การเชื่อมด้วยเลเซอร์ส่วนใหญ่มีวัตถุประสงค์เพื่อปรับปรุงประสิทธิภาพการเชื่อมและคุณภาพของวัสดุผนังบางและชิ้นส่วนที่มีความแม่นยำ วันนี้เราจะไม่พูดถึงข้อดีของการเชื่อมด้วยเลเซอร์ แต่มุ่งเน้นไปที่วิธีการใช้ก๊าซป้องกันสำหรับการเชื่อมด้วยเลเซอร์อย่างเหมาะสม
ทำไมต้องใช้ Gas Shield สำหรับการเชื่อมด้วยเลเซอร์?
ในการเชื่อมด้วยเลเซอร์ก๊าซโล่จะส่งผลกระทบต่อการสร้างการเชื่อมคุณภาพการเชื่อมความลึกของการเชื่อมและความกว้างของการเชื่อม ในกรณีส่วนใหญ่การเป่าก๊าซที่ได้รับความช่วยเหลือจะมีผลในเชิงบวกต่อการเชื่อม แต่อาจนำผลข้างเคียง
เมื่อคุณเป่าแก๊สโล่อย่างถูกต้องมันจะช่วยคุณ:
ปกป้องสระเชื่อมอย่างมีประสิทธิภาพเพื่อลดหรือหลีกเลี่ยงการเกิดออกซิเดชัน
ลดสาดน้ำที่ผลิตในกระบวนการเชื่อมได้อย่างมีประสิทธิภาพ
ลดรูขุมขนเชื่อมได้อย่างมีประสิทธิภาพ
ช่วยสระว่ายน้ำเชื่อมได้อย่างสม่ำเสมอเมื่อแข็งตัวเพื่อให้ตะเข็บเชื่อมมาพร้อมกับขอบที่สะอาดและเรียบเนียน
เอฟเฟกต์การป้องกันของขนนกโลหะหรือพลาสมาเมฆบนเลเซอร์จะลดลงอย่างมีประสิทธิภาพและอัตราการใช้งานที่มีประสิทธิภาพของเลเซอร์เพิ่มขึ้น
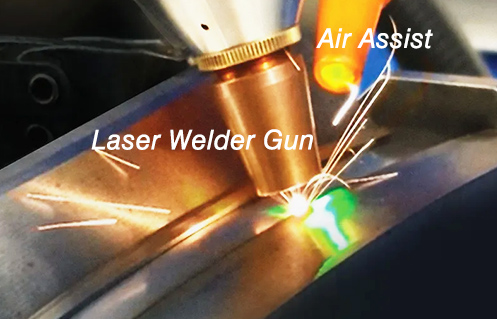
ตราบใดที่ประเภทเกาการป้องกันอัตราการไหลของก๊าซและการเลือกโหมดเป่าลมถูกต้องคุณสามารถได้รับผลในอุดมคติของการเชื่อม อย่างไรก็ตามการใช้ก๊าซป้องกันที่ไม่ถูกต้องอาจส่งผลเสียต่อการเชื่อม การใช้ก๊าซโล่ที่ไม่ถูกต้องอาจนำไปสู่เสียงดังเอี๊ยดในการเชื่อมหรือลดคุณสมบัติเชิงกลของการเชื่อม อัตราการไหลของก๊าซสูงเกินไปหรือต่ำเกินไปอาจนำไปสู่การเกิดออกซิเดชันของการเชื่อมที่รุนแรงมากขึ้นและการรบกวนภายนอกอย่างรุนแรงของวัสดุโลหะภายในสระว่ายน้ำเชื่อมส่งผลให้เกิดการล่มสลายหรือการก่อตัวที่ไม่สม่ำเสมอ
ประเภทของก๊าซโล่
ก๊าซป้องกันที่ใช้กันทั่วไปของการเชื่อมด้วยเลเซอร์ส่วนใหญ่เป็น N2, AR และ HE คุณสมบัติทางกายภาพและทางเคมีของพวกเขาแตกต่างกันดังนั้นผลกระทบที่มีต่อรอยเชื่อมก็แตกต่างกัน
ไนโตรเจน (N2)
พลังงานไอออนไนซ์ของ N2 อยู่ในระดับปานกลางสูงกว่าของ AR และต่ำกว่าของเขา ภายใต้การแผ่รังสีของเลเซอร์ระดับการแตกตัวเป็นไอออนของ N2 จะอยู่บนกระดูกงูสมเวลซึ่งสามารถลดการก่อตัวของคลาวด์พลาสมาได้ดีขึ้นและเพิ่มอัตราการใช้งานที่มีประสิทธิภาพของเลเซอร์ ไนโตรเจนสามารถทำปฏิกิริยากับโลหะผสมอลูมิเนียมและเหล็กกล้าคาร์บอนที่อุณหภูมิที่แน่นอนในการผลิตไนไตรด์ซึ่งจะปรับปรุงความเปราะบางของเชื่อมและลดความเหนียวและมีผลกระทบที่ไม่พึงประสงค์อย่างมากต่อคุณสมบัติเชิงกลของข้อต่อเชื่อม ดังนั้นจึงไม่แนะนำให้ใช้ไนโตรเจนเมื่อเชื่อมอลูมิเนียมเชื่อมและเหล็กกล้าคาร์บอน
