Scintillation Crystal
(Sub Surface Laser Engraving)
Scintillation-based detectors, using pixelated inorganic crystal scintillators, are widely used for particle and radiation detection, including in positron emission tomography (PET) scanners.
By adding light-guiding features to the crystal, the spatial resolution of the detector can be improved to the millimeter scale, enhancing the overall resolution of the tomograph.
However, the traditional method of physically pixelating the crystals is a complex, expensive, and laborious process. Additionally, the packing fraction and sensitivity of the detector can be compromised due to the non-scintillating reflective materials used.
You can view the Original Research Paper Here. (From ResearchGate)
Subsurface Laser Engraving for Scintillation Crystal
An alternative approach is the use of subsurface laser engraving (SSLE) techniques for scintillator crystals.
By focusing a laser inside the crystal, the heat generated can create a controlled pattern of microcracks that act as reflective structures, effectively creating light-guiding pixels without the need for physical separation.
1. No physical pixelation of the crystal is required, reducing complexity and cost.
2. The optical characteristics and geometry of the reflective structures can be precisely controlled, enabling the design of custom pixel shapes and sizes.
3. Readout and detector architecture remain the same as for standard pixelated arrays.
Laser Engraving Process (SSLE) for Scintillator Crystal
The SSLE engraving process involves the following steps:
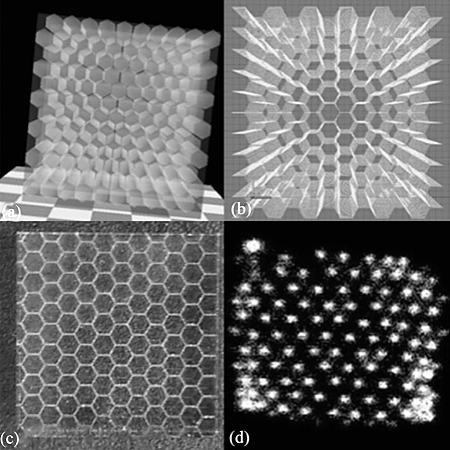
1. The Design:
Simulation and design of the desired pixel architecture, including dimensions and optical characteristics.
2. The CAD Model:
Creation of a detailed CAD model of the microcrack distribution, based on the simulation results and laser engraving specifications.
3. Start Engraving:
Actual engraving of the LYSO crystal using the laser system, guided by the CAD model.
SSLE Development Procedure: (A)Simulation Model, (B)CAD Model, (C) Engraved LYSO, (D)Field Flood Diagram
4. Result Evaluation:
Evaluation of the engraved crystal's performance using a flood field image and Gaussian fitting to assess the pixel quality and spatial resolution.
Subsurface Laser Engraving EXPLAINED in 2 Minutes
The subsurface laser engraving technique for scintillator crystals offers a transformative approach to the pixelation of these materials.
By providing precise control over the optical characteristics and geometry of the reflective structures, this method enables the development of innovative detector architectures with enhanced spatial resolution and performance, all without the need for complex and costly physical pixelation.
Want to Know More about:
Subsurface Laser Engraving Scintillation Crystal?
Findings for SSLE Scintillation Crystal
1. Improved Light Yield
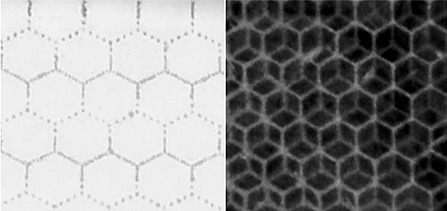
Left: Engraved Surface Reflectivity Asymmetry DoI Overview.
Right: Pixel Displacement DoI.
The comparison of pulses between subsurface laser engraved (SSLE) arrays and conventional arrays demonstrates a far better light yield for SSLE.
This is likely due to the absence of plastic reflectors between the pixels, which can cause optical mismatching and photon loss.
The improved light yield means more light for the same energy pulses, making SSLE a desirable characteristic.
2. Enhanced Timing Behavior
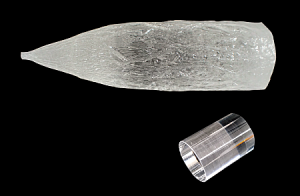
A Picture of Scintillation Crystal
Crystal length has a detrimental effect on timing, which is crucial for Positron Emission Tomography (PET) applications.
However, the higher sensitivity of SSLE crystals allows for the use of shorter crystals, which can improve the timing behavior of the system.
Simulations have also suggested that different pixel shapes, such as hexagonal or dodecagonal, may lead to better light-guiding and timing performance, similar to the principles of optical fibers.
3. Cost-Effective Advantages
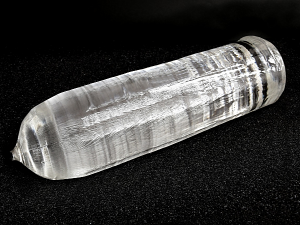
A Picture of Scintillator Crystal
Compared to monolithic blocks, the price of SSLE crystals can be as low as one-third of the cost of the corresponding pixelated array, depending on the pixel dimensions.
Additionally, the higher sensitivity of SSLE crystals allows for the use of shorter crystals, further reducing the overall cost.
The SSLE technique requires lower laser power compared to laser cutting, allowing for less expensive SSLE systems compared to laser melting or cutting facilities.
The initial investment in infrastructure and training for SSLE is also significantly lower than the cost of developing a PET detector.
4. Design Flexibility and Customization
The process of engraving SSLE crystals is not time-consuming, with an approximate 15 minutes needed to engrave a 12.8x12.8x12 mm, 3-crystal array.
The flexible nature, cost-effectiveness, and ease of preparation of SSLE crystals, along with their superior packing fraction, compensate for the slightly inferior spatial resolution compared to standard pixelated arrays.
Non-Conventional Pixel Geometries
SSLE allows for the exploration of non-conventional pixel geometries, enabling the scintillating pixels to be precisely matched to the specific requirements of each application, such as collimators or the dimensions of silicon photomultiplier pixels.
Controlled Light-Sharing
Controlled light-sharing can be achieved through precise manipulation of the optical characteristics of the engraved surfaces, facilitating further miniaturization of gamma detectors.
Exotic Designs
Exotic designs, such as Voronoi tessellations, can be easily engraved within monolithic crystals. Furthermore, a random distribution of pixel sizes can enable the introduction of compressed sensing techniques, taking advantage of the extensive light sharing.
Machines for Subsurface Laser Engraving
The heart of Subsurface Laser creation lies in the laser engraving machine. These machines utilize a high-powered green laser, specifically designed for subsurface laser engraving in crystal.
The One & Only Solution you will ever need for Subsurface Laser Engraving.
Supports 6 Different Configurations
From Small Scale Hobbyist to Large Scale Production
Repeated Location Accuracy at <10μm
Surgical Precision for 3D Laser Carving
3D Crystal Laser Engraving Machine (SSLE)
For Subsurface Laser Engraving, precision is crucial for creating detailed and intricate engravings. The laser's focused beam precisely interacts with the crystal's internal structure, creating the 3D image.
Portable, Accurate & Advanced
Compact Laser Body for SSLE
Shock-Proof & Safer for Beginners
Fast Crystal Engraving up to 3600 points/second
Great Compatibility in Design