Foam, a lightweight and porous material typically made from plastic or rubber, is valued for its excellent shock-absorbing and insulating properties. It is widely used in various applications, including packaging, cushioning, insulation, and creative arts and crafts.
From custom inserts for shipping and furniture production to wall insulation and industrial packaging, foam is an integral part of modern manufacturing. As the demand for foam components continues to rise, production techniques must adapt to meet these needs efficiently. Laser foam cutting has emerged as a highly effective solution, enabling businesses to achieve superior product quality while significantly boosting production capacity.
In this guide, we’ll delve into the process of laser cutting foam, its material compatibility, and the advantages it offers over traditional cutting methods.
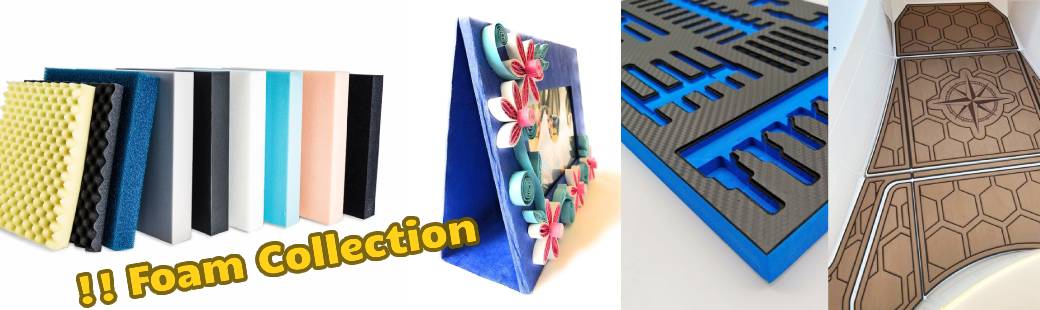
from
Laser Cut Foam Lab
The Overview of Laser Foam Cutting
▶ What is Laser Cutting ?
Laser cutting is a cutting-edge manufacturing process that employs CNC (computer numerically controlled) technology to direct a laser beam with precision.
This technique introduces intense heat into a small, focused point, quickly melting the material along a specified path.
For cutting thicker or tougher materials, reducing the laser's movement speed allows more heat to transfer to the workpiece.
Alternatively, a higher-wattage laser source, capable of generating more energy per second, can be utilized to achieve the same effect.
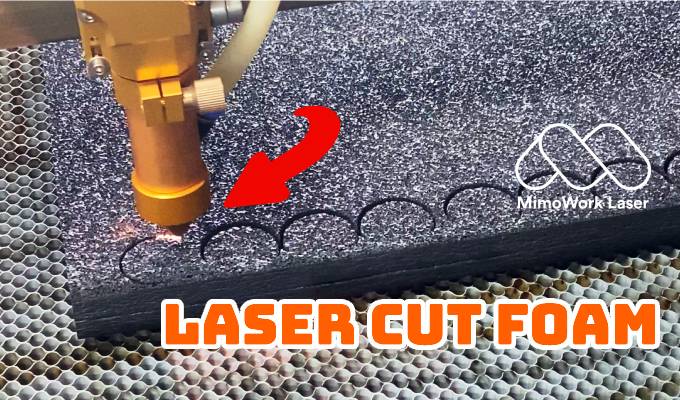
▶ How Laser Cutting Foam Works?
Laser foam cutting relies on a concentrated laser beam to precisely vaporize foam, removing material along predetermined paths. The process begins by preparing a laser cutting file using design software. The laser foam cutter's settings are then adjusted according to the foam's thickness and density.
Next, the foam sheet is securely positioned on the laser bed to prevent movement. The machine’s laser head is focused on the foam surface, and the cutting process follows the design with remarkable precision. Foam for laser cutting offers unparalleled accuracy, making it an excellent choice for creating intricate shapes and designs.
▶ Benefits from Laser Cutting Foam
Foam and similar materials present challenges for traditional cutting methods. Manual cutting requires skilled labor and is time-consuming, while punch-and-die setups can be expensive and inflexible.Laser foam cutters offer a range of advantages, making them a superior option for foam processing.
✔ Faster Production
Laser cutting foam significantly boosts production efficiency. While harder materials require slower cutting speeds, softer materials like foam, plastic, and plywood can be processed much faster. For example, foam inserts that might take hours to cut manually can now be produced in mere seconds using a laser foam cutter.
