How to Select the Best Gas Mixtures for Your Laser Welding?
Types, Benefits, and Applications
Introduction:
Key Things to Know Before Diving In
Laser welding is a high-precision welding method that uses a laser beam to melt the material of the workpiece and then forms a weld after cooling. In laser welding, gas plays a key role.
The protective gas not only affects the welding seam formation, welding seam quality, welding seam penetration, and penetration width but also directly affects the quality and efficiency of laser welding.
What gases are needed for laser welding? This article will take an in-depth look at the importance of laser welding gases, the gases used, and what they do.
We will also recommend the best laser welding machine for your needs.
Why Is Gas Needed For Laser Welding?
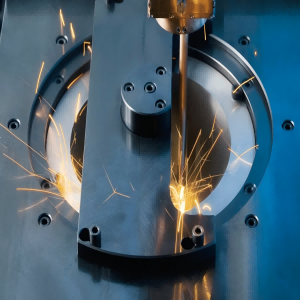
Laser Beam Welding
During the laser welding process, a high-energy-density laser beam is focused on the welding area of the workpiece.
Causing instantaneous melting of the surface material of the workpiece.
Gas is required during laser welding to protect the welding area.
Control the temperature, improve the quality of the weld, and protect the optical system.
Choosing the appropriate gas type and supply parameters are important factors in ensuring an efficient.
And stable laser welding process and obtaining high-quality welding results.
1. Protection Of Welding Areas
During the laser welding process, the weld area is exposed to the external environment and is easily affected by oxygen and other gases in the air.
Oxygen triggers oxidation reactions that may lead to reduced weld quality, and the creation of pores and inclusions. The weld can be effectively protected from oxygen contamination by supplying an appropriate gas, usually an inert gas such as argon, to the welding area.
2. Heat Control
Gas selection and supply can help control the temperature of the welding area. By adjusting the flow rate and type of gas, the cooling rate of the welding area can be affected. This is important to control the heat-affected zone (HAZ) during welding and reduce thermal distortion.
3. Improved Weld Quality
Some auxiliary gases, such as oxygen or nitrogen, can improve the quality and performance of welds. For example, adding oxygen can improve the penetration of the weld and increase the welding speed, while also affecting the shape and depth of the weld.
4. Gas Cooling
In laser welding, the welding area is usually affected by high temperatures. Using a gas cooling system can help control the temperature of the welding area and prevent overheating. This is essential to reduce thermal stress in the welding area and improve welding quality.
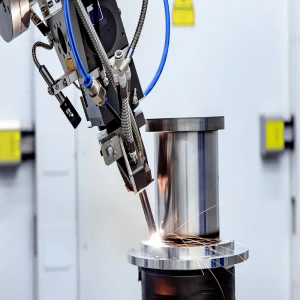
Automated Laser Beam Welding
5. Gas Protection Of Optical Systems
The laser beam is focused on the welding area through an optical system.
During the soldering process, the molten material and aerosols generated may contaminate optical components.
By introducing gases into the welding area, the risk of contamination is reduced and the life of the optical system is extended.
Which Gases Are Used In Laser Welding?
In laser welding, the gas can isolate the air from the welding plate and prevent it from reacting with the air. This way, the welding surface of the metal plate will be whiter and more beautiful. Using gas also protects the lenses from welding dust. Usually, the following gases are used:
1. Protective Gas:
Shielding gases, sometimes called “inert gases,” play an important role in the laser welding process. Laser welding processes often use inert gases to protect the weld pool. The commonly used protective gases in laser welding mainly include argon and neon. Their physical and chemical properties are different, so their effects on the weld are also different.
Protective Gas: Argon
Argon is one of the most commonly used inert gases.
It has a high degree of ionization under the action of the laser, which is not conducive to controlling the formation of plasma clouds, which will have a certain impact on the effective use of lasers.
The inert nature of argon keeps it out of the soldering process, while it also dissipates heat well, helping to control the temperature in the soldering area.
