Laser welding technology has revolutionized the manufacturing and fabrication industries, offering unparalleled precision, speed, and versatility. This advanced welding method utilizes concentrated laser beams to melt and join materials, making it suitable for a wide range of applications.
One of the primary advantages of laser welding is its capability to work with various materials, enabling manufacturers to create strong, durable joints in diverse products.
In this article, we will explore the key materials that can be welded using laser welding machines, highlighting their unique properties and applications.
1. Laser Machine Welding Metals
a. Stainless Steel
Stainless steel is among the most commonly welded metals using laser technology. Known for its corrosion resistance and strength, stainless steel is widely used in industries such as food processing, pharmaceuticals, automotive manufacturing, and construction.
Laser welding provides high-quality, clean welds with minimal heat-affected zones (HAZ), ensuring that the material's properties remain intact. The ability to precisely control the laser's energy allows for the welding of thin and thick sections alike, making it suitable for intricate designs and complex assemblies.
b. Carbon Steel
Carbon steel is another metal that lends itself well to laser welding. This material is prevalent in construction and manufacturing, where it is used for structural components and machinery. Laser welding enhances the strength and durability of carbon steel welds while maintaining a high-quality finish.
The process is efficient, reducing the risk of warping and distortion often associated with traditional welding methods. Additionally, the speed of laser welding allows manufacturers to increase productivity without compromising quality.
c. Aluminum and Aluminum Alloys
Aluminum is valued for its lightweight and corrosion-resistant properties, making it a favored material in the aerospace and automotive industries. However, welding aluminum can be challenging due to its high thermal conductivity and susceptibility to heat-related issues.
Laser welding addresses these challenges by providing a focused heat source that minimizes heat input and reduces distortion. This technique allows for precise joining of aluminum components, enabling the production of lightweight structures with excellent mechanical properties.
d. Copper and Copper Alloys
Copper is known for its excellent electrical conductivity, making it essential in electrical applications such as wiring and circuit boards.
While welding copper can be difficult due to its high thermal conductivity and reflective surface, laser welding machines equipped with advanced settings can achieve successful results.
This technology enables the efficient joining of copper and its alloys, ensuring strong and reliable connections that are critical in electrical applications.
e. Nickel and Nickel Alloys
Nickel and its alloys are commonly used in high-temperature and corrosive environments, such as in the chemical and oil industries.
Laser welding provides an efficient and effective solution for joining these materials, ensuring that the welds maintain their integrity under extreme conditions.
The precision of laser welding is particularly beneficial in applications where the performance of the welded joint is critical.
2. Using A Laser Welding Plastics
In addition to metals, laser welding is also effective for a variety of plastics, expanding its applicability in diverse industries.
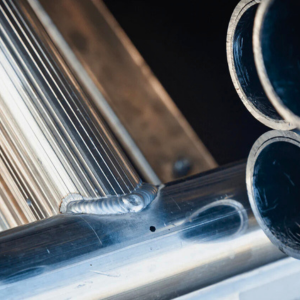
Metal Laser Welding Machine Aluminum

a. Polypropylene (PP)
Polypropylene is widely used in packaging, automotive components, and consumer goods. Laser welding allows for strong, seamless joints that can enhance the performance of polypropylene products.
The process is clean and efficient, reducing the need for additional adhesives or mechanical fasteners, which can save time and reduce costs.
b. Polyethylene (PE)
Polyethylene is another common plastic that can be welded using laser technology. It is used in applications ranging from containers to piping systems.Laser welding of polyethylene provides a robust joining method that can withstand various environmental conditions. The precision of the process ensures that the welds are strong and reliable, meeting the demands of critical applications.
c. Polycarbonate (PC)
Polycarbonate is prized for its impact resistance and optical clarity, making it an ideal choice for applications such as safety goggles and electronic displays. Laser welding offers a way to join polycarbonate components without compromising their structural integrity. This capability is particularly beneficial in industries where transparency and durability are essential.
d. Polyamide (Nylon)
Nylon, known for its strength and flexibility, is commonly used in automotive, textile, and consumer products. Laser welding can be employed to join nylon components effectively, providing strong bonds that can withstand mechanical stress. The ability to weld nylon using lasers opens new possibilities in product design and engineering.
Want to Buy a Laser Welder?
3. Laser Welding Composite Materials
As industries increasingly turn to composite materials for their unique properties, laser welding technology is adapting to meet these needs.
a. Metal-Plastic Composites
Metal-plastic composites combine the benefits of both materials, offering lightweight yet strong solutions for various applications.
Laser welding can effectively join these composites, making it a valuable technique in automotive and electronic manufacturing.
The ability to create strong joints without adding significant weight is a significant advantage in these industries.
b. Fiber-Reinforced Composites
These materials, which incorporate fibers into a resin matrix, are known for their high strength-to-weight ratios.
Laser welding technology can be applied to certain types of fiber-reinforced composites, allowing for precise joining that maintains the integrity of the fibers.
This capability is particularly useful in aerospace and automotive applications, where lightweight structures are critical for performance.
4. Laser Welding Machine Weld Emerging Applications
The versatility of laser welding technology is leading to its adoption in new and innovative applications.
Industries such as renewable energy are exploring the use of laser welding for solar panel production, where the ability to join dissimilar materials is essential.
Additionally, advancements in laser technology are enabling the welding of more complex materials, further expanding the scope of laser welding.
5. Conclusion
Laser welding machines are capable of joining a diverse array of materials, including metals, plastics, and composites.
The precision and efficiency of laser welding make it an ideal choice for various industries, including automotive, aerospace, electronics, and medical applications.
As technology continues to advance, the range of materials that can be effectively welded using lasers is likely to expand, further enhancing its versatility and applicability in modern manufacturing.
This adaptability positions laser welding as a critical process in achieving high-quality, durable products in an increasingly competitive market.

Laser Welder Welding Metal
Want To Know More About Laser Welder?
Related Machine: Laser Welders
The handheld fiber laser welder is designed with five parts: the cabinet, the fiber laser source, the circular water-cooling system, the laser control system, and the hand held welding gun.
The simple but stable machine structure makes it easier for the user to move the laser welding machine around and weld the metal freely.
The portable laser welder is commonly used in metal billboard welding, stainless steel welding, sheet metal cabinet welding, and large sheet metal structure welding.
The fiber laser welder machine is equipped with a flexible laser welding gun which helps you conduct the hand-held operation.
Depending on a fiber cable of a certain length, the stable and high-quality laser beam is transmitted from the fiber laser source to the laser welding nozzle.
That improves the safety index and is friendly to the beginner to operate the handheld laser welder.
Post time: Jan-06-2025