Is Laser Cutting the Best Choice for Filter Cloth?
Types, Benefits, and Applications
Introduction:
Key Things to Know Before Diving In
Laser cutting technology has revolutionized the processing of materials in various industries. Among these, the use of laser cutting for filter cloth stands out for its precision, efficiency, and versatility. Filter cloth, essential in industries like water treatment, air filtration, pharmaceuticals, and food processing, demands high-quality cutting methods to maintain its functionality.
This article examines whether laser cutting is suitable for filter cloth, compares it with other cutting methods, and highlights the advantages of laser cutting filter cloth. We’ll also recommend the best filter cloth laser cutting machines tailored for your needs.
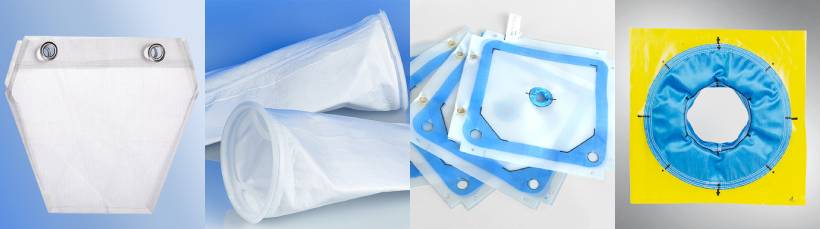
Filter cloth materials like polyester, nylon, and polypropylene are designed for applications where they trap particles while allowing liquids or gases to pass through. Laser cutting excels in processing these materials because it delivers:
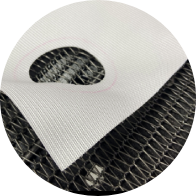
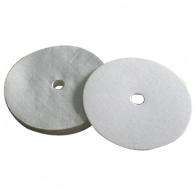
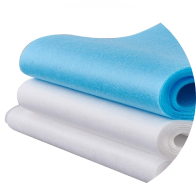
1. Clean Edges
Laser cutting filter cloth provides sealed edges, preventing fraying and enhancing the longevity of filter cloths.
2. High Precision
The filter cloth laser cutting machine has a fine but powerful laser beam that can cut precise shapes and special designs. It is suitable for customized or high-value filter materials.
3. Customization
A laser cutter can handle intricate designs and unique shapes, essential for specialized filtration needs.
4. High Efficiency
Filter cloth laser cutting systems operate at high speeds, making them perfect for bulk production.
5. Minimal Material Waste
Unlike traditional methods, laser cutting reduces material waste through optimized patterns and precise cutting.
6. High Automation
The filter cloth laser cutting system is easy to operate, thanks to the CNC system and intelligent laser cutting software. One person can control the laser machine and achieve mass production in a short time.
While laser cutting has proven to be highly effective for filter cloth, there are several other methods that are commonly used for cutting fabrics. Let’s explore them briefly:
1. Mechanical Cutting:
Common tools like rotary cutters are economical but prone to frayed edges and inconsistent results, especially in detailed designs.
Traditional cutting methods such as rotary cutters or fabric knives are commonly used for cutting filter cloth. However, these methods can cause fraying at the edges, which may affect the integrity of the fabric, especially in precision applications like filtration.
2. Die Cutting:
Efficient for simple, repetitive shapes in mass production but lacks flexibility for custom or intricate designs.
Die-cutting is often used for mass production of filter cloth parts, particularly when simple shapes are required. While die cutting can be efficient, it doesn't offer the same level of precision or flexibility as laser cutting, especially when dealing with more intricate designs.
3. Ultrasonic Cutting:
Effective for certain fabrics but limited in versatility compared to filter cloth laser cutters, particularly for complex or large-scale jobs.
Ultrasonic cutting uses high-frequency sound waves to cut materials. It is useful for certain applications but may not be as versatile or efficient as laser cutting for all types of filter cloth.
Conclusion:
Laser cutting outperforms these methods by delivering precision, versatility, and efficiency, all without physical contact or tool wear.
Laser cutting provides a precise, sealed edge that prevents fraying. This is particularly crucial for materials like polyester or nylon, which can unravel easily if not properly cut. The laser's heat also sterilizes the cut edges, reducing the risk of contamination, which is important in medical or food industry applications.
Whether you need to cut intricate perforations, specific shapes, or custom designs, laser cutting can be tailored to meet your needs. The precision allows for complex cuts that traditional methods cannot replicate.
Unlike die cutters or mechanical blades, lasers do not experience wear and tear. This means there’s no need for blade replacements, which can lead to cost savings and reduced downtime.
Laser cutting filter cloth works by focusing a high-powered laser beam on the material, which melts or vaporizes the material at the point of contact. The laser beam is controlled with great precision by a CNC (Computer Numerical Control) system, allowing it to cut through or engrave various filter cloth materials with exceptional accuracy.