✔ Minimizing Material Waste
Traditional cutting methods can generate significant material waste, especially for intricate designs. Laser foam cutting reduces waste by enabling digital design layouts through CAD (computer-aided design) software. This ensures precise cuts on the first attempt, saving both material and time.
✔ Cleaner Edges
Soft foam often bends and distorts under pressure, making clean cuts challenging with traditional tools. Laser cutting, however, uses heat to precisely melt the foam along the cutting path, resulting in smooth and accurate edges. Unlike knives or blades, the laser doesn’t physically touch the material, eliminating issues like jagged cuts or uneven edges.
✔ Versatility and Flexibility
Laser cutters excel in versatility, allowing for diverse applications of laser foam cutting. From creating industrial packaging inserts to designing intricate props and costumes for the film industry, the possibilities are vast. Additionally, laser machines aren’t limited to foam; they can handle materials like metal, plastic and fabric with equal efficiency.
Crisp & Clean Edge
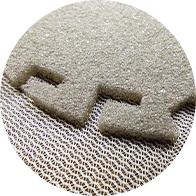
Flexible Multi-shapes Cutting
Vertical Cutting
How To Laser Cutting Foam?
▶ The Process Of Laser Cutting Foam
Laser cutting foam is a seamless and automated process. Using the CNC system, your imported cutting file guides the laser head along the designated cutting path with precision. Simply place your foam on the worktable, import the cutting file, and let the laser take it from there.
Foam Preparation: keep the foam flat and intact on the table.
Laser Machine: choose laser power and machine size according to foam thickness and size.
▶
Design File: import the cutting file to the software.
Laser Setting: test to cut foam by setting different speeds and powers
▶
Start Laser Cutting: laser cutting foam is automatic and highly precise, creating constant high-quality foam products.
Cut Seat Cushion with Foam Laser Cutter
▶ Some Tips When You Are Laser Cutting Foam
Material Fixation: Use tape, magnet, or vacuum table to keep your foam flat on the working table.
Ventilation: Proper ventilation is crucial to remove smoke and fumes generated during cutting.
Focusing: Ensure that the laser beam is properly focused.
Testing and Prototyping: Always conduct test cuts on the same foam material to fine-tune your settings before starting the actual project.
Any Questions About That?
Connect With Our Laser Expert !
Common Problems When Laser Cut Foam
Laser foam cutting is an effective and efficient method for processing foam materials. However, due to the soft and porous nature of foam, challenges can arise during the cutting process. Below are common issues encountered when using a laser foam cutter and their corresponding solutions.
1. Material Melting and Charring
Cause: Excessive laser power or slow cutting speeds lead to excessive energy deposition, causing the foam to melt or char.
Solution:
1. Lower the laser power output.
2. Increase the cutting speed to minimize prolonged heat exposure.
3. Test adjustments on scrap foam before proceeding with the final piece.
2. Material Ignition
Cause: Flammable foam materials, such as polystyrene and polyethylene, may ignite under high laser power.
Solution:
Carbonization Of Foam Due To Excessive Power
1. Reduce the laser power and increase cutting speed to prevent overheating.
2. Opt for non-flammable foams like EVA or polyurethane, which are safer alternatives for laser cutting foam.
Dirty Optics Leading To
Poor Edge Quality
3. Fumes and Odors
Cause: Foam materials, often plastic-based, emit hazardous and unpleasant fumes when melted.
Solusion:
1. Operate your laser cutter in a well-ventilated area.
2. Install a fume hood or exhaust system to remove harmful emissions.
3. Consider using an air filtration system to further minimize exposure to fumes.
4. Poor Edge Quality
Cause: Dirty optics or an out-of-focus laser beam can compromise the quality of foam cutting, resulting in uneven or jagged edges.
Solution:
1. Regularly clean the laser optics, especially after extended cutting sessions.
2. Verify that the laser beam is correctly focused on the foam material.
5. Inconsistent Cutting Depth
Cause: An uneven foam surface or inconsistencies in the foam’s density can disrupt the laser’s penetration depth.
Solution:
1. Ensure the foam sheet is lying perfectly flat on the workbench before cutting.
2. Use high-quality foam with consistent density for better results.
6. Poor Cutting Tolerances
Cause: Reflective surfaces or residual adhesive on the foam can interfere with the laser’s focus and accuracy.