อย่างไรก็ตามปฏิกิริยาทางเคมีระหว่างไนโตรเจนและสแตนเลสที่สร้างขึ้นโดยไนโตรเจนสามารถปรับปรุงความแข็งแรงของข้อต่อเชื่อมซึ่งจะเป็นประโยชน์ในการปรับปรุงคุณสมบัติเชิงกลของการเชื่อมดังนั้นการเชื่อมของสแตนเลสสามารถใช้ไนโตรเจนเป็นก๊าซป้องกัน
อาร์กอน (AR)
พลังงานไอออไนเซชันของอาร์กอนค่อนข้างต่ำและระดับไอออไนเซชันของมันจะสูงขึ้นภายใต้การกระทำของเลเซอร์ จากนั้นอาร์กอนในฐานะก๊าซป้องกันไม่สามารถควบคุมการก่อตัวของเมฆพลาสมาได้อย่างมีประสิทธิภาพซึ่งจะลดอัตราการใช้งานที่มีประสิทธิภาพของการเชื่อมด้วยเลเซอร์ คำถามที่เกิดขึ้น: อาร์กอนเป็นผู้สมัครที่ไม่ดีสำหรับการใช้งานเชื่อมเป็นก๊าซป้องกันหรือไม่? คำตอบคือไม่เป็นก๊าซเฉื่อยอาร์กอนนั้นยากที่จะทำปฏิกิริยากับโลหะส่วนใหญ่และ AR นั้นราคาถูกที่จะใช้ นอกจากนี้ความหนาแน่นของ AR นั้นมีขนาดใหญ่มันจะเอื้อต่อการจมลงสู่พื้นผิวของสระว่ายน้ำที่หลอมเหลวเชื่อมและสามารถป้องกันสระน้ำได้ดีขึ้นดังนั้นอาร์กอนจึงสามารถใช้เป็นก๊าซป้องกันทั่วไปได้
ฮีเลียม (เขา)
ซึ่งแตกต่างจากอาร์กอนฮีเลียมมีพลังงานไอออนไนซ์ค่อนข้างสูงซึ่งสามารถควบคุมการก่อตัวของเมฆพลาสมาได้อย่างง่ายดาย ในเวลาเดียวกันฮีเลียมไม่ได้ทำปฏิกิริยากับโลหะใด ๆ เป็นทางเลือกที่ดีสำหรับการเชื่อมด้วยเลเซอร์ ปัญหาเดียวคือฮีเลียมค่อนข้างแพง สำหรับผู้ประดิษฐ์ที่ให้บริการผลิตภัณฑ์โลหะที่ผลิตจำนวนมากฮีเลียมจะเพิ่มค่าใช้จ่ายในการผลิตเป็นจำนวนมาก ดังนั้นฮีเลียมจึงใช้ในการวิจัยทางวิทยาศาสตร์หรือผลิตภัณฑ์ที่มีมูลค่าเพิ่มสูงมาก
วิธีเป่าแก๊สโล่?
ก่อนอื่นควรชัดเจนว่าสิ่งที่เรียกว่า "การเกิดออกซิเดชัน" ของการเชื่อมเป็นเพียงชื่อสามัญซึ่งในทางทฤษฎีหมายถึงปฏิกิริยาทางเคมีระหว่างการเชื่อมและส่วนประกอบที่เป็นอันตรายในอากาศซึ่งนำไปสู่การเสื่อมสภาพของการเชื่อม . โดยทั่วไปโลหะเชื่อมทำปฏิกิริยากับออกซิเจนไนโตรเจนและไฮโดรเจนในอากาศที่อุณหภูมิที่แน่นอน
เพื่อป้องกันไม่ให้เชื่อม "ออกซิไดซ์" ต้องลดหรือหลีกเลี่ยงการสัมผัสระหว่างส่วนประกอบที่เป็นอันตรายและโลหะเชื่อมภายใต้อุณหภูมิสูงซึ่งไม่เพียง แต่ในโลหะสระว่ายน้ำที่หลอมเหลว แต่ตลอดเวลาจากเวลาที่โลหะเชื่อมถูกละลายจนกระทั่ง โลหะสระว่ายน้ำหลอมเหลวนั้นแข็งตัวและอุณหภูมิจะเย็นลงถึงอุณหภูมิที่แน่นอน
สองวิธีหลักในการเป่าแก๊สโล่
หนึ่งคือการเป่าแก๊สโล่ที่แกนด้านข้างดังแสดงในรูปที่ 1
อีกวิธีหนึ่งคือวิธีการเป่าแบบโคแอกเชียลดังแสดงในรูปที่ 2
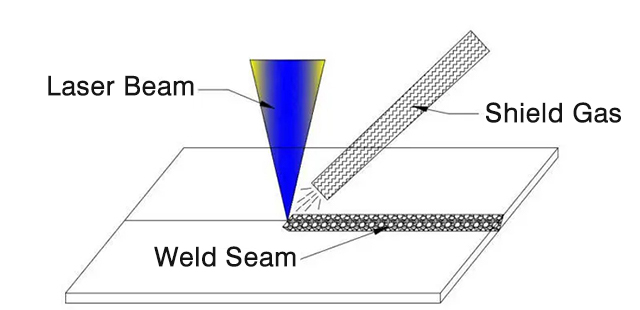
รูปที่ 1.
