Laser Welding Aluminum
To laser weld aluminum safely and effectively, it's important to follow proper procedures and safety precautions.
This includes thoroughly cleaning the aluminum surface,
using the appropriate laser wavelength and power,
and providing adequate shielding gas coverage.
With the right techniques, handheld laser welding of aluminum can be a viable and advantageous joining method.
What is Handheld Laser Welding?
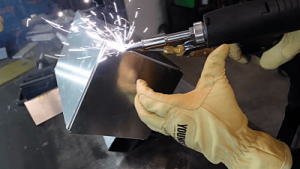
Handheld Laser Welding Aluminum
Handheld laser welding is an innovative technique that has gained significant traction in metal fabrication in recent years.
Unlike conventional welding methods such as MIG or TIG,
this process employs a concentrated laser beam to melt and join metal components with exceptional accuracy.
The primary benefits of handheld laser welding include remarkable speed, superior precision, and user-friendly operation.
In fact, laser welding can achieve speeds up to four times faster than traditional MIG or TIG welding,
while the highly focused laser ensures consistent, high-quality welds.
Thanks to advancements in fiber laser technology,
these systems have become more cost-effective and durable, accelerating their widespread adoption in the metalworking sector.
Can Aluminum be Laser Welded?
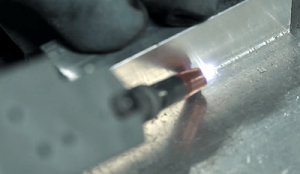
Laser Welding Aluminum with Aluminum Laser Welder
Yes, aluminum can be successfully laser welded, including with handheld laser welding systems.
Laser welding offers several advantages for welding aluminum compared to other welding methods.
Advantages for Laser Welding Aluminum
Narrow Weld Joints & Small Heat-Affected Zones :
This significantly reduces thermal distortion while preserving the structural stability of aluminum parts.
Precise Control:
Laser welding offers exceptional automation capabilities, enabling programmable precision for uniform, premium-quality welds.
Ability to Weld Thin Aluminum Sections:
Laser welding can effectively join aluminum as thin as 0.5 mm without burning through the material.
Unique Challenges for Laser Welding Aluminum
High Reflectivity
The highly reflective surface of aluminum causes substantial laser energy loss, posing challenges for effective beam-material coupling. Advanced processing methods are essential to enhance laser energy absorption.
Tendency for Porosity and Hot Cracking
Aluminum's rapid heat dissipation and fluid molten pool characteristics often result in welding imperfections such as gas pores and hot cracks. Precise regulation of process variables and inert gas protection is therefore essential.
Laser Welding Aluminum Can be Challenging
We Can Provide the Right Settings for you
How to Laser Weld Aluminum Safely?
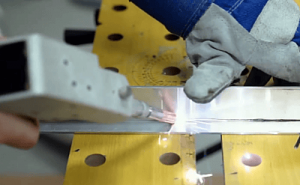
Laser Welding Highly Reflective Aluminum
Laser welding aluminum presents several unique challenges that must be addressed to ensure safe and successful welding.
From a material perspective,
Aluminum's high thermal conductivity,
Low melting point,
Tendency to form oxide layers
Can all contribute to welding difficulties.
How to Overcome these Challenges? (For Aluminum Laser Weld)
Manage Heat Input:
Aluminum's high thermal conductivity means that heat can quickly spread throughout the workpiece, leading to excessive melting or deformation.
Use a laser welding machine with sufficient power to penetrate the material, but carefully control the heat input by adjusting parameters like welding speed and laser power.
Remove Oxide Layers
The oxide layer that forms on the surface of aluminum has a much higher melting point than the base metal, which can lead to porosity and other defects.
Thoroughly clean the surface before welding, either mechanically or chemically, to ensure good weld quality.
Prevent Hydrocarbon Contamination
Any lubricants or contaminants on the aluminum surface can also cause issues during welding.
Ensure the workpiece is completely clean and dry before beginning the welding process.
