Laser Cutting for DTF (Direct to Film)
Welcome to the vibrant world of Direct-to-Film (DTF) Printing – the game-changer in custom apparel!
If you’ve ever wondered how designers create eye-catching, durable prints on everything from cotton tees to polyester jackets, you’re in the right place.
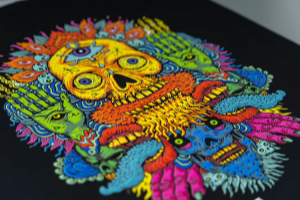
DTF Printing
By the end of this, you’ll:
1. Understand how DTF works and why it’s dominating the industry.
2. Discover its pros, cons, and how it stacks up against other methods.
3. Gain actionable tips for preparing flawless print files.
Whether you’re a seasoned printer or a curious newbie, this guide will equip you with insider knowledge to harness DTF like a pro.
What is DTF Printing?
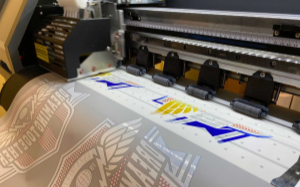
DTF Printer
DTF printing transfers intricate designs onto fabrics using a polymer-based film.
Unlike traditional methods, it’s fabric-agnostic – perfect for cotton, blends, and even dark materials.
Industry adoption has surged by 40% since 2021.
Used by brands like Nike and indie creators for its versatility.
Ready to see how the magic happens? Let’s break down the process.
How Does DTF Printing Work?
Step 1: Preparing the Film
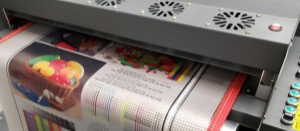
Direct to Film Printer
1. Print your design onto a special film, then coat it with adhesive powder.
High-resolution printers (Epson SureColor) ensure 1440 dpi precision.
2. Powder shakers evenly distribute adhesive for consistent bonding.
Use CMYK color mode and 300 DPI for crisp details.
Step 2: Heat Pressing
Pre-press fabric to remove moisture.
Then fuse the film at 160°C (320°F) for 15 seconds.
Step 3: Peeling & Post-Pressing
Peel the film cold, then post-press to lock in the design.
Post-pressing at 130°C (266°F) boosts wash durability to 50+ cycles.
Sold on DTF? Here's what we offer for Large Format DTF Cutting:
Designed for SEG Cutting: 3200mm (126 inches) in Width
• Laser Power: 100W/150W/300W
• Working Area: 3200mm * 1400mm
• Conveyor Working Table with Auto Feeding Rack
DTF Printing: Pros & Cons
DTF Printing Pros
Versatility: Works on cotton, polyester, leather, and even wood!
Vibrant Colors: 90% of Pantone colors achievable.
Durability: No cracking, even on stretchy fabrics.
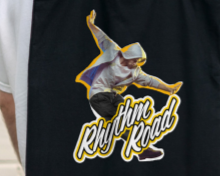
Direct to Film Printing
DTF Printing Cons
Startup Costs: Printers + film + powder = ~$5,000 upfront.
Slower Turnaround: 5–10 minutes per print vs. DTG’s 2 minutes.
Texture: Slightly raised feel compared to sublimation.
Factor | DTF | Screen Printing | DTG | Sublimation |
Fabric Types | All Materials | Cotton Heavy | Cotton ONLY | Polyester ONLY |
Cost (100Pcs) | $3.50/unit | $1.50/unit | $5/unit | $2/unit |
Durability | 50+ Washes | 100+ Washes | 30 Washes | 40 Washes |
How to Prepare Print Files for DTF
File Type
Use PNG or TIFF (no JPEG compression!).
Resolution
300 DPI minimum for sharp edges.
Colors
Avoid semi-transparencies; CMYK gamut works best.
Pro Tip
Add a 2px white outline to prevent color bleeding.
Common Questions about DTF
Is DTF better than sublimation?
For polyester, sublimation wins. For mixed fabrics, DTF reigns.
How long does DTF last?
50+ washes if post-pressed properly (per AATCC Standard 61).
DTF vs. DTG – which is cheaper?
DTG for single prints; DTF for batches (saves 30% on ink).
How to Laser Cut Sublimated Sportswear
The MimoWork vision laser cutter presents an innovative solution for cutting sublimated clothing such as sportswear, leggings, and swimwear.
With its advanced pattern recognition and precise cutting capabilities, you can achieve high-quality results in your printed sportswear.
The auto-feeding, conveying, and cutting features allow for continuous production, significantly enhancing your efficiency and output.
Laser cutting is widely utilized in various applications, including sublimation apparel, printed banners, teardrop flags, home textiles, and garment accessories.
Frequently Asked Questions (FAQ) About DTF Printing
DTF printing is a digital transfer method where designs are printed onto a special film, coated with adhesive powder, and heat-pressed onto fabric.
It works on cotton, polyester, blends, and even dark fabrics—making it one of the most versatile printing techniques today.
The DTF film acts as a temporary carrier for the design. After printing, it’s coated with adhesive powder, then heat-pressed onto fabric.
Unlike traditional transfers, DTF film allows for vibrant, detailed prints without fabric limitations.
It depends!
DTF Wins For: Small batches, complex designs, and mixed fabrics (no screens needed!).
Screen Printing Wins For: Large orders (100+ pieces) and ultra-durable prints (100+ washes).
Many businesses use both—screen printing for bulk orders and DTF for custom, on-demand jobs.
The DTF process involves:
1. Printing a design onto PET film.
2. Applying adhesive powder (which sticks to the ink).
3. Curing the powder with heat.
4. Pressing the film onto fabric and peeling it away.
The result? A soft, crack-resistant print that lasts 50+ washes.
No! DTF requires:
1. A DTF-compatible printer (e.g., Epson SureColor F2100).
2. Pigment inks (not dye-based).
3. A powder shaker for adhesive application.
Warning: Using regular inkjet film will result in poor adhesion and fading.
Factor | DTF Printing | DTG Printing |
Fabric | All Materials | Cotton ONLY |
Durability | 50+ Washes | 30 Washes |
Cost (100Pcs) | $3.50/shirt | $5/shirt |
Setup Time | 5–10 Mins Per Print | 2 Mins Per Print |
Verdict: DTF is cheaper for mixed fabrics; DTG is faster for 100% cotton.
Essential Equipment:
1. DTF printer (3,000 - 10,000)
2. Adhesive powder ($20/kg)
3. Heat press (500 - 2000)
4. PET film (0.5-1.50/sheet)
Budget Tip: Starter kits (like the VJ628D) cost ~$5,000.
Breakdown (Per Shirt):
1. Film: $0.50
2. Ink: $0.30
3. Powder: $0.20
4. Labor: 2.00 - 3.50/shirt (vs. 5 for DTG).
Example:
1. Investment: $8,000 (printer + supplies).
2. Profit/Shirt: 10 (retail) – 3 (cost) = $7.
3. Break-Even: ~1,150 shirts.
4. Real-World Data: Most shops recoup costs in 6–12 months.