ పాయింట్
లేజర్ శక్తి సాంద్రత కట్టింగ్ వేగంపై గొప్ప ప్రభావాన్ని కలిగి ఉన్నందున, లెన్స్ ఫోకల్ లెంగ్త్ ఎంపిక ఒక ముఖ్యమైన విషయం. లేజర్ బీమ్ ఫోకస్ చేసిన తర్వాత లేజర్ స్పాట్ పరిమాణం లెన్స్ యొక్క ఫోకల్ పొడవుకు అనులోమానుపాతంలో ఉంటుంది. లేజర్ పుంజం లెన్స్ ద్వారా చిన్న ఫోకల్ పొడవుతో కేంద్రీకృతమై ఉన్న తరువాత, లేజర్ స్పాట్ యొక్క పరిమాణం చాలా చిన్నది మరియు కేంద్ర బిందువు వద్ద శక్తి సాంద్రత చాలా ఎక్కువ, ఇది పదార్థ కోతకు ప్రయోజనకరంగా ఉంటుంది. కానీ దాని ప్రతికూలత ఏమిటంటే, చిన్న ఫోకస్ లోతుతో, పదార్థం యొక్క మందం కోసం ఒక చిన్న సర్దుబాటు భత్యం మాత్రమే. సాధారణంగా, చిన్న ఫోకల్ పొడవు కలిగిన ఫోకస్ లెన్స్ హై-స్పీడ్ కట్టింగ్ సన్నని పదార్థానికి మరింత అనుకూలంగా ఉంటుంది. మరియు పొడవైన ఫోకల్ పొడవుతో ఫోకస్ లెన్స్ విస్తృత ఫోకల్ లోతును కలిగి ఉంటుంది, దీనికి తగినంత శక్తి సాంద్రత ఉన్నంతవరకు, నురుగు, యాక్రిలిక్ మరియు కలప వంటి మందపాటి వర్క్పీస్లను కత్తిరించడానికి ఇది మరింత అనుకూలంగా ఉంటుంది.
ఏ ఫోకల్ పొడవు లెన్స్ను ఉపయోగించాలో నిర్ణయించిన తరువాత, కట్టింగ్ నాణ్యతను నిర్ధారించడానికి వర్క్పీస్ ఉపరితలానికి ఫోకల్ పాయింట్ యొక్క సాపేక్ష స్థానం చాలా ముఖ్యం. కేంద్ర బిందువు వద్ద అత్యధిక శక్తి సాంద్రత ఉన్నందున, చాలా సందర్భాలలో, కేంద్ర బిందువు కత్తిరించేటప్పుడు వర్క్పీస్ యొక్క ఉపరితలం వద్ద లేదా కొంచెం తక్కువగా ఉంటుంది. మొత్తం కట్టింగ్ ప్రక్రియలో, స్థిరమైన కట్టింగ్ నాణ్యతను పొందటానికి ఫోకస్ మరియు వర్క్పీస్ యొక్క సాపేక్ష స్థానం స్థిరంగా ఉండేలా చూడటం ఒక ముఖ్యమైన పరిస్థితి.
3. ఎయిర్ బ్లోయింగ్ సిస్టమ్ & సహాయక వాయువు
సాధారణంగా, మెటీరియల్ లేజర్ కట్టింగ్కు సహాయక వాయువు వాడకం అవసరం, ప్రధానంగా సహాయక వాయువు యొక్క రకం మరియు పీడనానికి సంబంధించినది. సాధారణంగా, సహాయక వాయువు లెన్స్ను కాలుష్యం నుండి రక్షించడానికి లేజర్ పుంజంతో ఏకాంతంగా బయటకు తీయబడుతుంది మరియు కట్టింగ్ ప్రాంతం యొక్క దిగువన ఉన్న స్లాగ్ను చెదరగొడుతుంది. లోహేతర పదార్థాలు మరియు కొన్ని లోహ పదార్థాల కోసం, కరిగించిన మరియు ఆవిరైపోయిన పదార్థాలను తొలగించడానికి సంపీడన గాలి లేదా జడ వాయువు ఉపయోగించబడుతుంది, అదే సమయంలో కట్టింగ్ ప్రాంతంలో అధిక దహనను నిరోధిస్తుంది.
