Filtration Fabric Laser Cutter:
Transforming the Filtration Industry
Introduction:
Key Things to Know Before Diving In
In the dynamic world of filtration, where quality and efficiency are paramount, the methods used to cut filtration fabrics play a crucial role in determining the overall effectiveness of filter products.
Traditional cutting methods have often struggled to meet the precise demands of this industry, leading to the adoption of advanced technologies like laser cutting, particularly CO₂ laser systems.
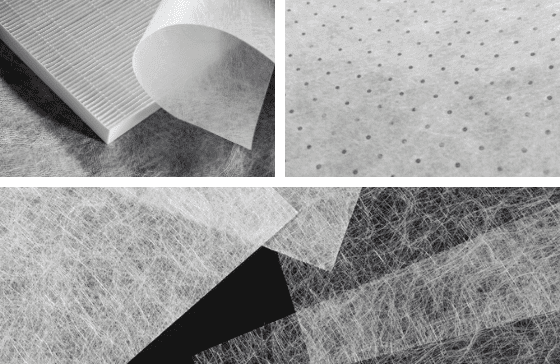
Filtration Fabric Applications
This article explores the benefits of eurolaser CO₂ laser cutting technology in the filtration industry.
Highlighting its precision, clean edges, and material versatility.
It also discusses applications across various sectors.
Demonstrating how laser cutting enhances productivity and improves the quality of filtration products.
This article delves into the comprehensive benefits of using laser cutters for filtration fabrics, emphasizing the advantages offered by CO₂ laser cutters.
1. Precision and Accuracy:
Laser cutting technology is renowned for its exceptional precision, allowing manufacturers to achieve cuts that meet stringent specifications.
This level of accuracy is particularly vital in the filtration industry, where even the slightest deviation can compromise the performance of a filter.
CO₂ lasers operate with a focused beam that can cut through various materials with minimal tolerance, ensuring that every piece of filtration fabric is tailored to exact dimensions.
2. Clean Edges and Enhanced Durability:
One of the most significant advantages of laser cutting is the production of clean, sealed edges.
The high heat generated by the laser not only cuts through materials but also melts and fuses the edges, preventing fraying.
This characteristic is crucial for filtration fabrics, as clean edges enhance the overall durability and lifespan of the products.
Additionally, the superior finish contributes to the aesthetic appeal, which can be important for consumer-facing applications.
3. Versatility in Material Handling:
Laser cutters are incredibly versatile and can handle a wide range of materials, including both synthetic fabrics and natural fibers.
This adaptability is particularly beneficial in the filtration industry, where manufacturers often need to switch between different materials depending on the application.
The ability to cut non-woven fabrics, foams, and composite materials without extensive reconfiguration allows for greater flexibility and responsiveness to market demands.
4. Reduced Material Waste:
Material efficiency is a crucial consideration in manufacturing.
Laser cutting minimizes waste by producing precise cuts that maximize the use of raw materials.
The ability to nest cuts closely together on a material sheet reduces off-cuts, allowing manufacturers to optimize their resources.
This reduction in waste not only lowers production costs but also minimizes the environmental impact, aligning with sustainability goals increasingly important in today’s market.
5. Speed and Efficiency:
The rapid cutting capabilities of laser technology significantly boost production rates.
Laser systems can operate continuously and at high speeds, enabling manufacturers to meet tight deadlines without sacrificing quality.
This efficiency is especially beneficial in industries where time-to-market is critical, as the ability to quickly produce high-quality filtration fabrics can provide a competitive edge.
6. Automation and Customization:
Modern laser cutting technology includes features like precision tension feeding and automatic sorting systems, which facilitate seamless integration into automated production lines.
This automation reduces the need for manual intervention, minimizing labor costs and the potential for human error.
Furthermore, working areas can be customized to accommodate specific production needs, enhancing operational flexibility.
In this video, we demonstrate the process of laser cutting filter fabric, highlighting the importance of selecting the right material and laser settings for optimal performance.
Watch as we prepare our design and set up the laser cutter, ensuring precise cuts for effective filtration.
Finally, we showcase the finished pieces and discuss their various applications in crafting and industrial uses!
