
Table of Content
Intro:
Laser welding is an advanced joining process that utilizes the concentrated heat of a laser beam to fuse together two or more metal components.
Unlike traditional welding techniques that rely on an open flame or electric arc, laser welding offers a highly precise and controlled method of creating strong, seamless joints.
1. What is laser Welding?
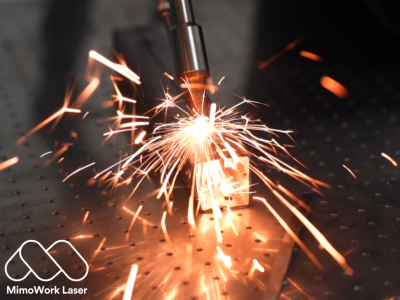
At the heart of the laser welding process is a specialized machine that generates an intense, focused beam of coherent light.
This laser beam is directed onto the target materials, where it rapidly heats the surface to its melting point.
The molten metal then fuses together, creating a tight, secure bond.
One of the key advantages of laser welding is its ability to produce very narrow, high-quality welds with minimal distortion or thermal damage to the surrounding area.
This makes it an ideal choice for applications that require precision, such as in the automotive, aerospace, and electronics industries.
Furthermore, laser welding is a highly automated process that can be easily integrated into manufacturing workflows.
This allows for increased productivity, reduced labor costs, and improved consistency in the final welded product.
Furthermore, laser welding is a highly automated process that can be easily integrated into manufacturing workflows.
This allows for increased productivity, reduced labor costs, and improved consistency in the final welded product.
Overall, laser welding represents a significant advancement in joining technology, offering a versatile and efficient solution for a wide range of industrial applications.
2. How Does Laser Welding Work?
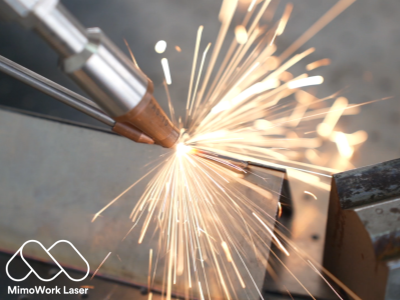
The laser welding process can be broken down into several key steps:
Laser Generation: The process begins with a powerful laser source. These lasers generate an intense, collimated beam of light with a specific wavelength and power output.
Beam Delivery: The laser beam is then directed and focused onto the workpiece using a series of mirrors and lenses. This ensures the beam is precisely aimed and concentrated at the desired welding location.
Material Interaction: As the focused laser beam strikes the surface of the metal components, it rapidly heats the material to its melting point. This creates a small, keyhole-shaped cavity in the metal, known as the "weld pool."
Weld Pool Formation: The molten metal in the weld pool flows and solidifies, forming a strong, continuous joint between the two workpieces. The depth and width of the weld pool can be carefully controlled by adjusting the laser power, speed, and focus.
Shielding Gas: In many laser welding applications, an inert shielding gas, such as argon or helium, is used to protect the weld pool from atmospheric contaminants, which could otherwise compromise the integrity of the joint.
Automation and Monitoring: Laser welding machines are often highly automated, with computer-controlled movement and precise monitoring of parameters like laser power, weld speed, and shielding gas flow. This ensures consistent, high-quality welds with minimal human intervention.
Handheld Variant: Handheld Welding Machines are also popular choices among workshops and personal uses, being mobile and extremely flexible on the fly. Trade off some laser welding power with much more affordability.
The versatility of laser welding allows it to be used on a wide range of metal materials, including steel, aluminum, and titanium.
By carefully optimizing the process parameters, welders can achieve deep, narrow welds with minimal distortion and a clean, uniform appearance.
Handheld Laser Welder or Laser Welding Machine
It can be Hard to Decide
3. How Much Does a Laser Welder Cost?
The cost of a laser welding machine can vary significantly depending on a number of factors, such as the specific type of laser, the size and power output of the machine, and the level of automation and integration features.
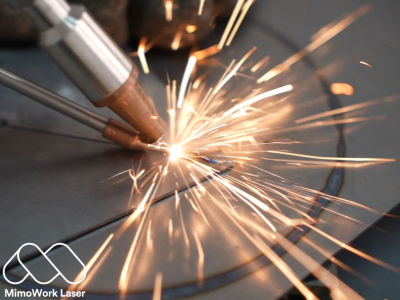
Basic tabletop laser welding systems can be purchased for $20,000 to $50,000.
