Using a Laser welding machine is a widely used manufacturing process that involves using a high-energy laser beam to fuse materials together. This technology has found its application in a wide range of industries, from automotive and aerospace to medical and electronics. In this article, we will explore the various applications for using a laser welder, highlighting its advantages in each field.
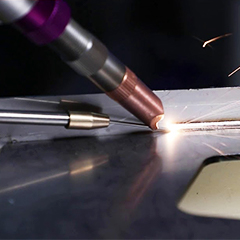
Applications of Laser Welding?
Automotive Industry
The automotive industry is one of the biggest users of laser welding technology. This is due to the high accuracy and speed of laser welding, which allows manufacturers to produce excellent-quality automotive components in large quantities. A Laser welder is used for welding body components, chassis parts, exhaust systems, and other critical parts in the vehicle. Laser welding provides superior welding quality, which ensures the strength and durability of the final product.
Aerospace Industry
The aerospace industry requires topnotch-quality welding to produce reliable and safe parts. Laser welding has found its application in the aerospace industry due to its ability to weld high-strength alloys and lightweight materials. The precision and speed when welding with laser make it an ideal process for welding thin materials used in the production of aircraft components, such as control surfaces, wings, and fuel tanks.
Medical Industry
The medical industry has found several applications for laser welding. A Laser welding machine is used to manufacture medical implants, instruments, and devices that require high precision and accuracy. The laser beam's high level of control allows for the precise welding of small and complex parts, which is essential in the production of medical devices.
Electronics Industry
The electronics industry has also found various applications for using a handheld laser welder. Laser welding is used for welding electronic components such as sensors, connectors, and batteries. The high level of precision and control of laser welding enables the creation of high-quality welds that ensure the reliability and performance of the final product.
Jewelry Industry
The appearance of a handheld laser welding machine has revolutionized the jewelry industry by providing a more precise, accurate, and efficient welding process. Jewelry manufacturers use laser welders to repair and assemble small parts, such as clasps, prongs, and settings. The precise welding allows the manufacturer to create intricate designs and improve the quality of the final product.
Our recommended Handheld Laser Welder:
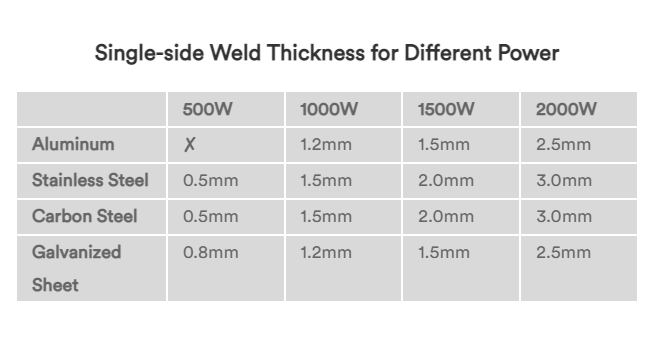
Laser Welder - Working Environment
◾ Temperature range of working environment: 15~35 ℃
◾ Humidity range of working environment: < 70%No condensation
◾ Cooling: water chiller is necessary due to the function of heat removing for laser heat-dissipating components, ensuring the laser welder runs well.
(Detailed use and guide about water chiller, you can check the: Freeze-proofing Measures for CO2 Laser System)
Advantages of Laser Welding?
• High accuracy and precision in welding
• Fast and efficient process
• High-quality welds with no distortion
• Ability to weld thin and delicate materials
• Minimal heat affected zone
• Little to no post-welding finishing required
• Non-contact welding process
Disadvantages of Laser Welding?
• High initial investment cost
• Maintenance cost and downtime
• Safety considerations due to the high energy of the laser beam
• Limited thickness of the material that can be welded
• Limited depth of penetration
In conclusion, laser welding has found its application in a wide range of industries due to its precision, speed, and accuracy. The advantages of using a laser welding machine include high-quality welds, efficient process, and minimal finishing required. However, the initial investment and maintenance cost, as well as safety considerations, should be taken into account. Overall, laser welding is a valuable technology for creating high-quality and reliable products in many industries.
Wanna Know more about Laser Welders?
Post time: Feb-23-2023