Introduction
In welding processes, the choice of shielding gas significantly influences arc stability, weld quality, and efficiency.
Different gas compositions offer unique advantages and limitations, making their selection critical for achieving optimal results in specific applications.
Below is an analysis of common shielding gases and their effects on welding performance.
Gas
Pure Argon
Applications: Ideal for TIG (GTAW) and MIG (GMAW) welding.
Effects: Ensures a stable arc with minimal spatter.
Advantages: Reduces weld contamination and produces clean, precise welds.
Carbon Dioxide
Applications: Commonly used in MIG welding for carbon steel.
Advantages: Enables faster welding speeds and deeper weld penetration.
Disadvantages:Increases weld spatter and raises the risk of porosity (bubbles in the weld).
Limited arc stability compared to argon blends.
Gas Blends for Enhanced Performance
Argon + Oxygen
Key Benefits:
Increases weld pool heat and arc stability.
Improves weld metal flow for smoother bead formation.
Reduces spatter and supports faster welding on thin materials.
Ideal For: Carbon steel, low-alloy steel, and stainless steel.
Argon + Helium
Key Benefits:
Boosts arc temperature and welding speed.
Reduces porosity defects, especially in aluminum welding.
Ideal For: Aluminum, nickel alloys, and stainless steel.
Argon + Carbon Dioxide
Common Use: Standard blend for MIG welding.
Advantages:
Enhances weld penetration and creates deeper, stronger welds.
Improves corrosion resistance in stainless steel.
Reduces spatter compared to pure CO₂.
Caution: Excessive CO₂ content can reintroduce spatter.
Want To Know More About Laser Welding?
Start a Conversation Now!
Ternary Blends
Argon + Oxygen+ Carbon Dioxide
Improves weld pool fluidity and reduces bubble formation.
Perfect for carbon steel and stainless steel.
Argon + Helium+ Carbon Dioxide
Enhances arc stability and heat control for thick materials.
Reduces weld oxidation and ensures high-quality, rapid welds.
Related Videos
Shielding Gas 101
Shielding gases are key in Laser Welding, TIG and MIG processes. Knowing their uses helps achieve quality welds.
Each gas has unique properties affecting welding results. The right choice leads to stronger welds.
This video shares useful handheld laser welding info for welders of all experience levels.
FAQs
In MIG welding, Argon is non-reactive, whereas in MAG welding, CO2 is reactive, which results in a more intense and deeply penetrating arc.
Argon is frequently utilized as the inert gas of choice in the TIG welding process.
It's highly popular among welders since it's applicable for welding various metals like mild steel, stainless steel, and aluminum, reflecting its versatility in the welding sector.
Additionally, a mixture of Argon and Helium can be employed in both TIG and MIG welding applications.
TIG welding demands pure Argon gas, which yields a pristine weld free from oxidization.
For MIG welding, a blend of Argon, CO2, and Oxygen is necessary to enhance penetration and heat.
Pure Argon is essential in TIG welding since, as a noble gas, it remains chemically inert during the process.
Selecting the Right Gas: Key Consideration
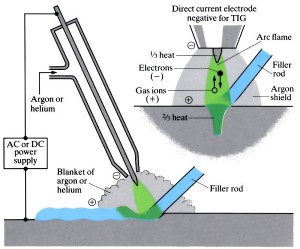
Gas Shielded TIG Welding Process
1. Material Type: Use Argon + Helium for aluminum; Argon + Carbon Dioxide for carbon steel; Argon + Oxygen for thin stainless steel.
2. Welding Speed: Carbon Dioxide or Helium blends accelerate deposition rates.
3. Spatter Control: Argon-rich mixtures (e.g., Argon + Oxygen) minimize spatter.
4. Penetration Needs: Carbon Dioxide or ternary blends enhance penetration in thick materials.
Related Articles
Recommend Machines
Post time: Apr-27-2025