What is MDF? How to Improve Processing Quality?
Laser Cut MDF
At present, among all the popular materials used in furniture, doors, cabinets, and interior decoration, in addition to solid wood, the other widely used material is MDF.
Meanwhile, with the development of laser cutting technology and other CNC machines, many people from pros to hobbyists now have another affordable cutting tool to accomplish their projects.
The more choices, the more confusion. People always have trouble deciding which kind of wood they should choose for their project and how the laser works on the material. So, MimoWork would like to share as much knowledge and experience as possible for your better understanding of wood and laser cutting technology.
Today we are going to talk about the MDF, the differences between it and solid wood, and some tips to help you get a better cutting result of MDF wood. Let's get started!
Know about What is MDF
-
1. Mechanical properties:
MDF has a uniform fiber structure and strong bonding strength between fibers, so its static bending strength, plane tensile strength, and elastic modulus are better than Plywood and particle board/chipboard.
-
2. Decorating properties:
Typical MDF has a flat, smooth, hard, surface. Perfect to be used to make panels with wood frames, crown molding, out-of-reach window casings, painted architectural beams, etc., and easy to finish and save paint.
-
3. Processing properties:
MDF can be produced from a few millimeters to tens of millimeters thickness, it has excellent machinability: no matter sawing, drilling, grooving, tenoning, sanding, cutting, or engraving, the edges of the board can be machined according to any shape, resulting in a smooth and consistent surface.
-
4. Practical performance:
Good heat insulation performance, not aging, strong adhesion, can be made of sound insulation and sound-absorbing board. Due to the above excellent characteristics of MDF, it has been used in high-end furniture manufacturing, interior decoration, audio shell, musical instrument, vehicle, and boat interior decoration, construction, and other industries.

1. Lower costs
As MDF is made from all kinds of wood and its processing leftovers and plant fibers through a chemical process, it can be manufactured in bulk. Therefore, it has a better price compared to solid wood. But MDF can have the same durability as solid wood with proper maintenance.
And it is popular among hobbyists and self-employed entrepreneurs who use MDF to make name tags, lighting, furniture, decorations, and much more.
2. Machining convenience
We solicited many experienced carpenters, they appreciate that MDF is decent for trim work. It's more flexible than wood. Also, it is straight when it comes to installing which is a great advantage for workmen.
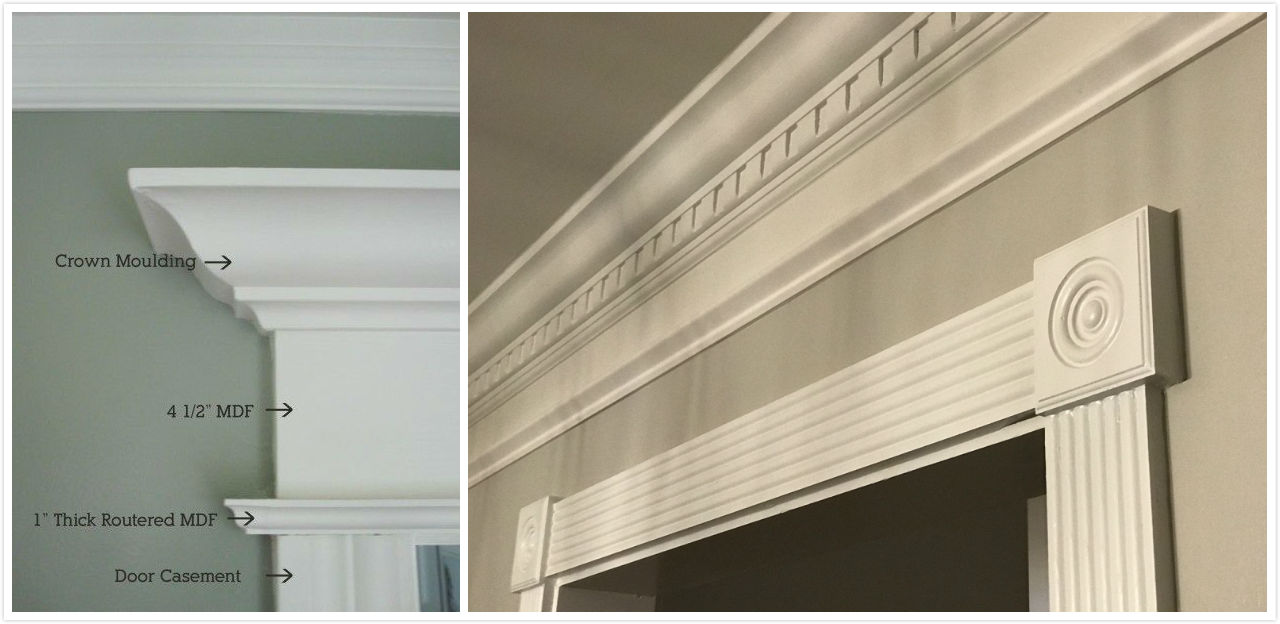
3. Smooth surface
The surface of MDF is smoother than solid wood, and no need to worry about knots.
