Laser Oxide Removal
Oxides are common compounds resulting from oxidation processes that affect various materials.
Understanding how oxidation occurs helps in managing its effects.
Especially in industries where material integrity is crucial.
Laser cleaning emerges as a highly effective solution for removing these unwanted oxide layers.
Ensuring materials are restored to their original condition without harm.
What is Oxide & Oxidation?
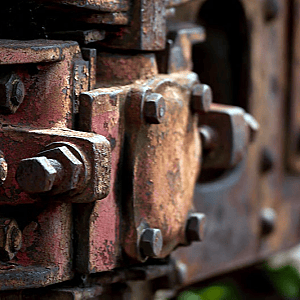
Oxidation Found in Train Tracks
Oxides are chemical compounds that consist of oxygen and another element.
They can form on various materials, including metals, ceramics, and even some non-metals.
Common Examples Include:
Rust:
Iron oxide (Fe₂O₃), which forms on iron and steel when they react with moisture and oxygen.
Aluminum Oxide:
A protective layer that forms on aluminum, preventing further corrosion.
Copper Oxide:
A green patina (Cu₂(OH)₂CO₃) that develops on copper surfaces over time.
Metals:
Metals like iron, copper, and aluminum readily oxidize when exposed to oxygen.
This can weaken the structural integrity of the metal.
Ceramics:
Oxidation can also affect ceramics, particularly those made from metal oxides.
Altering their properties and appearance.
Non-Metals:
Some non-metals, such as carbon, can oxidize to form carbon dioxide (CO₂) when burned.
Why Oxidation Should be Cleaned?
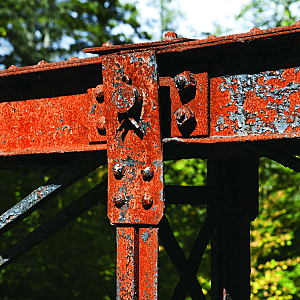
Oxidation Found on Bridge Structures Can be Laser Cleaned
Oxidation can significantly affect various materials in industrial settings.
Leading to a range of problems that can impact efficiency, safety, and costs.
Here are several reasons why it’s crucial to address oxidation:
Structural Integrity of Metals: Aesthetic and Functional Quality
Oxidation, particularly in metals like iron and steel, leads to corrosion.
Which can weaken structural components.
Bridges:
Rust can compromise the safety of bridges, necessitating expensive repairs or replacements.
Machinery:
Corroded parts in machinery can fail, leading to costly downtime and potential safety hazards.
Oil and Gas:
Oxidation in pipelines can lead to leaks or bursts, resulting in environmental hazards and financial losses.
Increased Maintenance Costs & Reduced Performance
When oxidation is not addressed, it can lead to increased maintenance and repair costs.
While also hindering the performance of various systems
Frequent Repairs:
Regularly repairing or replacing oxidized components can strain budgets.
Heat Exchangers:
Oxidation can decrease the efficiency of heat exchangers, leading to higher energy costs.
Manufacturing Equipment:
Oxidized surfaces can interfere with production processes, causing defects and waste.
Oxidation Can Lead to Serious Problems
Solve & Safeguards the Future with Laser Oxide Removal Machine
Application: Laser Oxide Removal
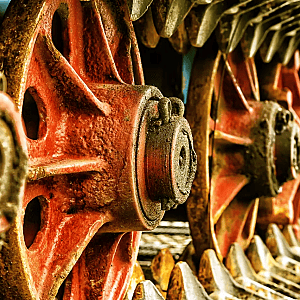
The Need for Oxide Removal is Almost Everywhere
Laser oxide removal is an advanced technique used to effectively eliminate oxidation from various materials, particularly metals.
This method is gaining popularity in several industrial applications due to its precision, efficiency, and eco-friendliness.
Here’s a closer look at specific applications of laser oxide removal.
Aluminum naturally forms a protective oxide layer when exposed to air.
However this oxide can sometimes interfere with further processing or bonding.
In industries such as aerospace and automotive.
Removing this oxide layer is crucial for achieving strong welds and ensuring proper adhesive bonding.
Laser cleaning allows for targeted removal of the oxide without damaging the underlying aluminum.
Ensuring that surfaces are clean and ready for further treatment.
Stainless steel is often used in environments prone to oxidation, leading to the formation of rust or scale.
In food processing, pharmaceuticals, and chemical industries.
Maintaining clean stainless steel surfaces is vital for hygiene and safety.
Laser oxide removal effectively cleans stainless steel surfaces, restoring their appearance and preventing corrosion.
Which in turn enhances the longevity of the equipment.
In welding, the presence of oxides on metal surfaces can lead to poor joint quality and weak welds.
Before welding, it’s important to remove any oxidation or contaminants from the metal surface to ensure a strong bond.
Laser cleaning provides a quick and precise way to prepare surfaces.
Resulting in stronger, more reliable welds and reducing the likelihood of defects.
Surface Preparation for Coating & Bonding
Proper surface preparation is essential before applying coatings or paints to ensure adhesion and durability.
In automotive and manufacturing industries.
Surfaces must be free of oxides and contaminants to achieve optimal coating performance.
Laser oxide removal thoroughly cleans surfaces.
Promoting better adhesion of coatings and enhancing the overall finish and longevity of the product.
Laser oxide removal is versatile and can be applied in various other settings:
Laser Cleaning Automotive Parts: Cleaning components like engine parts before assembly to prevent corrosion.
Electronics: Preparing metal surfaces for soldering or coating to improve conductivity and reliability.
Laser Cleaning Industrial Equipment: Regular maintenance of machinery to remove oxidation and prolong service life.
Laser Oxide Removal Machine
Laser oxide removal is a highly effective method for addressing oxidation on materials like aluminum and stainless steel across various applications, including welding, surface preparation, and bonding.
Its precision, efficiency, and eco-friendly nature make it an ideal choice for industries looking to maintain high standards of quality and performance.
Laser Power: 100W - 500W
Pulse Frequency Range: 20 - 2000 kHz
Pulse Length Modulation: 10 - 350 ns
Oxidation can lead to serious problems in various industrial applications, affecting safety, costs, and efficiency.
By addressing oxidation proactively, especially through advanced solutions like laser cleaning, businesses can protect their assets, enhance performance, and maintain a competitive edge.
Laser Power: 1000W - 3000W
Laser Wavelength: 1070nm
Cooling: Water Cooling