Several materials are commonly used in the filtration industry and are well-suited for laser cutting:
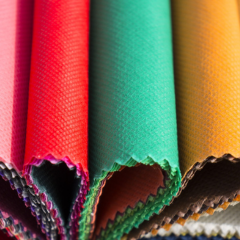
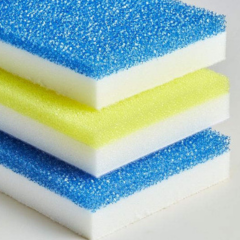
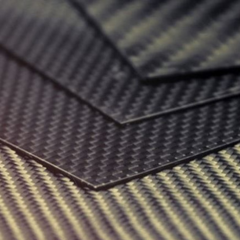
Non-Woven Fabrics
These are ideal for air and liquid filtration due to their excellent filtration properties and structural integrity.
Foams
Used extensively for sound and air filtration, foams can be cut precisely to meet specific design requirements.
Composite Materials
Offering enhanced durability and strength, these materials are essential for demanding filtration tasks that require robust solutions.
Advanced Material Compatibility
CO₂ laser cutters are specifically designed to handle a broad spectrum of technical textiles used in filter production.
Their engineering allows for the effective processing of materials such as non-woven fabrics, foams, and composite materials, which are often employed in various filtration applications.
This advanced compatibility ensures that manufacturers can achieve optimal results across diverse product lines.
Application Examples
The versatility of systems is evident in their application across multiple sectors, including:
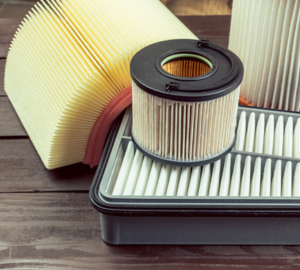
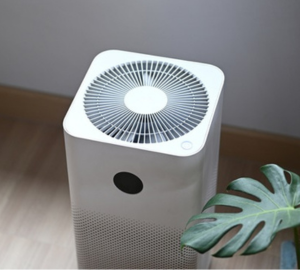
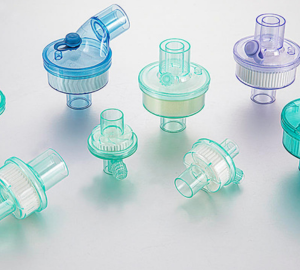
Automotive Filters:
Precision-cut filtration fabrics are essential for vehicle air and oil filtration systems, ensuring optimal performance and longevity.
Air Purification Systems:
High-quality filters made from meticulously cut fabrics are critical for maintaining air quality in residential and industrial settings.
Medical Devices:
In healthcare, effective filtration is vital in devices such as surgical masks and ventilators, where high standards of cleanliness and reliability are mandatory.
• Working Area (W *L): 1000mm * 600mm
• Laser Power: 60W/80W/100W
• Working Area (W *L): 1300mm * 900mm
• Laser Power: 100W/150W/300W
• Working Area (W *L): 1800mm * 1000mm
• Laser Power: 100W/150W/300W
In Conclusion
The integration of laser cutting technology, particularly through advanced systems like CO₂ laser cutters, has revolutionized the production of filtration fabrics.
With benefits ranging from precision and speed to material versatility, this technology enhances productivity and contributes to the overall quality and effectiveness of filtration products.
As the industry continues to evolve, laser cutting will undoubtedly remain at the forefront of innovation in the filtration sector, paving the way for improved filtration solutions that meet the growing demands of consumers and industries alike.
Q: Are There Safety Considerations When Using a Laser Cutter?
A: Yes, safety is crucial when operating a laser cutter. Key considerations include:
• Wearing appropriate personal protective equipment (PPE)
• Ensuring proper ventilation to avoid harmful fumes
• Following manufacturer guidelines for operation and maintenance
Q: What Should I Consider When Choosing a Laser Cutter for Filtration Fabrics?
A: Consider the following factors:
• Cutting area size: Ensure it meets your production needs.
• Laser power: Higher wattage allows cutting of thicker materials.
• Software compatibility: It should work seamlessly with your design software.
• Support and training: Look for manufacturers that offer comprehensive support and training.
Q: What is the Typical Maintenance Required for a Laser Cutter?
A: Regular maintenance may include:
• Cleaning the lens and mirrors
• Checking and replacing the laser tube as necessary
• Ensuring the cooling system is functioning properly
• Regular calibration and testing for accuracy
Q: Can Laser Cutters Handle Large Production Volumes?
A: Yes, modern laser cutters are designed for high throughput and can handle large production volumes efficiently, making them suitable for industrial applications.
Any Ideas about Filtration Laser Cutter,
Come to Tell Us!
Any Questions about Filter Cloth Laser Cutting Machine?
Post time: Jan-08-2025