Easy painting is also a big advantage. We recommend you to do your first priming with a quality oil-based primer instead of aerosol spray primers. The latter one would soak right into the MDF and result in a rough surface.
Moreover, because of this character, MDF is people's first choice for veneer substrate. It allows MDF to be cut and drilled by a wide variety of tools such as a scroll saw, jigsaw, band saw, or laser technology without damage.
4. Consistent structure
Because MDF is made of fibers, it has a consistent structure. MOR (modulus of rupture)≥24MPa. Many people are concerned about whether their MDF board would crack or warp if they plan to use it in damp areas. The answer is: Not really. Unlike some kinds of wood, even it comes to an extreme change in humidity and temperature, the MDF board would just move as a unit. Also, some boards provide better water resistance. You can simply choose MDF boards that have been specially made to be highly water-resistant.

5. Excellent absorption of painting
One of the greatest strengths of MDF is that it lends itself perfectly to being painted. It can be varnished, dyed, lacquered. It gets along with solvent-based paint very well, like oil-based paints, or water-based paints, like acrylic paints.
1. Demanding maintenance
If MDF is chipped or cracked, you cannot repair or cover it easily. Therefore, if you want to expend the service life of your MDF goods, you must be sure to caulk it with primer, seal any rough edges and avoid the holes left in the wood where edges are routed.
2. Unfriendly to mechanical fasteners
The solid wood will close on a nail, but the MDF doesn't hold mechanical fasteners very well. Its bottom line it's not as strong as wood that could be easy to strip the screw holes. To avoid this from happening, please pre-drill holes for nails and screws.
3. Not recommended keeping in high-moisture location
Although there are now water-resistant varieties on the market today that can be used outdoors, in bathrooms, and basements. But if the quality and post-processing of your MDF are not standard enough, you never know what is going to happen.
4. Noxious gas and dust
As MDF is a synthetic building material that contains VOCs (eg. urea-formaldehyde), dust generated during the manufacture could be harmful to your health. Small amounts of formaldehyde may be off-gassed during cutting, so protective measures need to be taken while cutting and sanding to avoid inhalation of the particles. MDF which has been encapsulated with primer, paint, etc. reduces health risk still further. We recommend you use a better tool like laser cutting technology to do the cutting job.
1. Use a safer product
For artificial boards, the density board is finally made with adhesive bonding, like wax and resin (glue). Also, formaldehyde is the main component of the adhesive. Therefore, you are most likely to deal with hazardous fume and dust.
Over the last few years, it has become more common for worldwide manufacturers of MDF to lower the amount of added formaldehyde in adhesive bonding. For your safety, you may want to choose the one that uses alternate glues that emit less formaldehyde (eg. Melamine formaldehyde or phenol-formaldehyde) or no added formaldehyde (eg. soy, polyvinyl acetate, or methylene diisocyanate).