సహాయక వాయువును నిర్ధారించే ఆవరణలో, గ్యాస్ పీడనం చాలా ముఖ్యమైన అంశం. అధిక వేగంతో సన్నని పదార్థాన్ని కత్తిరించేటప్పుడు, స్లాగ్ కట్ వెనుక భాగంలో అంటుకోకుండా నిరోధించడానికి అధిక గ్యాస్ పీడనం అవసరం (హాట్ స్లాగ్ వర్క్పీస్ను తాకినప్పుడు కట్ అంచుని దెబ్బతీస్తుంది). పదార్థ మందం పెరిగినప్పుడు లేదా కట్టింగ్ వేగం నెమ్మదిగా ఉన్నప్పుడు, గ్యాస్ పీడనాన్ని తగిన విధంగా తగ్గించాలి.
4. ప్రతిబింబ రేటు
CO2 లేజర్ యొక్క తరంగదైర్ఘ్యం 10.6 μm, ఇది లోహేతర పదార్థాలు గ్రహించడానికి గొప్పది. కానీ CO2 లేజర్ మెటల్ కట్టింగ్కు తగినది కాదు, ముఖ్యంగా బంగారం, వెండి, రాగి మరియు అల్యూమినియం మెటల్ వంటి అధిక ప్రతిబింబాలతో కూడిన లోహ పదార్థం మొదలైనవి.
తాపన యొక్క ప్రారంభ దశలో పుంజం యొక్క శోషణ రేటు ఒక ముఖ్యమైన పాత్ర పోషిస్తుంది, కాని కట్టింగ్ రంధ్రం వర్క్పీస్ లోపల ఏర్పడిన తర్వాత, రంధ్రం యొక్క నల్ల-శరీర ప్రభావం పదార్థం యొక్క శోషణ రేటును పుంజానికి దగ్గరగా చేస్తుంది 100%వరకు.
పదార్థం యొక్క ఉపరితల స్థితి పుంజం యొక్క శోషణను నేరుగా ప్రభావితం చేస్తుంది, ముఖ్యంగా ఉపరితల కరుకుదనం, మరియు ఉపరితల ఆక్సైడ్ పొర ఉపరితలం యొక్క శోషణ రేటులో స్పష్టమైన మార్పులకు కారణమవుతుంది. లేజర్ కటింగ్ యొక్క అభ్యాసంలో, కొన్నిసార్లు బీమ్ శోషణ రేటుపై పదార్థ ఉపరితల స్థితి యొక్క ప్రభావం ద్వారా పదార్థం యొక్క కట్టింగ్ పనితీరును మెరుగుపరచవచ్చు.
5. లేజర్ హెడ్ నాజిల్
నాజిల్ సక్రమంగా ఎంపిక చేయబడితే లేదా సరిగా నిర్వహించబడకపోతే, కాలుష్యం లేదా నష్టాన్ని కలిగించడం సులభం, లేదా నాజిల్ నోరు యొక్క చెడు గుండ్రని లేదా వేడి లోహ స్ప్లాషింగ్ వల్ల కలిగే స్థానిక అడ్డుపడటం వలన, నాజిల్లో ఎడ్డీ ప్రవాహాలు ఏర్పడతాయి, దీని ఫలితంగా గణనీయంగా జరుగుతుంది అధ్వాన్నమైన కట్టింగ్ పనితీరు. కొన్నిసార్లు, నాజిల్ నోరు కేంద్రీకృత పుంజానికి అనుగుణంగా ఉండదు, నాజిల్ అంచుని కత్తిరించడానికి పుంజం ఏర్పడుతుంది, ఇది అంచు కట్టింగ్ నాణ్యతను కూడా ప్రభావితం చేస్తుంది, చీలిక వెడల్పును పెంచుతుంది మరియు కట్టింగ్ సైజు తొలగుట చేస్తుంది.
