What is laser cleaning
By exposing concentrated laser energy to the surface of the contaminated workpiece, laser cleaning can remove the dirt layer instantly without damaging the substrate process. It is the ideal choice for a new generation of industrial cleaning technology.
Laser cleaning technology has also become an indispensable cleaning technology in the industry, shipbuilding, aerospace, and other high-end manufacturing fields, including the removal of rubber dirt on the surface of tire molds, the removal of silicon oil contaminants on the surface of gold film, and the high precision cleaning of microelectronics industry.
For laser technology such as laser cutting, laser engraving, laser cleaning, and laser welding, you may be familiar with these but the related laser source. There is a form for your reference which is about four laser sources and corresponding suitable materials and applications.
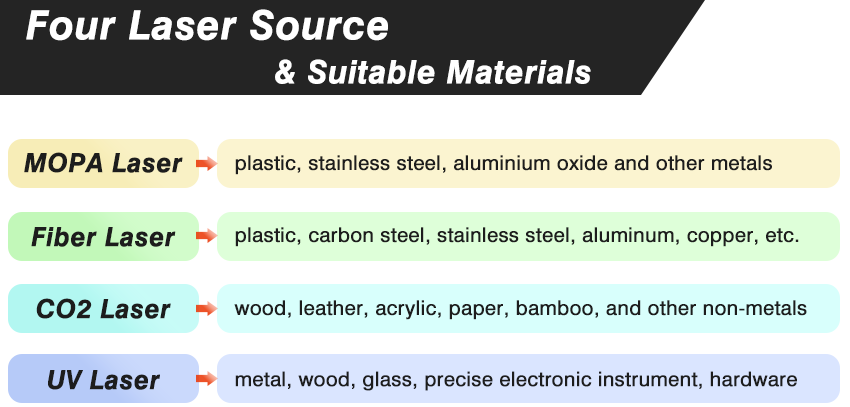
Four laser source about laser cleaning
Due to the differences in important parameters such as wavelength and power of different laser source, absorption rate of different materials and stains, so you need to choose the right laser source for your laser cleaning machine according to the specific contaminant removal requirements.
▶ MOPA Pulse Laser Cleaning
(working on all kinds of material)
MOPA laser is the most widely used type of laser cleaning. MO stands for master oscillator. Since MOPA fiber laser system can be amplified in strict accordance with the seed signal source coupled to the system, the relevant characteristics of the laser such as the center wavelength, pulse waveform and pulse width will not be changed. Therefore, the parameter adjustment dimension is higher and the range is wider. For different application scenarios of different materials, the adaptability is stronger and the process window interval is larger, which can meet the surface cleaning of various materials.
▶ Composite Fiber Laser Cleaning
(best choice for paint removal)
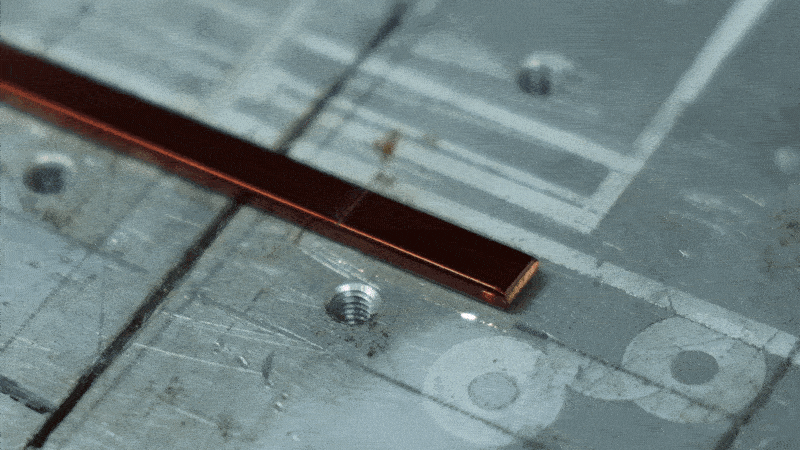
Laser composite cleaning uses semiconductor continuous laser to generate heat conduction output, so that the substrate to be cleaned absorbs energy to produce gasification, and plasma cloud, and form thermal expansion pressure between the metal material and the contaminated layer, reducing the interlayer bonding force. When the laser source generates a high-energy pulse laser beam, the vibration shock wave will peel off the attachment with the weak adhesion force, so as to achieve rapid laser cleaning.
Laser composite cleaning combines continuous laser and pulsed laser functions at the same time. High speed, high efficiency, and more uniform cleaning quality, for different materials, can also use different wavelengths of laser cleaning at the same time to achieve the purpose of removing stains.
For example, in the laser cleaning of thick coating materials, the single laser multi-pulse energy output is large and the cost is high. The composite cleaning of pulsed laser and semiconductor laser can quickly and effectively improve the cleaning quality, and does not cause damage to the substrate. In the laser cleaning of highly reflective materials such as aluminum alloy, a single laser has some problems such as high reflectivity. Using pulse laser and semiconductor laser composite cleaning, under the action of semiconductor laser thermal conduction transmission, increase the energy absorption rate of the oxide layer on the metal surface, so that the pulse laser beam can peel the oxide layer faster, improve the removal efficiency more effectively, especially the efficiency of paint removal is increased by more than 2 times.