Look for CARB (the California Air Resources Board) certified MDF boards and molding with NAF (no added formaldehyde), ULEF (ultra-low emitting formaldehyde) on the label. This will not only avoid your health risk and also provide you with a better quality of goods.
2. Use a suitable laser cutting machine
If you have processed large pieces or amount of wood before, you should notice that skin rash and irritation is the most common health hazard caused by wood dust. Wood dust, especially from hardwood, not only settles in the upper airways causing eye and nasal irritation, nose obstruction, headaches, some particles may even cause nasal and sinus cancer.
If feasible, use a laser cutter to process your MDF. Laser technology can be used on many materials such as acrylic, wood, and paper, etc. As laser cutting is non-contact processing, it simply avoids wood dust. Additionally, its local exhaust ventilation will extract the generating gases at the working part and vent them outside. However, if not feasible, please make sure you use good room ventilation and wear a respirator with cartridges approved for dust and formaldehyde and wear it properly.
Moreover, laser cutting MDF saves the time for sanding or shaving, as the laser is heat treatment, it provides burr-free cutting edge and easy cleaning up the working area after processing.
3. Test your material
Before you get to cut, you should have a thorough knowledge of the materials you are going to cut/engrave and what kind of materials can be cut with a CO2 laser. As MDF is an artificial wood board, the composition of materials is different, the proportion of the material is also different. So, not every kind of MDF board is suitable for your laser machine. Ozon board, water washing board, and poplar board are acknowledged have great laser ability. MimoWork recommends you inquiry experienced carpenters and laser specialists for good suggestions, or you can simply do a quick sample test on your machine.

Working Area (W *L) |
1300mm * 900mm (51.2” * 35.4 ”) |
Software |
Offline Software |
Laser Power |
100W/150W/300W |
Laser Source |
CO2 Glass Laser Tube or CO2 RF Metal Laser Tube |
Mechanical Control System |
Step Motor Belt Control |
Working Table |
Honey Comb Working Table or Knife Strip Working Table |
Max Speed |
1~400mm/s |
Acceleration Speed |
1000~4000mm/s2 |
Package Size |
2050mm * 1650mm * 1270mm (80.7'' * 64.9'' * 50.0'') |
Weight |
620kg |
Working Area (W * L) |
1300mm * 2500mm (51” * 98.4”) |
Software |
Offline Software |
Laser Power |
150W/300W/450W |
Laser Source |
CO2 Glass Laser Tube |
Mechanical Control System |
Ball Screw & Servo Motor Drive |
Working Table |
Knife Blade or Honeycomb Working Table |
Max Speed |
1~600mm/s |
Acceleration Speed |
1000~3000mm/s2 |
Position Accuracy |
≤±0.05mm |
Machine Size |
3800 * 1960 * 1210mm |
Operating Voltage |
AC110-220V±10%,50-60HZ |
Cooling Mode |
Water Cooling and Protection System |
Working Environment |
Temperature:0—45℃ Humidity:5%—95% |
Package Size |
3850mm * 2050mm *1270mm |
Weight |
1000kg |
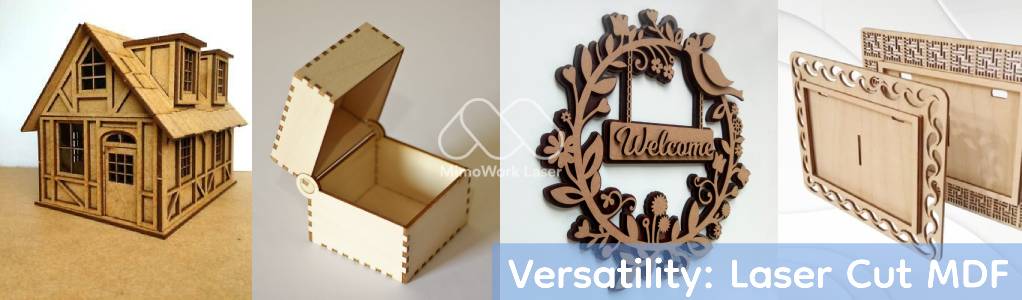
• Furniture
• Home Deco
• Promotional Items
• Signage
• Plaques
• Prototyping
• Architectural Models
• Gifts and Souvenirs
• Interior Design
• Model Making
Tutorial of Laser Cutting & Engraving Wood
Everyone wants their project to be as perfect as possible, but it is always nice to have another alternative that within everyone's reach to purchase. By choosing to use MDF in certain areas of your house, you can save money to use on other things. MDF definitely provides you with a lot of flexibility when it comes to the budget of your project.
