1. Швидкість різання
Багато клієнтів у консультації з лазерним різанням запитають, як швидко може вирізати лазерна машина. Дійсно, лазерна різниця - це високоефективне обладнання, а швидкість різання, природно, є фокусом занепокоєння клієнтів. Але найшвидша швидкість різання не визначає якість лазерного різання.
Занадто швидко tВін скорочую швидкість
а. Не можу прорізати матеріал
б. Поверхня різання представляє косо зерно, а нижня половина заготовки виробляє плавлені плями
c. Груба ріжуча кромка
Занадто уповільнити швидкість різання
а. Над умовою плавлення з шорсткою різання поверхні
б. Ширший розрізний проміжок і гострий кут розплавиться в закруглені кути
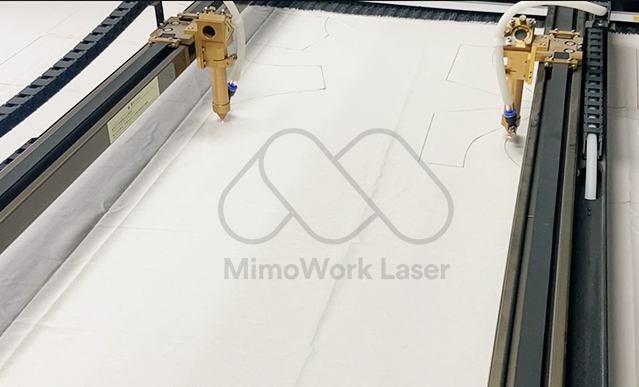
Щоб зробити обладнання для лазерного різання машини краще відтворити свою функцію різання, не просто запитуйте, наскільки швидко може вирізати лазерна машина, відповідь часто неточна. Навпаки, надайте mimowork специфікацією вашого матеріалу, і ми дамо вам більш відповідальну відповідь.
2.
Оскільки щільність лазерної потужності має великий вплив на швидкість різання, вибір фокусної відстань об'єктива є важливим моментом. Розмір лазерного плями після фокусування лазерного променя пропорційний фокусній відстані об'єктива. Після того, як лазерний промінь буде зосереджений об'єктивом з короткою фокусною відстань, розмір лазерного місця дуже невеликий, а щільність потужності в фокусному точці дуже висока, що корисно для різання матеріалу. Але його недоліком є те, що з короткою глибиною фокусу лише невелика припуск регулювання товщини матеріалу. Взагалі, об'єктив фокусування з короткою фокусною відстань більше підходить для швидкого різання тонкого матеріалу. А об'єктив фокусування з довгою фокусною відстань має широку фокусну глибину, доки вона має достатню щільність потужності, вона більше підходить для різання товстих заготовки, таких як піна, акрил та дерево.
Визначивши, який об'єктив фокусної відстань використовувати, відносне положення фокусної точки до поверхні заготовки є дуже важливим для забезпечення якості різання. Через найвищу щільність потужності в фокусному точці, у більшості випадків фокус знаходиться просто на або трохи нижче поверхні заготовки при різанні. У всьому процесі різання є важливим станом для того, щоб відносне положення фокусування та заготовки є постійним для отримання стабільної якості різання.
3. Система повітряного видування та допоміжний газ
Загалом, матеріальне лазерне різання вимагає використання допоміжного газу, в основному пов'язане з типом та тиском допоміжного газу. Зазвичай допоміжний газ викидається коаксіально лазерним променем для захисту об'єктива від забруднення і видування шлаку внизу області розрізання. Для неметалічних матеріалів та деяких металевих матеріалів використовується стиснене повітря або інертний газ для видалення розплавлених та випарених матеріалів, при цьому пригнічуючи надмірне згоряння в зоні різання.
Відповідно до передумови забезпечення допоміжного газу, тиск газу є надзвичайно важливим фактором. При розрізанні тонкого матеріалу на великій швидкості потрібен високий тиск газу, щоб запобігти прилипанні шлаку до задньої частини розрізу (гарячий шлак пошкодитиме крайовий край, коли він потрапляє на заготовку). Коли товщина матеріалу збільшується або швидкість різання повільна, тиск газу повинен бути належним чином знижений.
4. Коефіцієнт відображення
Довжина хвилі лазера CO2 становить 10,6 мкм, що чудово підходить для неметалічних матеріалів. Але лазер CO2 не підходить для різання металу, особливо металевого матеріалу з високою відбиттям, такими як золото, срібло, мідь та алюмінієвий метал тощо.
Швидкість поглинання матеріалу до променя відіграє важливу роль на початковій стадії нагрівання, але як тільки отвір для різання утворюється всередині заготовки, ефект чорного тіла отвору робить швидкість поглинання матеріалу до променя закритою до 100%.
Поверхневий стан матеріалу безпосередньо впливає на поглинання променя, особливо шорсткість поверхні, і шар поверхні оксиду спричинить очевидні зміни швидкості поглинання поверхні. У практиці лазерного різання іноді ефективність різання матеріалу може бути покращена шляхом впливу стану поверхні матеріалу на швидкість поглинання променя.
5. Лазерна насадка
Якщо насадка неправильно відібрана або погано підтримується, легко спричинити забруднення або пошкодження, або через погану округлюкість рота насадки або локального блокування, спричиненого бризок гарячого металу, у насадці будуть утворювати гірші вигідні показники. Іноді рот насадки не відповідає цілеспрямованому промені, утворюючи промінь для зсуву краю насадки, що також вплине на якість різання краю, збільшує ширину щілини і зробить дислокацію розміру різання.
Для форсунок слід приділяти особливу увагу на два питання
а. Вплив діаметра насадки.
б. Вплив відстані між насадкою та поверхнею заготовки.
6. Оптичний шлях
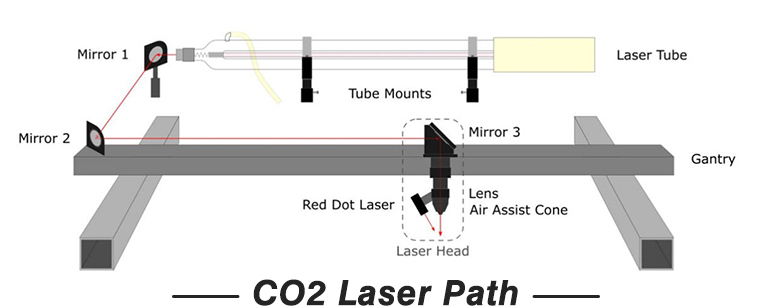
Оригінальний промінь, що випромінюється лазером, передається (включаючи відображення та передачу) через зовнішню систему оптичного шляху, і точно висвітлює поверхню заготовки з надзвичайно високою щільністю.
Оптичні елементи зовнішньої системи оптичного шляху слід регулярно перевіряти та регулювати вчасно, щоб переконатися, що коли різання факел проходить над заготовкою, світловий промінь правильно передається в центр об'єктива і зосереджується на невеликому місці, щоб вирізати заготовка з високою якістю. Після того, як положення будь -якого оптичного елемента змінюється або забруднюється, якість різання вплине, і навіть різання не може бути здійснено.
Зовнішня об'єктива оптичного шляху забруднюється домішками в потік повітря і скріплюється бризками частинок у зоні різання, або об'єктив не охолоджується, що призведе до перегріву лінзи та вплине на передачу енергії променя. Це спричиняє колімацію оптичного шляху до дрейфу і призводить до серйозних наслідків. Перегрівання об'єктива також призведе до вогнищевого спотворення і навіть загрожує сам об'єктив.
Дізнайтеся більше про типи лазерних різаків CO2 та ціни
Час посади: вересень-20-2022