These compact machines are typically used for small-scale, light-duty welding applications, such as jewelry making or prototype development.
On the higher end, large-scale, fully automated industrial laser welding systems can cost upwards of $500,000 to $1 million or more.
These advanced machines are often found in high-volume manufacturing environments, such as automobile assembly lines or aerospace component production facilities.
However...
If you are looking for something more affordable, more compact, in the trade of some welding capabilities, Handheld Laser Welding Machine would be what you are looking for.
Starting from $3,000 to $10,000.
4. Is Laser Welding Strong?
In short, Yes.
Laser welding is renowned for its ability to produce remarkably strong and durable joints, making it a highly desirable choice for a wide range of industrial applications.
The key factors that contribute to the inherent strength of laser welds include:
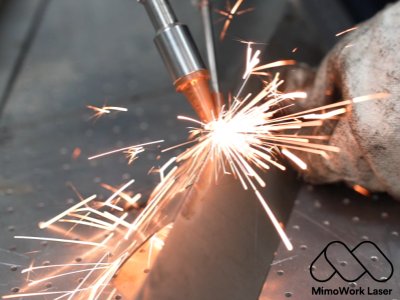
Weld Depth and Penetration: Laser welding can create deep, narrow welds that penetrate deeply into the base material, resulting in a stronger, more secure bond.
Minimal Distortion: The concentrated, precise nature of the laser beam ensures minimal thermal distortion of the surrounding metal, preserving the original structural integrity of the components.
Metallurgical Properties: The rapid heating and cooling of the weld pool can lead to desirable metallurgical changes, such as refined grain structure and increased hardness, further enhancing the strength of the joint.
Weld Geometry: Laser welds typically have a characteristic "keyhole" shape, which provides a larger surface area for the molten metal to solidify and form a strong, continuous bond.
Moreover, laser welding can be used to join a wide range of metal alloys, including steel, aluminum, and titanium, each with its own unique set of mechanical properties.
By carefully selecting the appropriate welding parameters and techniques, welders can optimize the strength and durability of the final joint.
Overall, the combination of precision, control, and metallurgical advantages make laser welding a highly reliable and robust joining method for critical applications where structural integrity is of paramount importance.
5. Are Laser Welders Any Good?
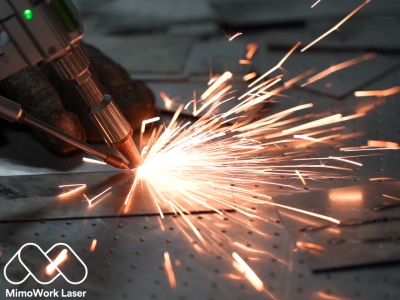
When it comes to the performance and capabilities of laser welding machines, the simple answer is: YES
They are highly effective and considered superior to many traditional welding techniques in a variety of applications.
One of the key advantages of laser welders is their ability to produce high-quality, consistent welds with minimal defects.
The precision and control afforded by the laser beam allows welders to create narrow, deep penetration welds with a clean, uniform appearance and minimal distortion of the base material.
Additionally, laser welding offers several process-related benefits that make it an attractive choice for industrial applications:
Speed and Productivity: Laser welding is a highly efficient process, with welding speeds that can be several times faster than conventional arc welding methods.
Automation and Integration: Laser welding machines are well-suited for automation, allowing for seamless integration into manufacturing workflows and increased productivity.
Versatility: Laser welding can be used to join a wide range of metal alloys, including steel, aluminum, and even dissimilar metals, making it a versatile solution for diverse applications.
Energy Efficiency: Laser welding is a more energy-efficient process compared to traditional welding, leading to lower operating costs and a reduced environmental impact.
Accessibility: Advancements in laser technology and the increasing availability of affordable laser welding systems have made this technology more accessible to a wider range of industries and applications.
Of course, like any welding technique, laser welding has its own unique set of challenges and limitations.
Factors such as joint accessibility, material thickness, and the need for specialized equipment and training can impact the suitability and cost-effectiveness of laser welding in certain applications.
However, the overwhelming evidence suggests that laser welding is a highly capable and reliable joining method, capable of delivering exceptional quality, productivity, and cost-effectiveness in a wide range of industrial settings.
