Laser Welding Machine Welding Parameters Detailed Description
Laser welding is a precise and efficient method of joining materials, particularly metals.
Understanding the welding parameters is crucial for achieving optimal results.
This article outlines the essential principles and parameters that influence the effectiveness of laser welding, including the thickness of the material, wire diameter, power settings, and more.
Key Principles of Laser Welding
1. Material Thickness and Wire Diameter:
o When welding thicker materials, it is essential to use a thicker welding wire and a higher power setting.
Conversely, for thinner materials, a finer welding wire and lower power are suitable.
o For example, if the material thickness increases, the wire diameter should also increase proportionally, and the power should be adjusted to be higher while reducing the wire feed speed.
This ensures that enough energy penetrates the material for a solid weld.
2. Power Settings and Weld Appearance:
o The power setting directly influences the appearance of the weld.
Lower power tends to produce a whiter weld surface, while higher power results in a darker, more colored weld seam.
As the power increases, the weld may also transition from a multi-colored appearance to a predominantly black color, indicating that the weld is forming from a single side.
o This characteristic is crucial for assessing the quality of the weld and ensuring it meets the desired standards.
3. Wire Diameter Selection:
o Selecting the appropriate wire diameter is critical.
The diameter of the welding wire should not exceed the thickness of the material, and it should ideally be biased towards being thicker than the base material.
This selection significantly influences the fullness of the weld bead.
o A thicker wire can contribute to a more robust weld, while a wire that is too thin may result in insufficient fusion and a weaker joint.
4. Welding Wire Diameter and Scanning Width:
o The diameter of the welding wire also affects the scanning width of the laser beam.
A finer wire will necessitate a narrower scanning width, which can be advantageous for precision welding applications where fine details are required.
o This relationship allows for better control of the heat input and ensures the weld is focused on the desired area, minimizing potential damage to surrounding material.
Want to Know More Details
About Laser Welding?
External Factors Affecting Welding Parameters
It is important to note that various external factors, such as shielding gas and environmental conditions, can significantly impact the welding process.
Therefore, it is advisable to adjust the welding parameters based on real-time conditions.
• Shielding Gas: The type and flow rate of shielding gas can affect the weld quality and appearance.
Proper gas coverage can prevent oxidation and improve the overall finish.
• Environmental Conditions: Factors like temperature, humidity, and air flow can influence the performance of the laser welding machine and the properties of the weld.
Any other Information About Laser Welder?
Laser Welding Carbon Steel
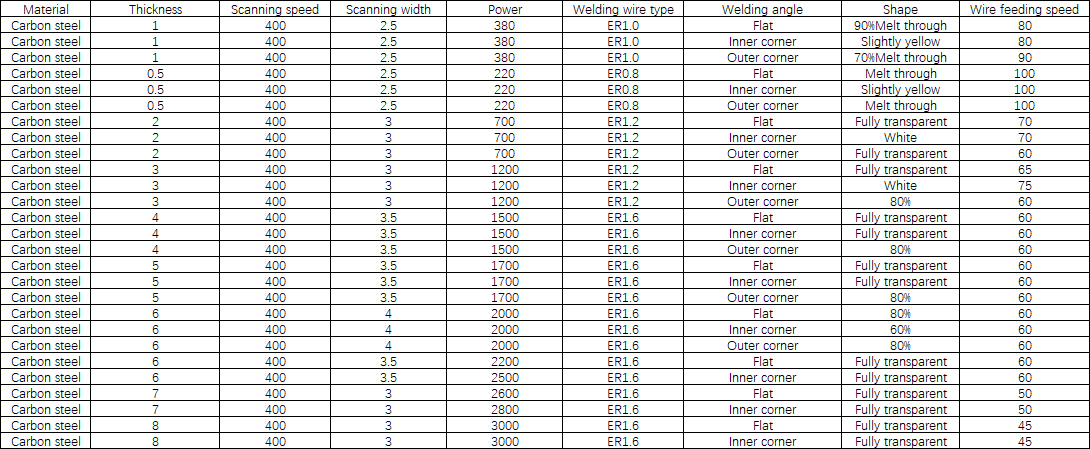
Note: Due to the influence of the zinc layer of the galvanized sheet, the power of the galvanized sheet can be appropriately lowered
Handheld Laser Welding Stainless Steel
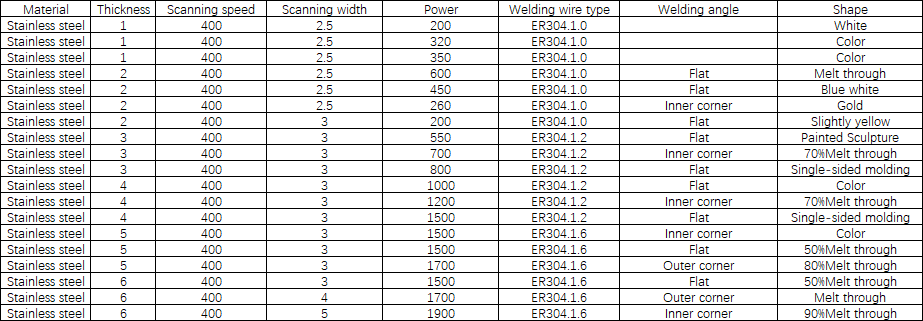
Notes:3000W stainless steel power reference carbon steel
Don't Know How to Choose Laser Machine?
We Can Help!
From Engaging Videos to Informative Articles
How to Use Handheld Laser Welder | Beginner Tutorial
Post time: Jan-06-2025