Laser Cleaning Plastic
Laser cleaning is a technology primarily used for removing contaminants like rust, paint, or dirt from various surfaces.
When it comes to plastics, the application of handheld laser cleaners is a bit more complex.
But it is possible under certain conditions.
Can you Laser Clean Plastic?
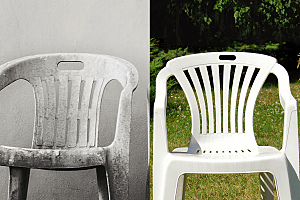
Plastic Chair Before & After Laser Cleaning
How Laser Cleaning Works:
Laser cleaners emit high-intensity beams of light that can vaporize or dislodge unwanted materials from a surface.
While it is possible to use handheld laser cleaners on plastic.
Success depends on the type of plastic.
The nature of the contaminants.
And the proper use of the technology.
With careful consideration and appropriate settings.
Laser cleaning can be an effective method for maintaining and restoring plastic surfaces.
What Type of Plastic Can be Laser Cleaned?
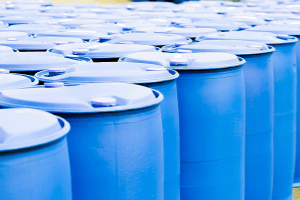
Industrial Plastic Bins for Laser Cleaning
Laser cleaning can be effective for certain types of plastics, but not all plastics are suitable for this method.
Here’s a breakdown of:
Which plastics can be laser cleaned.
Those that can be cleaned with limitations.
And those that should be avoided unless tested.
Plastics Great for Laser Cleaning
Acrylonitrile Butadiene Styrene (ABS):
ABS is tough and can withstand the heat generated by lasers, making it an excellent candidate for effective cleaning.
Polypropylene (PP):
Why it works: This thermoplastic has good heat resistance, allowing for effective cleaning of contaminants without significant damage.
Polycarbonate (PC):
Why it works: Polycarbonate is resilient and can handle the laser's intensity without deforming.
Plastics That Can Be Laser Cleaned with Limitations
Polyethylene (PE):
While it can be cleaned, careful attention is needed to avoid melting. Lower laser power settings are often required.
Polyvinyl Chloride (PVC):
PVC can be cleaned, but it may release harmful fumes when exposed to high temperatures. Adequate ventilation is essential.
Nylon (Polyamide):
Nylon can be sensitive to heat. Cleaning should be approached cautiously, with lower power settings to avoid damage.
Plastics Not Suitable for Laser Cleaning Unless Tested
Polystyrene (PS):
Polystyrene is highly susceptible to melting and deformation under laser energy, making it a poor candidate for cleaning.
Thermosetting Plastics (e.g., Bakelite):
These plastics harden permanently when set and cannot be reformed. Laser cleaning can cause cracking or breaking.
Polyurethane (PU):
This material can be easily damaged by heat, and laser cleaning can lead to unwanted surface changes.
Laser Cleaning Plastic is Difficult
But We Can Provide the Right Settings
Pulsed Laser Cleaning for Plastic
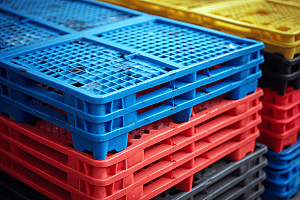
Plastic Pallets for Laser Cleaning
Pulsed laser cleaning is a specialized method for removing contaminants from plastic surfaces using short bursts of laser energy.
This technique is particularly effective for cleaning plastics.
And offers several advantages over continuous wave lasers or traditional cleaning methods.
Why Pulsed Lasers Are Ideal for Cleaning Plastic
Controlled Energy Delivery
Pulsed lasers emit short, high-energy bursts of light, allowing for precise control over the cleaning process.
This is crucial when working with plastics, which can be sensitive to heat.
The controlled pulses minimize the risk of overheating and damaging the material.
Effective Contaminant Removal
The high energy of pulsed lasers can effectively vaporize or dislodge contaminants such as dirt, grease, or paint.
Without physically scraping or scrubbing the surface.
This non-contact cleaning method preserves the integrity of the plastic while ensuring thorough cleaning.
Reduced Heat Impact
Since pulsed lasers deliver energy in brief intervals, the heat buildup on the plastic surface is significantly reduced.
This characteristic is essential for heat-sensitive materials.
As it prevents the warping, melting, or burning of the plastic.
Versatility
Pulsed lasers can be adjusted for different pulse durations and energy levels.
Making them versatile for various types of plastics and contaminants.
This adaptability allows operators to fine-tune settings based on the specific cleaning task.
Minimal Environmental Impact
The precision of pulsed lasers means less waste and fewer chemicals are needed compared to traditional cleaning methods.
This contributes to a cleaner working environment.
And reduces the ecological footprint associated with cleaning processes.
Comparison: Traditional & Laser Cleaning for Plastic
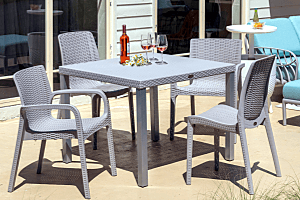
Plastic Furniture for Laser Cleaning
When it comes to cleaning plastic surfaces.
Traditional methods often fall short compared to the efficiency and precision of handheld pulsed laser cleaning machines.
Here’s a closer look at the drawbacks of traditional cleaning methods.
Drawbacks of Traditional Cleaning Methods
Use of Chemicals
Many traditional cleaning methods rely on harsh chemicals, which can damage plastics or leave harmful residues.
This can lead to plastic degradation, discoloration, or surface deterioration over time.
Physical Abrasion
Scrubbing or abrasive cleaning pads are commonly used in traditional methods.
These can scratch or wear down the surface of plastic, compromising its integrity and appearance.
Inconsistent Results
Traditional methods may not uniformly clean a surface, leading to missed spots or uneven finishes.
This inconsistency can be particularly problematic in applications where appearance and cleanliness are critical, such as in the automotive or electronics industries.
Time-Consuming
Traditional cleaning often requires multiple steps, including scrubbing, rinsing, and drying.
This can significantly increase downtime in manufacturing or maintenance processes.
Pulsed laser cleaning stands out as the best option for cleaning plastic due to its controlled energy delivery, effective contaminant removal, and reduced heat impact.
Its versatility and minimal environmental impact further enhance its appeal, making it a preferred choice for industries requiring meticulous cleaning of plastic surfaces.
Laser Power: 100W - 500W
Pulse Frequency Range: 20 - 2000 kHz
Pulse Length Modulation: 10 - 350 ns