レーザークリーニングステンレス鋼
レーザークリーニングは、さまざまな種類のステンレス鋼を洗浄するための効果的な方法です。
しかし、それは材料特性を完全に理解する必要があります
レーザーパラメーターの慎重な制御
最良の結果を確実にするため
変色や表面損傷などの潜在的な問題を避けてください。
レーザークリーニングとは何ですか?
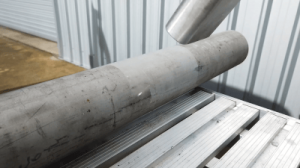
ハンドヘルドレーザークリーニング酸化物層は、ステンレス鋼管を層化します
レーザークリーニングは、多目的で効果的な技術です
これは、高エネルギーレーザービームを利用します
さまざまな表面から汚染物質、酸化物、およびその他の不要な材料を除去する。
この技術は、さまざまな業界で多数のアプリケーションを発見しました。
レーザークリーニングの重要な用途の1つは、溶接と金属製造の分野にあります。
溶接プロセスの後、溶接領域はしばしば変色と酸化を発症します、
最終製品の外観とパフォーマンスに悪影響を与える可能性があります。
レーザークリーニングは、これらの不要な副産物を効果的に除去できます。
さらなる処理または仕上げのために表面を準備します。
レーザークリーニングがステンレス鋼の洗浄に役立つ方法
ステンレス鋼の溶接クリーニング:
特に、ステンレス鋼は、レーザークリーニングから大きな恩恵を受ける材料です。
高エネルギーレーザービームは、溶接プロセス中にステンレス鋼の溶接に形成される厚い黒い「スラグ」を効率的に除去できます。
このクリーニングプロセスは、溶接の全体的な外観と品質を改善し、滑らかで均一な表面を確保するのに役立ちます。
効果的で自動化された、環境に優しい
ステンレス鋼の溶接のレーザー洗浄は、化学物質や機械的洗浄などの従来の洗浄方法よりもいくつかの利点を提供します。
既存の生産ラインに簡単に統合できる、クリーンで自動化された一貫したプロセスです。
レーザークリーニングプロセスは、1分あたり1〜1.5メートルの範囲のクリーニング速度を実現できます。これは、典型的な溶接速度と一致し、シームレスな統合になります。
さらに、レーザークリーニングは、化学物質の手動処理または研磨ツールの使用の必要性を排除します。
これは時間がかかり、危険であり、望ましくない副産物を生成する可能性があります。
これにより、職場の安全性が向上し、メンテナンス要件が削減され、より効率的な生産プロセスが生じます。
ステンレス鋼をきれいにしてもらえますか?
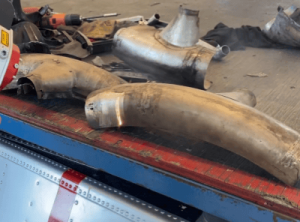
レーザークリーニングステンレス鋼パイプ
レーザークリーニングは、さまざまな種類のステンレス鋼を洗浄するための効果的な方法です。
しかし、特定のステンレス鋼合金とその特性を慎重に検討する必要があります。
レーザークリーニングオーステナイトステンレス鋼:
これらの鋼は、顔中心の立方体構造を持ち、耐食性が非常に高い、
しかし、彼らはさまざまな程度に働くことができます。
例には、304や316などの300シリーズのステンレス鋼が含まれます。
レーザークリーニングマルテンサイトステンレス鋼:
これらの鋼は、熱処理によって硬化し、和らげることができます。
それらは一般にオーステナイト鋼よりも困難ではありませんが、ニッケルの含有量が少ないため、より機密性があります。
400シリーズのステンレス鋼は、このカテゴリに分類されます。
レーザークリーニングフェライトステンレス鋼:
400シリーズのこのサブグループは熱処理可能であり、過度の作業なしで硬化します。
例には、刃によく使用される430ステンレス鋼が含まれます。
レーザークリーニングステンレス鋼:何を探していますか
レーザークリーニングステンレス鋼の場合、
変色(黄色または茶色の染色の形成)または表面への損傷の可能性に留意することが重要です。
レーザー出力、パルス周波数、制御された大気(窒素シールドガスなど)などの要因はすべて、洗浄プロセスの品質に影響を与える可能性があります。
レーザーパラメーターとガス流量の慎重な監視と調整は、この問題を軽減するのに役立ちます。
別の考慮事項は次のとおりですレーザー洗浄プロセス中のステンレス鋼の表面の作業硬化または歪みの可能性。
ステンレス鋼の最も効果的なレーザークリーニングを実現するために
適切な設定を提供できます
ステンレス鋼をきれいにする最も効果的な方法は何ですか?
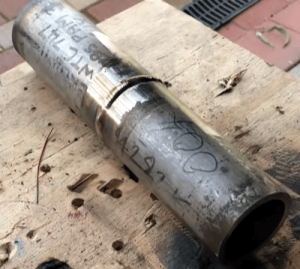
ステンレス鋼管のレーザークリーニング錆とマーク
ネタバレアラート:レーザークリーニングです
ステンレス鋼を掃除する一般的な方法(効果的ではありませんが)
一般的な方法の1つは、軽度の洗剤ソリューションを使用することです。
これは軽いクリーニングに効果的ですが、
頑固な錆や汚れを除去するには十分ではないかもしれません。
別のアプローチは、ステンレススチールクリーナーを適用することです。
汚れや汚れをきれいにするのに役立ちます。
ただし、これらのクリーナーは、より深刻な錆や縮尺の蓄積に対処するのに十分なほど深く浸透しない場合があります。
一部の人々は、白酢や重曹を使用してステンレス鋼をきれいにしようとします。
これらの自然なクリーナーは、特定の種類の汚れを除去するのに効果的ですが、
また、それらはあまりにも研磨性があり、ステンレス鋼のブラシ仕上げを潜在的に損傷する可能性があります。
対照的に、レーザークリーニングはどうですか?