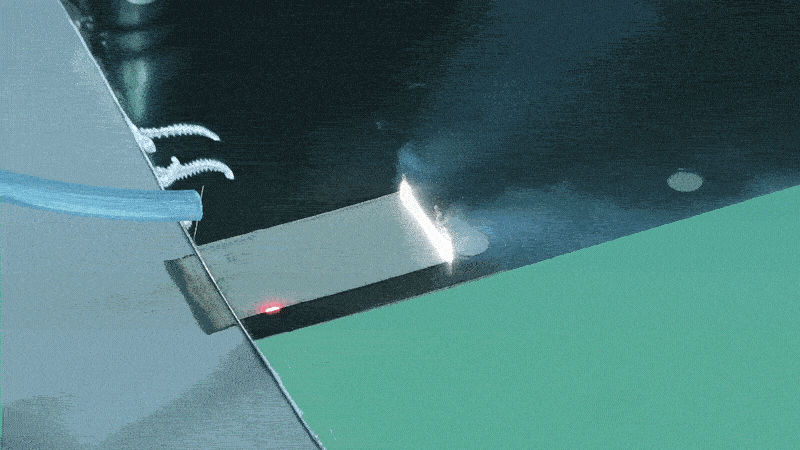
▶ CO2 Laser Cleaning
(best choice for cleaning non-metal material)
Carbon dioxide laser is a gas laser with CO2 gas as the working material, which is filled with CO2 gas and other auxiliary gases (helium and nitrogen as well as a small amount of hydrogen or xenon). Based on its unique wavelength, CO2 laser is the best choice for cleaning the surface of non-metallic materials such as removing glue, coating and ink. For example, the use of CO2 laser to remove the composite paint layer on the surface of aluminum alloy does not damage the surface of anodic oxide film, nor does it reduce its thickness.
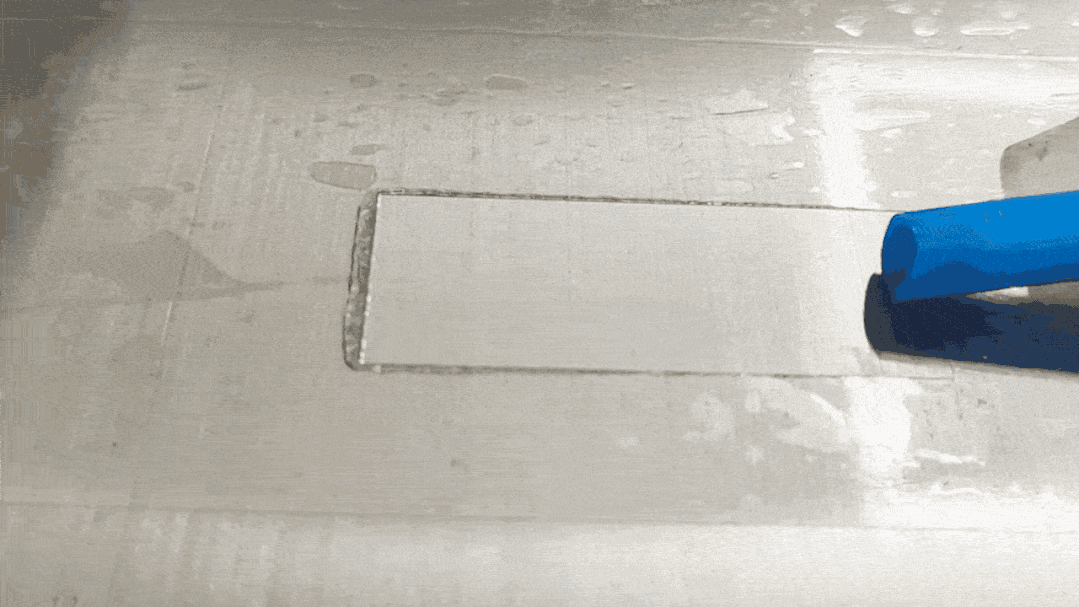
▶ UV Laser Cleaning
(best choice for sophisticated electronic device)
Ultraviolet lasers used in laser micromachining mainly include excimer lasers and all solid-state lasers. Ultraviolet laser wavelength is short, each single photon can deliver high energy, can directly break the chemical bonds between materials. In this way, coated materials are stripped off the surface in the form of gas or particles, and the whole cleaning process produce low heat energy that will only affect a small zone on the workpiece. As a result, UV laser cleaning has unique advantages in micro manufacturing, such as cleaning Si, GaN and other semiconductor materials, quartz, sapphire and other optical crystals, And polyimide (PI), polycarbonate (PC) and other polymer materials, can effectively improve the quality of manufacturing.
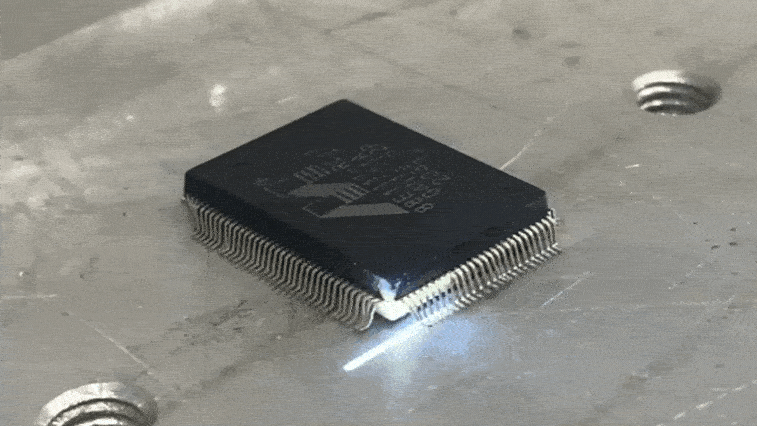
UV laser is considered to be the best laser cleaning scheme in the field of precision electronics, its most characteristic fine "cold" processing technology does not change the physical properties of the object at the same time, the surface of micro machining and processing, can be widely used in communication, optics, military, criminal investigation, medical and other industries and fields. For example, the 5G era has created a market demand for FPC processing. The application of UV laser machine makes it possible to precision cold machining of FPC and other materials.
Post time: Oct-10-2022