Protective Gas: Neon
Neon is often used as an inert gas, similar to argon, and is mainly used to protect the welding area from oxygen and other pollutants in the external environment.
It is important to note that neon is not suitable for all laser welding applications.
It is mainly used for some special welding tasks, such as welding thicker materials or when deeper weld seams are required.
2. Auxiliary Gas:
During the laser welding process, in addition to the main protective gas, auxiliary gases can also be used to improve welding performance and quality. The following are some common auxiliary gases used in laser welding.
Auxiliary Gas: Oxygen
Oxygen is commonly used as an assist gas and can be used to increase heat and weld depth during welding.
Adding oxygen can increase welding speed and penetration, but needs to be carefully controlled to avoid excess oxygen causing oxidation problems.
Auxiliary Gas: Hydrogen/ Hydrogen Mixture
Hydrogen improves the quality of welds and reduces the formation of porosity.
Mixtures of argon and hydrogen are used in some special applications, such as welding stainless steel. The hydrogen content of the mixture typically ranges from 2% to 15%.
Protective Gas: Nitrogen
Nitrogen is also often used as an auxiliary gas in laser welding.
The ionization energy of nitrogen is moderate, higher than argon and lower than hydrogen.
The ionization degree is generally under the action of a laser. It can better reduce the formation of plasma clouds, provide higher quality welds and appearance, and reduce the impact of oxygen on the welds.
Nitrogen can also be used to control the temperature of the welding area and reduce the formation of bubbles and pores.
Protective Gas: Helium
Helium is usually used for high-power laser welding because it has low thermal conductivity and is not easily ionized, allowing the laser to pass smoothly and the beam energy to reach the workpiece surface without any obstacles.
Conducive to higher power welding. Helium can also be used to improve weld quality and control welding temperatures. This is the most effective shielding gas used in laser welding, but it is relatively expensive.
3. Cooling Gas:
Cooling gas is often used during laser welding to control the temperature of the welding area, prevent overheating, and maintain welding quality. The following are some commonly used cooling gases:
Cooling Gas/ Medium: Water
Water is a common cooling medium often used to cool laser generators and laser welding optical systems.
Water cooling systems can help maintain a stable temperature of the laser generator and optical components to ensure laser beam stability and performance.
Cooling Gas/ Medium: Atmospheric Gases
In some laser welding processes, ambient atmospheric gases can be used for cooling.
For example, in the optical system of a laser generator, the surrounding atmosphere gas can provide a cooling effect.
Cooling Gas/ Medium: Inert Gases
Inert gases such as argon and nitrogen can also be used as cooling gases.
They have lower thermal conductivity and can be used to control the temperature of the welding area and reduce the heat-affected zone (HAZ).
Cooling Gas/ Medium: Liquid Nitrogen
Liquid nitrogen is an extremely low-temperature cooling medium that can be used for extremely high-power laser welding.
It provides a very effective cooling effect and ensures temperature control in the welding area.
4. Mixed Gas:
Gas mixtures are commonly used in welding to optimize various aspects of the process, such as welding speed, penetration depth, and arc stability. There are two main types of gas mixtures: binary and ternary mixtures.
Binary Gas Mixtures: Argon + Oxygen
Adding a small amount of oxygen to argon improves arc stability, refines the weld pool, and increases welding speed. This mixture is commonly used for welding carbon steel, low-alloy steel, and stainless steel.
Binary Gas Mixtures: Argon + Carbon Dioxide
The addition of CO₂ to argon increases welding strength and corrosion resistance while reducing spatter. This mixture is often used for welding carbon steel and stainless steel.
Binary Gas Mixtures: Argon + Hydrogen
Hydrogen increases arc temperature, improves welding speed, and reduces welding defects. It is especially useful for welding nickel-based alloys and stainless steel.