レーザークリーニングはです非常に正確で、特定の領域をターゲットにすることができます下にある金属を損傷することなく。
手動のスクラビングや化学洗浄と比較して、レーザークリーニングもより効率的で一貫性。
水やその他の洗浄ソリューションの必要性を排除しますそれは残留物や水の斑点を残すことができます。
さらに、レーザークリーニングはaです非接触法、つまり、ステンレス鋼の表面に物理的に触れないことを意味します。
レーザークリーニングステンレス鋼の錆
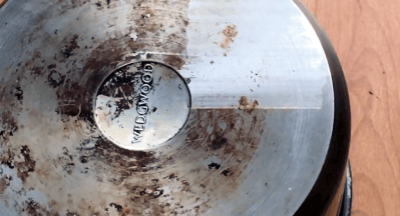
ステンレススチールフライパンからのレーザークリーニングラスト
レーザークリーニングは、ステンレス鋼の表面からさびやスケールを除去するための非常に効果的で効率的な方法となっています。
この非攻撃的で非接触洗浄プロセスは、従来の錆除去技術よりもいくつかの利点を提供します。
レーザークリーニングステンレス鋼の錆のための見落とされたヒント
正しい設定はすべての違いをもたらします
基礎となる材料への損傷を避けるために、ステンレス鋼の特定のタイプと厚さにレーザーパラメーター(電源、パルス期間、繰り返し速度)が最適化されていることを確認してください。
一貫性を監視します
洗浄プロセスを慎重に監視して、過度の暴露を避け、変色やその他の表面欠陥につながる可能性があります。
より良い結果を得るためにガスをシールドします
窒素やアルゴンなどのシールドガスの使用を検討して、洗浄プロセス中の新しい酸化物の形成を防ぎます。
定期的にメンテナンスと適切な安全対策
レーザーシステムを定期的に維持および調整して、一貫した信頼性の高いパフォーマンスを確保します。
目の保護や換気などの適切な安全対策を実施し、
洗浄プロセス中に生成されたレーザー放射および煙または微粒子からオペレーターを保護する。
レーザークリーニングステンレス鋼のアプリケーション
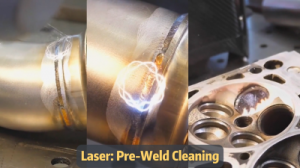
レーザークリーニングステンレス溶接
レーザー技術を使用して、さまざまな種類の木材を効果的に洗浄できます。
レーザークリーニングに最も適した木材は、色が暗すぎたり反射したりしないものです。
溶接の準備とクリーニング
レーザークリーニングは、ステンレス鋼の溶接の準備と洗浄に非常に役立ちます。
溶接プロセス中に形成される濃厚で黒いスラグを簡単に削除できます。
その後の仕上げ操作のために表面を準備します。
レーザークリーニングは、1〜1.5 m/minの洗浄速度を達成できます
一般的な溶接速度を一致させ、既存の生産ラインに簡単に統合できるようにします。
表面プロファイリング
製造されたステンレス鋼部品に保護コーティングを適用する前に、
表面は清潔で、油、グリース、スケール、酸化物層などのすべての汚染物質がない必要があります。
レーザークリーニングは非拡大し、
基礎となる材料を損傷することなく、これらの表面を徹底的にプロファイルして準備する非接触方法。
接着剤の結合準備
ステンレス鋼の強力で耐久性のある接着結合を確保するため、
酸化物、グリース、およびその他の汚染物質を除去することにより、表面は慎重に準備する必要があります。
レーザークリーニングは、基板を傷つけることなく表面を正確に変更できるため、このアプリケーションに最適です。
これにより、結合強度が優れており、耐食性が改善されます。
溶接残基除去
また、レーザークリーニングを使用して、完成したステンレス鋼の溶接ジョイントから残留フラックス、酸化物材料、および熱染色を除去することもできます。
これにより、溶接継ぎ目をパッシブ化し、耐食性が増加します。
レーザーの調整可能な波長とパワーにより、広範囲の材料の厚さにわたって正確な処理が可能になります。
部分的なデコ装置
レーザークリーニングは、ステンレス鋼の表面からの塗料またはコーティングの部分的な除去に効果的です。
ファラデーケージ、結合ポイント、電磁互換性を作成するなど。
レーザーは、基礎となる基質を損傷することなく、目的の領域のコーティングを正確に標的とすることができます。
非連続レーザー出力と高いピークレーザー出力により、パルスレーザークリーナーはより省エネであり、細かい部品の洗浄に適しています。
調整可能なパルスレーザーは、柔軟性があり、錆の除去、塗料の除去、剥離コーティング、酸化物やその他の汚染物質の除去に役立ちます。
汎用性調整可能な電力パラメーターを介して
低い運用およびメンテナンスコスト
非接触クリーニング木材の損傷を最小限に抑えます
パルスレーザークリーナーとは異なり、連続波レーザークリーニングマシンは、より高い速度とより大きなクリーニングカバースペースを意味する、より高い電力出力に到達する可能性があります。
これは、屋内や屋外の環境に関係なく、非常に効率的で安定した洗浄効果により、造船、航空宇宙、自動車、金型、パイプラインフィールドの理想的なツールです。
高出力産業用設定用
より高い効率濃厚な錆とコーティング用
直感的なオペレーティングシステムポイントアンドクリーンエクスペリエンス