Special Safety Considerations (For Laser Welding Aluminum)
Laser Safety
Aluminum's high reflectivity means that the laser beam can bounce around the work area, increasing the risk of eye and skin exposure.
Ensure proper laser safety protocols are in place, including the use of protective eyewear and shielding.
Fume Extraction
Welding aluminum can produce hazardous fumes, including those from the vaporization of alloying elements like magnesium and zinc.
Proper ventilation and fume extraction systems are essential to protect the welder and surrounding area.
Fire Prevention
The high heat input and molten metal associated with laser welding aluminum can pose a fire risk.
Take precautions to prevent ignition of nearby combustible materials and have appropriate fire extinguishing equipment on hand.
Laser Welding Aluminum Settings
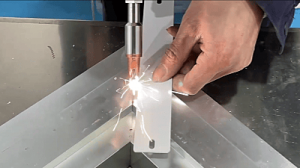
Handheld Laser Welding Aluminum Frame
When it comes to laser welding aluminum, the right settings can make all the difference.
General Settings for Laser Welding Aluminum (For Reference Only)
Laser Power
Aluminum's high reflectivity means that higher laser power is typically required, ranging from 1.5 kW to 3 kW or more, depending on the material thickness.
Focal Point
Focusing the laser beam slightly below the surface of the aluminum (around 0.5 mm) can help enhance penetration and reduce reflectivity.
Shielding Gas
Argon is the most commonly used shielding gas for laser welding aluminum, as it helps prevent oxidation and porosity in the weld.
Beam Diameter
Optimizing the laser beam diameter, typically between 0.2 and 0.5 mm, can balance penetration and heat input for the specific material thickness.
Welding Speed
The welding speed must be balanced to prevent both lack of penetration (too fast) and excessive heat input (too slow).
Recommended speeds typically range from 20 to 60 inches per minute.
Applications for Laser Welding Aluminum
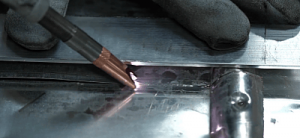
Laser Welding Aluminum with Handheld Laser Welder
Laser welding has become a popular technique for joining aluminum components across various industries due to its unique advantages.
Automotive Industry
Aluminum laser welders are extensively used in the automotive industry to join aluminum panels, doors, and other structural parts.
This helps reduce vehicle weight, improve fuel efficiency, and enhance the overall strength and rigidity of the vehicle body.
Aerospace Industry
In the aerospace sector, laser welding is employed to join engine blades, turbine discs, cabin walls, and doors made of aluminum alloys.
The precise control and minimal heat-affected zone of laser welding ensure the structural integrity and durability of these critical aircraft components.
Electronics and Communication
Laser welding is used to weld aluminum components in electronic devices, such as circuit boards, sensors, and displays.
The high precision and automation of laser welding enable reliable and consistent connections, crucial for the functionality and stability of electronic products.
Medical Devices
Aluminum laser welding is utilized in the manufacturing of medical devices, including surgical instruments, needles, stents, and dental appliances.
The sterile and damage-free nature of laser welding is essential for ensuring the safety and hygiene of these medical products.
Mold Processing
Laser welding is employed in the mold processing industry to repair and modify aluminum molds,
Such as stamping molds, injection molds, and forging molds.
The precise material addition and rapid repair capabilities of laser welding
Help extend the lifespan and performance of these critical manufacturing tools.
With a compact and small machine appearance, the portable laser welder machine is equipped with a moveable handheld laser welder gun, which is lightweight and convenient for multi-laser welding applications at any angles and surfaces.
Laser Power: 1000W - 1500W
Package Size (mm): 500*980*720
Cooling Method: Water Cooling
Cost Effective & Portable
The 3000W fiber laser welding machine features a high-power energy output, enabling it to laser weld thicker metal plates at a fast speed.
Equipped with a high-capacity water chiller to instantly cool down the laser welder temperature, the high-power fiber laser welder can function well and produce constant high-quality welding quality.
High Power Output for Industrial Setting
Higher Efficiency For Thicker Material
Industrial Water Chilling for Outstanding Performance