Each type of filter cloth requires specific settings to ensure optimal cutting results. Here’s a look at how laser cutting filter cloth works for some of the most common filter cloth materials:
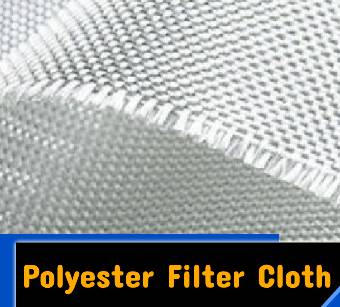
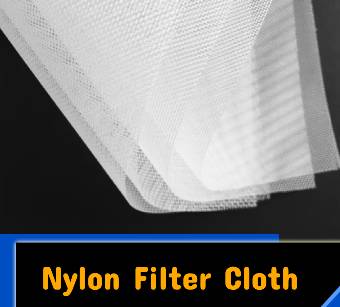
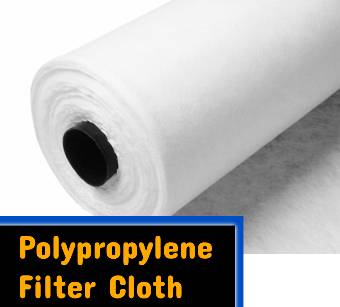
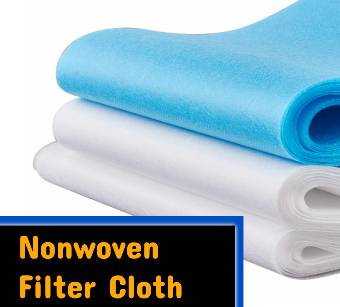
Laser Cut Polyester:
Polyester is a synthetic fabric that reacts well to laser cutting filter cloth.
The laser cuts smoothly through the material, and the heat from the laser beam seals the edges, preventing any unraveling or fraying.
This is especially important in filtration applications where clean edges are essential for maintaining the integrity of the filter.
Laser Cut Nonwoven Fabrics:
Nonwoven fabrics are lightweight and delicate, making them well-suited for laser cutting filter cloth. The laser can quickly cut through these materials without damaging their structure, providing clean cuts that are essential for producing precise filter shapes. Laser cutting filter cloth is particularly beneficial for nonwoven fabrics used in medical or automotive filtration applications.
Laser Cut Nylon:
Nylon is a strong, flexible material that is ideal for laser cutting filter cloth. The laser beam easily cuts through nylon and creates sealed, smooth edges. Additionally, laser cutting filter cloth does not cause distortion or stretching, which is often a problem with traditional cutting methods. The high precision of laser cutting filter cloth ensures that the final product maintains the necessary filtration performance.
Laser Cut Foam:
Foam filter materials are also suitable for laser cutting filter cloth, especially when precise perforations or cuts are required. Laser cutting filter cloth like foam allows for intricate designs and ensures that the edges are sealed, which prevents the foam from degrading or losing its structural properties. However, care must be taken with settings to prevent excessive heat buildup, which could cause burning or melting.
• Working Area (W *L): 1000mm * 600mm
• Laser Power: 60W/80W/100W
• Working Area (W *L): 1300mm * 900mm
• Laser Power: 100W/150W/300W
• Working Area (W *L): 1800mm * 1000mm
• Laser Power: 100W/150W/300W
In Conclusion
Laser cutting is undoubtedly a highly effective and efficient method for cutting filter cloth. Its precision, speed, and versatility make it a top choice for industries that require high-quality, custom cuts. If you're in need of a reliable and efficient laser cutting machine for filter cloth, MimoWork’s range of laser cutting machines provides excellent options to suit both small and large-scale production needs.
Reach out to us today to learn more about our laser cutting machines and how they can optimize your filter cloth production process.
Q: What types of filter cloth are suitable for laser cutting?
A: Materials like polyester, polypropylene, and nylon are ideal. The system also works for mesh fabrics and foam.
Q: How does a filter cloth laser cutter improve production efficiency?
A: By automating the cutting process and delivering precise, clean cuts without manual intervention, leading to faster production cycles.
Q: Can laser cutting handle intricate designs for filter cloth?
A: Absolutely. Laser systems excel in creating detailed patterns and custom shapes that traditional methods can’t achieve.
Q: Are filter cloth laser cutting machines easy to operate?
A: Yes, most machines feature user-friendly software and automation, requiring minimal training for operators.
Any Ideas about Laser Cutting Filter Cloth, Welcome to Discuss with Us!
Any Questions about Filter Cloth Laser Cutting Machine?
Post time: Nov-18-2024