Using Lasers in the Automotive Manufacturing Industry
Since Henry Ford introduced the first assembly line in the automotive manufacturing industry in 1913, car manufacturers have been continuously striving to optimize their processes with the ultimate goal of reducing assembly time, lowering costs, and increasing profits. Modern automotive production is highly automated, and robots have become commonplace throughout the industry. Laser technology is now being integrated into this process, replacing traditional tools and bringing many additional advantages to the manufacturing process.

The automotive manufacturing industry utilizes various materials, including plastics, textiles, glass, and rubber, all of which can be successfully processed using lasers. In fact, laser-processed components and materials are found in almost every area of a typical vehicle, both internally and externally. Lasers are applied at various stages of the car manufacturing process, from design and development to final assembly. Laser technology is not limited to mass production and is even finding applications in high-end custom car manufacturing, where production volumes are relatively low and certain processes still require manual work. Here, the goal is not to expand or accelerate production, but rather to improve processing quality, repeatability, and reliability, thus reducing waste and the costly misuse of materials.
Laser: Plastic Parts Processing Powerhouse

The most extensive applications of lasers is in the processing of plastic parts. This includes interior and dashboard panels, pillars, bumpers, spoilers, trims, license plates, and light housings. Automotive components can be made from various plastics such as ABS, TPO, polypropylene, polycarbonate, HDPE, acrylic, as well as various composites and laminates. The plastics can be exposed or painted and may be combined with other materials, such as fabric-covered interior pillars or support structures filled with carbon or glass fibers for added strength. Lasers can be used to cut or drill holes for mounting points, lights, switches, parking sensors.
Transparent plastic headlamp housings and lenses often require laser trimming to remove the waste left after injection molding. Lamp parts are usually made of polycarbonate for their optical clarity, high impact resistance, weather resistance, and resistance to UV rays. Although laser processing may result in a rough surface on this specific plastic, the laser-cut edges are not visible once the headlight is fully assembled. Many other plastics can be cut with high-quality smoothness, leaving clean edges that require no post-processing cleaning or further modification.
Laser Magic: Breaking Boundaries in Operations
Laser operations can be performed in areas that are inaccessible to traditional tools. Since laser cutting is a non-contact process, there is no tool wear or breakage, and lasers require minimal maintenance, resulting in minimal downtime. Operator safety is ensured as the entire process takes place within a closed space, eliminating the need for user intervention. There are no moving blades, eliminating associated safety hazards.

Plastic cutting operations can be performed using lasers with power ranging from 125W to higher, depending on the time required to complete the task. For most plastics, the relationship between laser power and processing speed is linear, meaning that to double the cutting speed, the laser power must be doubled. When evaluating the total cycle time for a set of operations, processing time must also be considered to appropriately select the laser power.
Beyond Cutting & Finishing: Expanding Laser's Plastic Processing Power

The laser applications in plastic processing are not limited to cutting and trimming alone. In fact, the same laser cutting technology can be used for surface modification or paint removal from specific areas of plastic or composite materials. When parts need to be bonded to a painted surface using adhesive, it is often necessary to remove the top layer of paint or roughen the surface to ensure good adhesion. In such cases, lasers are used in conjunction with galvanometer scanners to rapidly pass the laser beam over the required area, providing enough energy to remove the surface without damaging the bulk material. Precise geometries can be easily achieved, and removal depth and surface texture can be controlled, allowing for easy modification of the removal pattern as needed.
Of course, cars are not entirely made of plastic, and lasers can also be used to cut other materials used in automotive manufacturing. Car interiors typically include various textile materials, with upholstery fabric being the most prominent. The cutting speed depends on the type and thickness of the fabric, but higher-power lasers cut at correspondingly higher speeds. Most synthetic fabrics can be cleanly cut, with sealed edges to prevent fraying during subsequent stitching and assembly of car seats.
Genuine leather and synthetic leather can also be cut in the same way for automotive interior materials. Fabric coverings often seen on interior pillars in many consumer vehicles are also frequently precision processed using lasers. During the injection molding process, fabric is bonded to these parts, and excess fabric needs to be removed from the edges before installation in the vehicle. This is also a 5-axis robotic machining process, with the cutting head following the contours of the part and trimming the fabric precisely. In such cases, Luxinar's SR and OEM series lasers are commonly used.
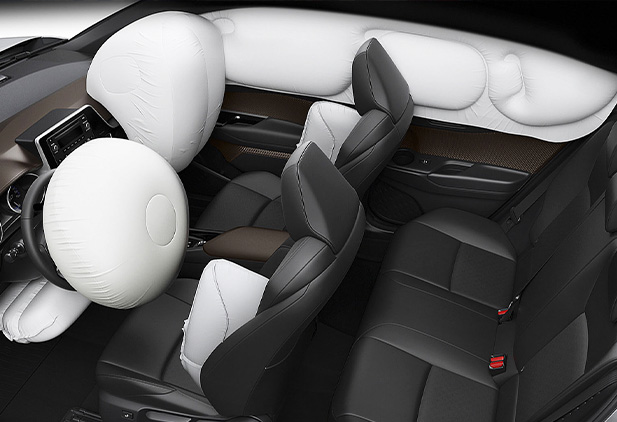
Laser Advantages in Automotive Manufacturing
Laser processing offers numerous advantages in the automotive manufacturing industry. In addition to providing consistent quality and reliability, laser processing is highly flexible and adaptable to the wide range of components, materials, and processes used in automotive manufacturing. Laser technology enables cutting, drilling, marking, welding, scribing, and ablation. In other words, laser technology is highly versatile and plays a vital role in driving the continuous development of the automotive industry.
As the automotive industry continues to evolve, car manufacturers are finding new ways to utilize laser technology. Currently, the industry is undergoing a fundamental shift towards electric and hybrid vehicles, introducing the concept of "electric mobility" by replacing traditional internal combustion engines with electric drivetrain technology. This requires manufacturers to adopt many new components and manufacturing processes
▶ Want to Get Started Right Away?
What About These Great Options?
Having Trouble Getting Started?
Contact Us for Detailed Customer Support!
▶ About Us - MimoWork Laser
We Don't Settle for Mediocre Results, Neither Should You
Mimowork is a results-oriented laser manufacturer, based in Shanghai and Dongguan China, bringing 20-year deep operational expertise to produce laser systems and offer comprehensive processing and production solutions to SMEs (small and medium-sized enterprises) in a wide array of industries.
Our rich experience of laser solutions for metal and non-metal material processing is deeply rooted in worldwide advertisement, automotive & aviation, metalware, dye sublimation applications, fabric and textiles industry.
Rather than offering an uncertain solution that requires purchase from unqualified manufacturers, MimoWork controls every single part of the production chain to make sure our products have constant excellent performance.

MimoWork has been committed to the creation and upgrade of laser production and developed dozens of advanced laser technology to further improve clients' production capacity as well as great efficiency. Gaining many laser technology patents, we are always concentrating on the quality and safety of laser machine systems to ensure consistent and reliable processing production. The laser machine quality is certificated by CE and FDA.
Get More Ideas from Our YouTube Channel
The Secret of laser Cutting?
Contact Us for Detailed Guides
Post time: Jul-13-2023