Ternary Gas Mixtures: Argon + Oxygen + Carbon Dioxide
This mixture combines the benefits of both argon-oxygen and argon-CO₂ mixtures. It reduces spatter, improves weld pool fluidity, and enhances weld quality. It is widely used for welding various thicknesses of carbon steel, low-alloy steel, and stainless steel.
Ternary Gas Mixtures: Argon + Helium + Carbon Dioxide
This mixture helps improve arc stability, increases weld pool temperature, and enhances welding speed. It is used in short-circuit arc welding and heavy welding applications, offering better control over oxidation.
Gas Selection In Different Applications
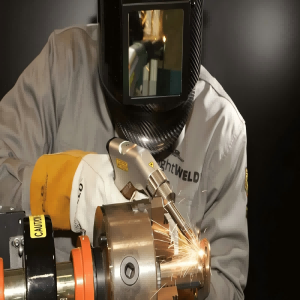
Handheld Laser Welding
In different applications of laser welding, choosing the appropriate gas is crucial, because different gas combinations can produce different welding quality, speed, and efficiency. Here are some guidelines to help you choose the right gas for your specific application:
Type of Welding Material:
Stainless Steel typically uses Argon or Argon/Hydrogen Mixture.
Aluminum and Aluminum Alloys often use Pure Argon.
Titanium Alloys often use Nitrogen.
High-Carbon Steels often use Oxygen as an Auxiliary Gas.
Welding Speed And Pentration:
If higher welding speed or deeper welding penetration is required, the gas combination can be adjusted. Adding oxygen often improves speed and penetration, but needs to be carefully controlled to avoid oxidation problems.
Control Of Heat Affected Zone (HAZ):
Depending on the material being cleaned, hazardous waste that requires special handling procedures may be generated during the cleaning process. This can add to the overall cost of the laser cleaning process.
Weld Quality:
Some gas combinations can improve the quality and appearance of welds. For example, nitrogen can provide a better appearance and surface quality.
Pore And Bubble Control:
For applications that require very high-quality welds, special attention needs to be paid to the formation of pores and bubbles. Proper gas selection can reduce the risk of these defects.
Equipment And Cost Considerations:
Gas selection is also influenced by equipment type and cost. Some gases may require special supply systems or higher costs.
For specific applications, it is recommended to work with a welding engineer or a professional laser welding equipment manufacturer to obtain professional advice and optimize the welding process.
Some experimentation and optimization are usually required before the final gas combination is selected.
Depending on the specific application, different gas combinations and parameters can be tried to find the optimal welding conditions.
Things You Need To Know About: Handheld Laser Welding
Recommended Laser Welding Machine
To optimize your metalworking and material processing tasks, selecting the right equipment is essential. MimoWork Laser recommends the Handheld Laser Welding Machine for precise and efficient metal joining.
High-Capacity & Wattage for Various Welding Applications
The 2000W handheld laser welding machine is characterized by small machine size but sparkling welding quality.
A stable fiber laser source and connected fiber cable provide a safe and steady laser beam delivery.
With the high power, the laser welding keyhole is perfectible and enables the welding joint firmer even for thick metal.
With a compact and small machine appearance, the portable laser welder machine is equipped with a moveable handheld laser welder gun which is lightweight and convenient for multi-laser welding applications at any angle and surface.
Optional various types of laser welder nozzles and automatic wire feeding systems make laser welding operation easier and that is friendly for beginners.
High-speed laser welding greatly increases your production efficiency and output while enabling an excellent laser welding effect.
Summarize
In short, laser welding needs to use gas to protect welding areas, control temperature, improve weld quality, and protect optical systems. Selecting appropriate gas types and supply parameters is an important factor in ensuring an efficient and stable laser welding process and obtaining high-quality welding results. Different materials and applications may require different types and mixed proportions to meet specific welding requirements.
Reach out to us today to learn more about our laser cutters and how they can optimise your cutting production process.
Related Links
Any Ideas About Laser Welding Machines?
Post time: Jan-13-2025