Q&As about how to get a perfect cutting result of MDF are just never enough, but lucky for you, now you are one step closer to a great MDF product. Hope you learned something new today! If you have some more specific questions, please feel free to ask your laser technical friend MimoWork.com.
© Copyright MimoWork, All Rights Reserved.
Who are we:
MimoWork Laser is a results-oriented corporation bringing 20-year deep operational expertise to offer laser processing and production solutions to SMEs (small and medium-sized enterprises) in and around clothing, auto, ad space.
Our rich experience of laser solutions deeply rooted in the advertisement, automotive & aviation, fashion & apparel, digital printing, and filter cloth industry allows us to accelerate your business from strategy to day-to-day execution.
We believe that expertise with fast-changing, emerging technologies at the crossroads of manufacture, innovation, technology, and commerce are a differentiator. Please contact us: Linkedin Homepage and Facebook homepage or info@mimowork.com
More FAQs of Laser Cut MDF
1. Can you cut MDF with a laser cutter?
Yes, you can cut MDF with a laser cutter. MDF (Medium Density Fiberboard) is commonly cut with CO2 laser machines. Laser cutting provides clean edges, precise cuts, and smooth surfaces. However, it can produce fumes, so proper ventilation or an exhaust system is essential.
2. How to clean laser cut MDF?
To clean laser-cut MDF, follow these steps:
Step 1. Remove Residue: Use a soft brush or compressed air to remove any loose dust or debris from the MDF surface.
Step 2. Clean the Edges: The laser-cut edges may have some soot or residue. Wipe the edges gently with a damp cloth or a microfiber cloth.
Step 3. Use Isopropyl Alcohol: For stubborn marks or residue, you can apply a small amount of isopropyl alcohol (70% or higher) to a clean cloth and gently wipe the surface. Avoid using too much liquid.
Step 4. Dry the Surface: After cleaning, ensure the MDF dries completely before further handling or finishing.
Step 5. Optional - Sanding: If needed, lightly sand the edges to remove any excess burn marks for a smoother finish.
This will help maintain the appearance of your laser-cut MDF and prepare it for painting or other finishing techniques.
3. Is MDF safe to laser cut?
Laser cutting MDF is generally safe, but there are important safety considerations:
Fumes and Gases: MDF contains resins and glues (often urea-formaldehyde), which can release harmful fumes and gases when burned by the laser. It’s crucial to use proper ventilation and a fume extraction system to prevent inhalation of toxic fumes.
Fire Hazard: Like any material, MDF can catch fire if the laser settings (such as power or speed) are incorrect. It’s important to monitor the cutting process and adjust settings accordingly. About how to set laser parameters for laser cutting MDF, please talk with our laser expert. After you purchasing the MDF laser cutter, our laser salesman and laser expert will offer you a detailed operation guide and maintenance tutorial.
Protective Equipment: Always wear safety gear such as goggles and ensure the workspace is clear of flammable materials.
In summary, MDF is safe to laser cut when proper safety precautions are in place, including adequate ventilation and monitoring of the cutting process.
4. Can you laser engrave MDF?
Yes, you can laser engrave MDF. Laser engraving on MDF creates precise, detailed designs by vaporizing the surface layer. This process is commonly used for personalizing or adding intricate patterns, logos, or text to MDF surfaces.
Laser engraving MDF is an effective method for achieving detailed and high-quality results, especially for crafts, signage, and personalized items.
Any Questions about Laser Cutting MDF or Learn More about MDF Laser Cutter
Post time: Nov-04-2024