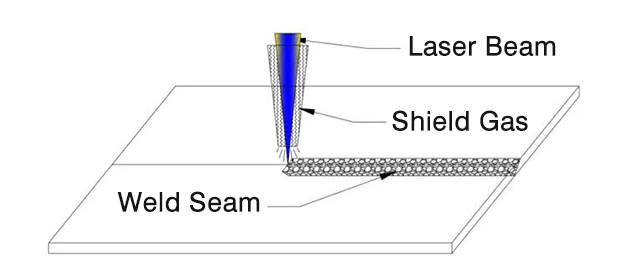
รูปที่ 2.
ทางเลือกเฉพาะของวิธีการเป่าสองวิธีคือการพิจารณาที่ครอบคลุมในหลาย ๆ ด้าน โดยทั่วไปขอแนะนำให้ใช้วิธีการป้องกันก๊าซด้านข้าง
ตัวอย่างของการเชื่อมด้วยเลเซอร์
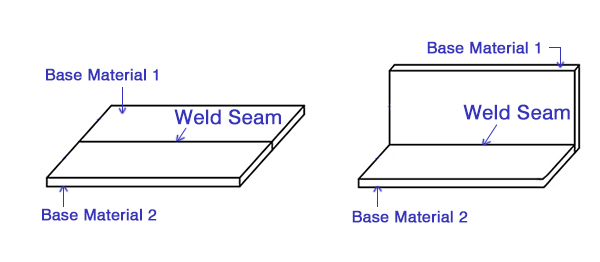
1. การเชื่อมลูกปัด/เส้นตรง
ดังที่แสดงในรูปที่ 3 รูปร่างการเชื่อมของผลิตภัณฑ์เป็นเส้นตรงและรูปแบบข้อต่อสามารถเป็นข้อต่อก้น, ข้อต่อตัก, มุมลบหรือข้อต่อเชื่อมที่ทับซ้อนกัน สำหรับผลิตภัณฑ์ประเภทนี้จะเป็นการดีกว่าที่จะใช้ก๊าซป้องกันด้านข้างด้านข้างดังแสดงในรูปที่ 1
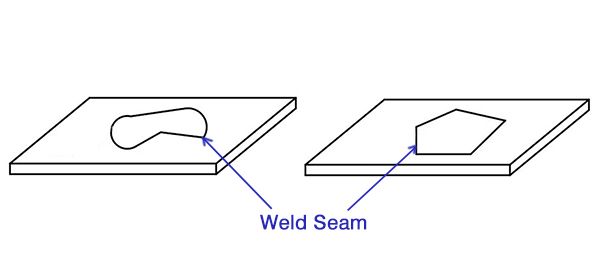
2. การเชื่อมรูปหรือพื้นที่ปิด
ดังที่แสดงในรูปที่ 4 รูปร่างการเชื่อมของผลิตภัณฑ์เป็นรูปแบบปิดเช่นเส้นรอบวงระนาบรูปร่างพหุภาคีระนาบรูปร่างเชิงเส้นหลายส่วนของระนาบ ฯลฯ รูปแบบข้อต่อสามารถเป็นข้อต่อก้น, ข้อต่อตัก, การเชื่อมที่ทับซ้อนกัน ฯลฯ เป็นการดีกว่าที่จะใช้วิธีการป้องกันก๊าซโคแอกเซียลดังแสดงในรูปที่ 2 สำหรับผลิตภัณฑ์ประเภทนี้
การเลือกก๊าซป้องกันส่งผลโดยตรงต่อคุณภาพการเชื่อมประสิทธิภาพและค่าใช้จ่ายในการผลิต แต่เนื่องจากความหลากหลายของวัสดุการเชื่อมในกระบวนการเชื่อมจริงการเลือกก๊าซเชื่อมมีความซับซ้อนมากขึ้น วิธีการตำแหน่งการเชื่อมรวมถึงข้อกำหนดของเอฟเฟกต์การเชื่อม ผ่านการทดสอบการเชื่อมคุณสามารถเลือกก๊าซเชื่อมที่เหมาะสมกว่าเพื่อให้ได้ผลลัพธ์ที่ดีขึ้น
สนใจการเชื่อมด้วยเลเซอร์และยินดีที่จะเรียนรู้วิธีการเลือก Gas Gas
ลิงค์ที่เกี่ยวข้อง:
เวลาโพสต์: ต.ค.-10-2022