నాజిల్ కోసం, రెండు సమస్యలకు ప్రత్యేక శ్రద్ధ వహించాలి
ఎ. నాజిల్ వ్యాసం యొక్క ప్రభావం.
బి. నాజిల్ మరియు వర్క్పీస్ ఉపరితలం మధ్య దూరం యొక్క ప్రభావం.
6. ఆప్టికల్ మార్గం
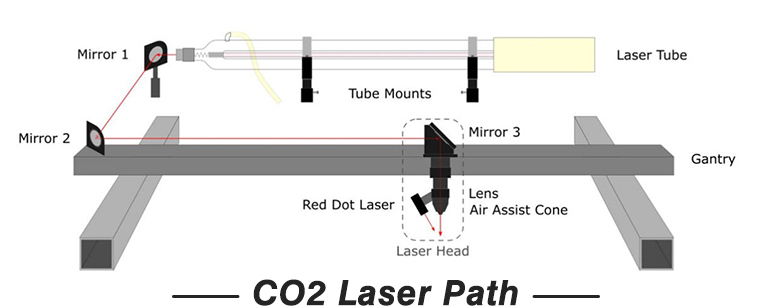
లేజర్ విడుదల చేసే అసలు పుంజం బాహ్య ఆప్టికల్ పాత్ సిస్టమ్ ద్వారా ప్రసారం అవుతుంది (ప్రతిబింబం మరియు ప్రసారంతో సహా), మరియు వర్క్పీస్ యొక్క ఉపరితలాన్ని చాలా ఎక్కువ శక్తి సాంద్రతతో ఖచ్చితంగా ప్రకాశిస్తుంది.
కట్టింగ్ టార్చ్ వర్క్పీస్ పైన నడుస్తున్నప్పుడు, కాంతి పుంజం లెన్స్ మధ్యలో సరిగ్గా ప్రసారం చేయబడి, కత్తిరించడానికి ఒక చిన్న ప్రదేశంలో కేంద్రీకృతమై ఉండేలా బాహ్య ఆప్టికల్ పాత్ సిస్టమ్ యొక్క ఆప్టికల్ అంశాలను క్రమం తప్పకుండా తనిఖీ చేసి సమయానికి సర్దుబాటు చేయాలి. అధిక నాణ్యత కలిగిన వర్క్పీస్. ఏదైనా ఆప్టికల్ మూలకం యొక్క స్థానం మారిన తర్వాత లేదా కలుషితమైన తర్వాత, కట్టింగ్ నాణ్యత ప్రభావితమవుతుంది మరియు కట్టింగ్ కూడా నిర్వహించబడదు.
బాహ్య ఆప్టికల్ పాత్ లెన్స్ వాయు ప్రవాహంలో మలినాలు ద్వారా కలుషితం చేయబడుతుంది మరియు కట్టింగ్ ప్రాంతంలో కణాలను స్ప్లాషింగ్ చేయడం ద్వారా బంధించబడుతుంది, లేదా లెన్స్ తగినంతగా చల్లబడదు, ఇది లెన్స్ వేడెక్కడానికి మరియు పుంజం శక్తి ప్రసారాన్ని ప్రభావితం చేస్తుంది. ఇది ఆప్టికల్ మార్గం యొక్క ఘర్షణకు కారణమవుతుంది మరియు తీవ్రమైన పరిణామాలకు దారితీస్తుంది. లెన్స్ వేడెక్కడం కూడా ఫోకల్ వక్రీకరణను ఉత్పత్తి చేస్తుంది మరియు లెన్స్కు కూడా అపాయం కలిగిస్తుంది.
CO2 లేజర్ కట్టర్ రకాలు మరియు ధరల గురించి మరింత తెలుసుకోండి
పోస్ట్ సమయం: సెప్టెంబర్ -20-2022