Laser Welding Aluminum: Key Notes
Its Advantages, Challenges, and Applications
Quick Navigation:
Laser welding involves using a laser beam to melt and fuse aluminum components together.
It is valued for its precision, minimal heat-affected zone, and the ability to weld thin materials with high speed.
Laser welding aluminum is a specialized process that offers precision and high-quality welds but comes with its own set of challenges and considerations.
Here’s a comprehensive guide to help you navigate this technique effectively:
Laser Welding Aluminum: The Perfect Combination
Laser welding has become increasingly popular in industrial applications due to its precision, speed, and flexibility.
However, one of the main challenges in laser welding machines is the welding of aluminum.
A material that is notoriously difficult to weld due to its high thermal conductivity and low melting point.
In this article, we will discuss the advantages and challenges of laser welding aluminum, as well as its applications in various industries.
Advantages of Aluminum Laser Welding
Laser welder offers several advantages over traditional welding methods when it comes to aluminum welding:
Minimal Heat-Affected Zone (HAZ):
Welding with a laser produces a much narrower heat-affected zone (HAZ) compared to other welding methods.
This reduces the chances of cracking and distortion, which are common problems in aluminum welding.
Versatility:
Capable of welding thin sections and complex geometries.
This is particularly advantageous when welding aluminum, as it is a highly reflective material that can cause problems with other welding methods.
Non-Contact Welding:
Laser welding is a non-contact process, which means that the welding torch does not need to come into contact with the material being welded.
High Precision:
Laser welding can be carried out with high precision, resulting in neat and clean welds with minimal spatter, which allows for tight tolerances and high-quality welds.
Don't Know Where to Start? Here a Little Something We Wrote:
Challenges of Laser Welding Aluminum

While laser welding offers several advantages over aluminum welding, it also presents several challenges.
High Thermal Conductivity of Aluminum: Which means that a lot of heat is dissipated quickly, resulting in a shallow penetration depth.
This can be overcome by using a high-power laser, but this can also increase the chances of cracking and distortion.
Low melting point of Aluminum: Which means that it is more prone to melting and vaporization during welding. This can result in porosity and poor weld quality.
Highly Reflective Nature of Aluminum: It can cause problems with laser beam absorption, which can affect the quality of the weld.
Aluminum Laser Welding: Some Field-Tested Suggestions
Material Preparation:
Surface Cleanliness: Aluminum should be clean and free from oxides, oils, and other contaminants.
Edge Preparation: Proper edge preparation can improve weld quality, especially for thicker sections.
Optimize Parameters:
Laser Power & Welding Speed: Adjust based on material thickness and type. High speeds can reduce heat input but may require careful control.
Focal Spot Size: A smaller spot size offers greater precision but may require fine-tuning of power and speed.
Use Proper Shielding:
Argon or Helium: Protects the weld pool from oxidation and contamination.
Maintain a Clean Environment: Ensure that the welding area is free of contaminants and debris.
Choose the Right Laser Type:
Continuous Wave (CW) Lasers are Ideal for high-speed welding and deeper welds.
Pulsed Lasers are Suitable for thin materials and precision applications.
Fixture and Alignment:
Precise Fixturing: Ensure that parts are accurately aligned and secured to avoid distortion or misalignment during welding.
Joint Design: Optimize joint design to accommodate the laser’s characteristics and reduce potential defects.
Still Having Troubles with Aluminum Laser Welding?
Applications of Laser Welding Aluminum
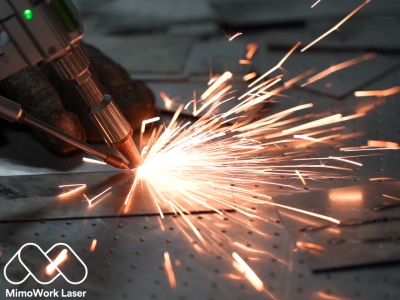
Despite the challenges associated with laser welding aluminum, it is still widely used in various industries.
The aerospace industry, for example, uses laser welder to join aluminum alloys for aircraft structures.
The automotive industry also uses laser welding to join aluminum components in cars and trucks.
Resulting in lighter vehicles with improved fuel efficiency.
Additionally, the electronics industry uses laser welding to join aluminum components in electronic devices.
As well as to produce fine and intricate structures for microelectronics.
Handheld Laser Weld: Video Demonstrations
5 things about Laser Welder Handheld
Welding with laser offers several advantages for aluminum welding, including precision, speed, and flexibility.
However, it also presents several challenges, such as the high thermal conductivity and low melting point of aluminum.
Despite these challenges, laser welding aluminum is still widely used in various industries, including aerospace, automotive, and electronics.
As laser welding technology continues to improve, we will likely see even more applications for aluminum welding in the future.
Some Key Notes for: Laser Welding Aluminum
Heat Sensitivity: Aluminum has a low melting point and high thermal conductivity, which means it requires precise control of laser parameters to avoid overheating or burn-through.
Oxide Layers: Aluminum forms an oxide layer that can affect weld quality. Ensure that it’s properly cleaned or use techniques like laser cleaning to remove it before welding.
Laser Interaction with Aluminum: Aluminum’s high reflectivity at certain wavelengths can be problematic.
Using a laser with a suitable wavelength and optimizing the focus can help mitigate this issue.
Distortion and Warping: Rapid heating and cooling can lead to warping or distortion.
Controlled heat input and proper cooling techniques can minimize these effects.
Reflectivity: Aluminum’s high reflectivity can lead to reduced efficiency and potential damage to the laser optics.
Use coatings or specific wavelengths designed to handle reflective materials.
Quality Control: Regularly monitor welds for consistency and defects.
Techniques such as ultrasonic testing or visual inspection can help maintain quality.
Thermal Management: Effective cooling and heat dissipation are crucial to prevent overheating and ensure weld quality.
Training and Expertise: Ensure that operators are well-trained in laser welding techniques and familiar with the specific requirements for aluminum.
Safety Considerations: Always use appropriate safety equipment, including eye protection and ventilation systems, to handle the high-intensity laser and potential fumes.
Don't Know Where to Start? Lets Start Here with Handheld Laser Welding Machine
Every Purchase Should be Well Informed
We can Help with Detailed Information and Consultation!
Post time: Mar-24-2023