6. What can be Welded using a Laser Welder?
One of the remarkable aspects of laser welding is its versatility in terms of the materials and components that can be successfully joined using this advanced joining technology.
Laser welding was initially developed for specific applications in the automotive and aerospace industries.
The scope of its usage has steadily expanded over the years to encompass a diverse range of materials and applications.
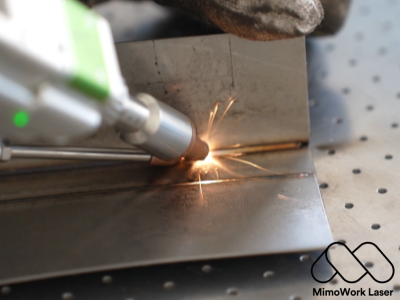
Some of the most common materials that can be effectively welded using a laser welder include:
Ferrous Metals: Steel (Low-carbon, High-carbon, Stainless), Cast Iron, Alloy Steels.
Non-Ferrous Metals: Aluminum & Aluminum alloys, Copper & Copper Alloys, Titanium & Titanium alloys.
Dissimilar Metals: Joining of Steel to Aluminum, Joining of Copper to Steel, Joining of Titanium to Other Metals.
In addition to these traditional metallic materials, laser welding has also found applications in the joining of advanced materials, such as ceramic-to-metal and polymer-to-metal composites, opening up new possibilities for innovative product designs and applications.
Beyond the versatility in material selection, laser welding can also be used to weld a wide range of component geometries, from thin sheets and foils to thick plates and complex, three-dimensional structures.
The precision and control offered by laser welding make it an ideal choice for applications that require high-quality, low-distortion welds, such as in the production of:
1. Automotive Body Panels and Frames
2. Aircraft Fuselage and Wing Components
3. Electronic Enclosures and Housings
4. Medical Devices and Implants
5. Precision Instruments and Machinery
As laser welding technology continues to evolve and become more accessible, the range of materials and components that can be successfully joined using this cutting-edge joining method will ONLY continue to expand, further solidifying its position as a vital tool in the modern industrial landscape.
Quick Video Overview: Laser Welders
Welding Like a Pro: Handheld Laser Welding
Laser Welding Vs TIG Welding
▶ Is Laser Welding Real?
Too Good to be Real?
Laser welding is a real and widely-used industrial joining technique. It utilizes the focused energy of a laser beam to melt and fuse materials together.
▶ Can you Laser Weld Aluminum?
Yes, laser welding is an effective method for joining aluminum and aluminum alloys.
The precision and control of the laser beam make it well-suited for welding this lightweight, reflective metal.
▶ Is Laser Welding Stronger than TIG?
In general, laser welding can produce welds that are stronger and more consistent than those created by traditional TIG (Tungsten Inert Gas) welding.
Due to its deeper penetration and narrower heat-affected zone.
▶ Does Laser Welding Need Gas?
Yes, most laser welding processes require the use of shielding gas.
Such as argon or helium, to protect the molten weld pool from atmospheric contamination and ensure high-quality, defect-free welds.
▶ Does Laser Welding use Filler?
Laser welding can be performed with or without the addition of filler material, depending on the specific application and joint requirements.
In some cases, filler wire is used to increase the weld volume or to join dissimilar metals.
▶ How Thick can a Laser Welder Weld?
Laser welding can accommodate a wide range of material thicknesses, from thin foils to plates several centimeters thick.
The specific welding depth capability depends on the power output and type of laser used.
▶ Is Laser Welding as Strong as MIG?
Laser welding can produce welds that are as strong, or even stronger, than those created by traditional MIG (Metal Inert Gas) welding.
Depending on the materials, joint design, and welding parameters used.
▶ Is Laser Welding Easy?
Laser welding requires specialized equipment, expertise, and training to achieve optimal results.
While the process itself is relatively straightforward, the precise control and integration of the laser system, shielding gas, and other parameters make it a more complex joining technique compared to some traditional welding methods.
▶ Is Laser Welding the Future?
Laser welding is widely considered a technology of the future, as it continues to advance in terms of cost-effectiveness, energy efficiency, and the range of materials and applications it can accommodate.
Its unique capabilities make it an increasingly attractive choice for modern manufacturing and fabrication industries.
Machine Recommendations for: Handheld Laser Welding Machine
Every Purchase Should be Well Informed
We can Help with Detailed Information and Consultation!
Post time: May-29-2024