Solution:
1. Cut reflective foam sheets from the non-reflective underside.
2. Apply masking tape to the cutting surface to reduce reflection and account for tape thickness.
Types And Application Of Laser Cutting Foam
▶ Types of Foam That Can Be Laser Cut
Laser cutting foam supports a variety of materials, ranging from soft to rigid. Each type of foam has unique properties that suit specific applications, simplifying the decision-making process for laser cutting projects. Below are the most popular types of foam for laser foam cutting:
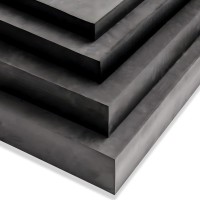
1. Ethylene-Vinyl Acetate(EVA) Foam
EVA foam is a high-density, highly elastic material. It is ideal for interior design and wall insulation applications. EVA foam maintains its shape well and is easy to glue, making it an excellent choice for creative and decorative design projects. Laser foam cutters handle EVA foam with precision, ensuring clean edges and intricate patterns.
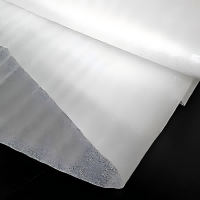
2. Polyethylene(PE) Foam
PE foam is a low-density material with good elasticity, making it perfect for packaging and shock absorption. Its lightweight nature is advantageous for reducing shipping costs. Additionally, PE foam is commonly laser cut for applications requiring high precision, such as gaskets and sealing components.
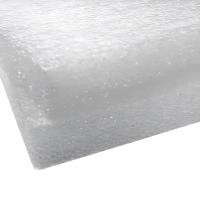
3. Polypropylene(PP) Foam
Known for its lightweight and moisture-resistant properties, polypropylene foam is widely used in the automotive industry for noise reduction and vibration control. Laser foam cutting ensures uniform results, crucial for the production of custom automotive parts.
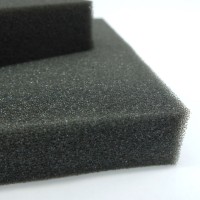
4. Polyurethane(PU) Foam
Polyurethane foam is available in both flexible and rigid varieties and offers great versatility. Soft PU foam is used for car seats, while rigid PU is used as insulation in refrigerator walls. Custom PU foam insulation is commonly found in electronic enclosures to seal the sensitive components, prevent shock damage, and prevent water ingress.
>> Check out the videos: Laser Cutting PU Foam
We Used
Material: Memory Foam (PU foam)
Material Thickness: 10mm, 20mm
Laser Machine: Foam Laser Cutter 130
You Can Make
Wide Application: Foam Core, Padding, Car Seat Cushion, Insulation, Acoustic Panel, Interior Decor, Crats, Toolbox and Insert, etc.
▶ Applications of Laser Cut Foam
What can you do with laser foam?
Laserable Foam Applications
Any questions about how the lase cutting foam work, Contact Us!
FAQs of Laser Cutting Foam
▶ What is the best laser to cut foam?
▶ How thick Can Laser Cut Foam?
▶ Can You Laser Cut EVA Foam?
▶ Can Foam With Adhesive Backing Be Laser Cut?
▶ Can Laser Cutter Engrave Foam?
▶ What Kind Of Foam Is Best For Laser Cutting?
Recommended Laser Foam Cutter
Working Table Size: 1300mm * 900mm (51.2” * 35.4 ”)
Laser Power Options: 100W/150W/300W
Overview of Flatbed Laser Cutter 130
For regular foam products like toolboxs, decorations, and crafts, the Flatbed Laser Cutter 130 is the most popular choice for foam cutting and engraving. The size and power satisfy most requirements, and the price is affordable. Pass through design, upgraded camera system, optional working table, and more machine configurations you can choose.

Working Table Size: 1600mm * 1000mm (62.9” * 39.3 ”)
Laser Power Options: 100W/150W/300W
Overview of Flatbed Laser Cutter 160
The Flatbed Laser Cutter 160 is a large-format machine. With the auto feeder and conveyor table, you can accomplish auto-processing roll materials. 1600mm *1000mm of working area is suitable for most yoga mat, marine mat, seat cushion, industrial gasket and more. Multiple laser heads are optional to enhance productivity.

Send Your Requirements to Us, We will Offer A Professional Laser Solution
Start A Laser Consultant Now!
> What information you need to provide?
> Our contact information
Dive Deeper ▷
You may be interested in
Any Confusion Or Questions For The Foam Laser Cutter, Just Inquire Us At Any Time
Post time: Jan-14-2025